Cobuilder
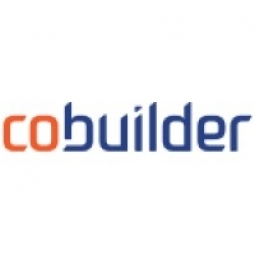
Overview
HQ Location
Norway
|
Year Founded
1997
|
Company Type
Private
|
Revenue
$10-100m
|
Employees
51 - 200
|
Website
|
Company Description
Cobuilder offers an IT platform that employs all relevant international standards for data management to help construction industry actors exploit the potential of product data.
Supplier missing?
Start adding your own!
Register with your work email and create a new supplier profile for your business.
Case Studies.
Case Study
Wienerberger AG creates an enterprise-level data model in order to ensure consistency and standardisation of the product data managed within the organisation’s IT environment
Wienerberger AG identified the need to provide relevant data to their customers more effectively within the software they use (BIM authoring software) and improve the customer journey across all touchpoints. The company's data stewards were faced with numerous challenges concerning the consistency and standardisation of product (systems, materials etc.) data across the whole group and its brands. In order to improve the quality of their data services, Wienerberger AG set an objective to standardise data internally, and decided to introduce an enterprise Product Information Management (PIM) system which would be the single source of data for all their clients. However, a traditional PIM did not fully meet their needs. They needed a solution that also could ‘translate’ data to the particular needs of users within different markets and across different software, without maintaining data duplicates and numerous local ‘silo’ databases.
Case Study
Pipelife Norway adopts a standardised approach to product data management by implementing Wienerberger AG’s new enterprise-level data model
Pipelife Norge, a subsidiary of Wienerberger AG, was one of the first to implement Wienerberger’s enterprise-level data model. The model is aimed at adopting a systematic and centralised approach to product data management at enterprise-level, as the digital readiness across the entire group varies significantly from brand to brand and company to company. Pipelife Norge also reported the increasing demand, especially in their home market, for relevant and accurate product data that can be used across the supply chain by various software and actors. One of the main challenges was that most of Pipelife’s product information was stored in siloed systems and file formats that hindered the flow of information. In addition, Pipelife’s web-catalog was maintained by the respective Product Managers responsible for the different product lines, which sometimes led to inconsistencies in the quality and richness of the product information.
Case Study
NCC introduces a new data management process to enable paperless, efficient flow of data in internal systems and streamlined exchange of information with suppliers
NCC, a leading construction company, was facing challenges in implementing a paperless workflow related to the specification and selection of building elements used in internal processes and in the procurement process. The use of different words and definitions within the industry, as well as different data structure and language in systems, made it time-consuming to secure the quality of the data collected and exchanged. The difference in data models made it difficult to get different systems to process data in an efficient way.