Customer Company Size
Mid-size Company
Region
- Africa
Country
- South Africa
Product
- Wonderware System Platform
- Wonderware InTouch HMI
- Wonderware Historian
- Wonderware Historian Clients
Tech Stack
- PLC
- SCADA
Implementation Scale
- Enterprise-wide Deployment
Impact Metrics
- Cost Savings
- Productivity Improvements
- Customer Satisfaction
Technology Category
- Platform as a Service (PaaS) - Application Development Platforms
- Platform as a Service (PaaS) - Data Management Platforms
Applicable Industries
- Food & Beverage
Applicable Functions
- Discrete Manufacturing
- Quality Assurance
Use Cases
- Process Control & Optimization
- Real-Time Location System (RTLS)
Services
- System Integration
- Software Design & Engineering Services
About The Customer
Woodlands Dairy is a dairy company located in Humansdorp, South Africa. The company is subject to increasingly close scrutiny in the supply of primary foodstuffs such as dairy products. To stay in business profitably in the dairy industry means the consistent provision of quality products and unswerving compliance with ISO standards. The company had a variety of PLCs and no PLC or SCADA standards. They needed a centralized environment for process data logging which would allow them to analyze data in real-time and produce reports. They also needed flexible security facilities that would allow operator access only to designated areas of the plant. Finally, they needed system redundancy to provide for uninterrupted operation as well as the ability to develop and deploy solutions from a central point for ease of maintenance.
The Challenge
Woodlands Dairy faced the challenge of integrating a second-hand powder plant from Denmark with an outdated control system into their existing operations. The control system was not suitable for the modifications required to adapt the process to Woodlands Dairy’s specifications. This prompted the company to consider how this expansion could be integrated with the rest of the site. The company needed a single platform that could integrate all the disparate plants on site while preserving past investments in expensive assets and legacy systems while making provision for future expansion. They also needed a centralized environment for process data logging which would allow them to analyze data in real-time and produce reports. The system also needed to comply with ISO 22000 standards and the project had to be completed without any interruptions to production.
The Solution
The solution to Woodlands Dairy's challenges was the Wonderware System Platform consisting of the Application Server, InTouch HMI, Historian and Historian Clients trending and reporting tool. The platform was chosen for its universal data connectivity, object-oriented technology, distributed system, easy report creation and retrieval of historical data, full redundancy, scalability, and the level of support available in South Africa. The total implementation took about six months, half of which was spent on the new powder plant which was commissioned first. The standards developed for the powder plant were rolled out for these projects. Other process areas were also upgraded and these included a new Clean in Place (CIP) Station, a new cream pasteurizer/butter plant, an upgrade to the milk pasteurizer, new pasteurized milk silo and milk lines, new pasteurized cream silo and a new milk reception area with its own CIP station.
Operational Impact
Quantitative Benefit
Case Study missing?
Start adding your own!
Register with your work email and create a new case study profile for your business.
Related Case Studies.

Case Study
The Kellogg Company
Kellogg keeps a close eye on its trade spend, analyzing large volumes of data and running complex simulations to predict which promotional activities will be the most effective. Kellogg needed to decrease the trade spend but its traditional relational database on premises could not keep up with the pace of demand.
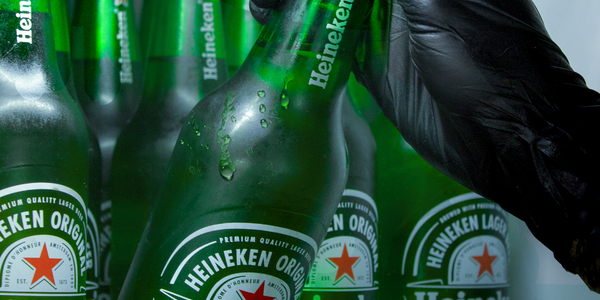
Case Study
HEINEKEN Uses the Cloud to Reach 10.5 Million Consumers
For 2012 campaign, the Bond promotion, it planned to launch the campaign at the same time everywhere on the planet. That created unprecedented challenges for HEINEKEN—nowhere more so than in its technology operation. The primary digital content for the campaign was a 100-megabyte movie that had to play flawlessly for millions of viewers worldwide. After all, Bond never fails. No one was going to tolerate a technology failure that might bruise his brand.Previously, HEINEKEN had supported digital media at its outsourced datacenter. But that datacenter lacked the computing resources HEINEKEN needed, and building them—especially to support peak traffic that would total millions of simultaneous hits—would have been both time-consuming and expensive. Nor would it have provided the geographic reach that HEINEKEN needed to minimize latency worldwide.
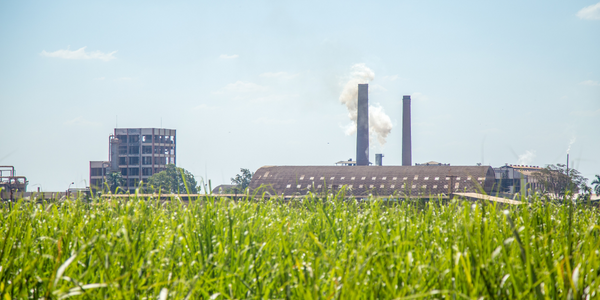
Case Study
Energy Management System at Sugar Industry
The company wanted to use the information from the system to claim under the renewable energy certificate scheme. The benefit to the company under the renewable energy certificates is Rs 75 million a year. To enable the above, an end-to-end solution for load monitoring, consumption monitoring, online data monitoring, automatic meter data acquisition which can be exported to SAP and other applications is required.
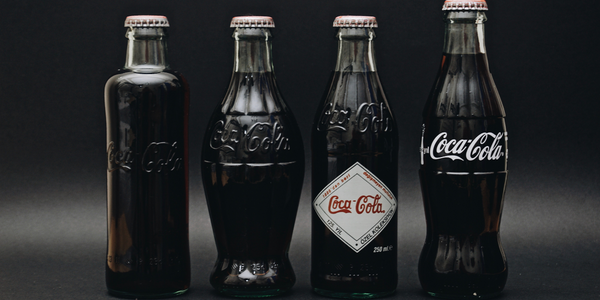
Case Study
Coca Cola Swaziland Conco Case Study
Coco Cola Swaziland, South Africa would like to find a solution that would enable the following results: - Reduce energy consumption by 20% in one year. - Formulate a series of strategic initiatives that would enlist the commitment of corporate management and create employee awareness while helping meet departmental targets and investing in tools that assist with energy management. - Formulate a series of tactical initiatives that would optimize energy usage on the shop floor. These would include charging forklifts and running cold rooms only during off-peak periods, running the dust extractors only during working hours and basing lights and air-conditioning on someone’s presence. - Increase visibility into the factory and other processes. - Enable limited, non-intrusive control functions for certain processes.
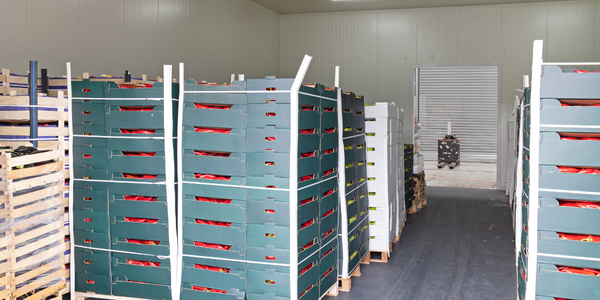
Case Study
Temperature Monitoring for Restaurant Food Storage
When it came to implementing a solution, Mr. Nesbitt had an idea of what functionality that he wanted. Although not mandated by Health Canada, Mr. Nesbitt wanted to ensure quality control issues met the highest possible standards as part of his commitment to top-of-class food services. This wish list included an easy-to use temperature-monitoring system that could provide a visible display of the temperatures of all of his refrigerators and freezers, including historical information so that he could review the performance of his equipment. It also had to provide alert notification (but email alerts and SMS text message alerts) to alert key staff in the event that a cooling system was exceeding pre-set warning limits.
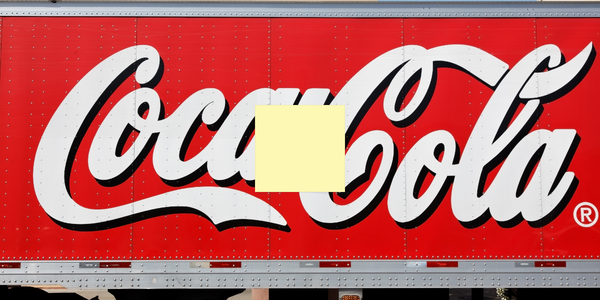
Case Study
Coca-Cola Refreshments, U.S.
Coca-Cola Refreshments owns and manages Coca-Cola branded refrigerators in retail establishments. Legacy systems were used to locate equipment information by logging onto multiple servers which took up to 8 hours to update information on 30-40 units. The company had no overall visibility into equipment status or maintenance history.