eFlex Systems
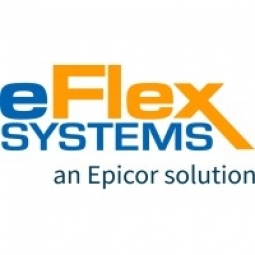
Overview
HQ Location
United States
|
Year Founded
1988
|
Company Type
Private
|
Revenue
< $10m
|
Employees
1,001 - 10,000
|
Website
|
Twitter Handle
|
Company Description
eFlex Systems, an Epicor solution, is a leader in Advanced Manufacturing technology and optimization solutions with a suite of battle-tested MES products. It strives to empower manufacturers to join the Industry 4.0 movement with cost effective, easy-to-use solutions, permitting them to become agile, data driven and best in class.
Supplier missing?
Start adding your own!
Register with your work email and create a new supplier profile for your business.
Case Studies.
Case Study
Line Changeover Comparison Study: Flexible Assembly Line vs Highly Automated Fixed Tooling
The global automotive manufacturer in this case study had two manufacturing plants producing the same V6 engine with similar production rates and model variants. One plant used the eFlex Assembly architecture, while the other used a highly automated fixed architecture. Both lines had over 100 workstations and up to 200 model variants. Both sites needed to re-rate production and introduce new models. The challenge was that the highly automated fixed tooling line was inflexible, costly, and time-consuming to change. This resulted in lost opportunities and a lack of competitiveness in the market. The manufacturer needed a solution that would allow for rapid changes in production requirements, configurability, distributed control, and plug-and-play capabilities.
Case Study
Large Automotive Manufacturer Integrates eFlex Vision with Cognex Cameras to Optimize Vision Inspection System, Improve Part Quality and Reduce Warranty Costs
The customer, a global automobile manufacturer, was facing challenges with their existing transmission manufacturing process. The detailed nature of automotive transmission manufacturing and the high cost of errors made it crucial to ensure high levels of quality and minimize warranty costs. Prior to implementing a vision inspection system, the transmission line and all previous assembly lines were managed in a manner that was inefficient and costly. Images were stored on 50 PCs scattered throughout the plant, requiring engineers to visit each storage area to retrieve images associated to a particular serial number. This incurred excessive PC life-cycle cost and labor due to the initial investment, and ongoing OS patches, virus updates and hardware failures. The PCs failed to integrate and store images reliably, resulting in lost images. The system also lacked diagnostic capabilities, such as alerts when quality was degrading, as well as data and reporting capabilities.
Case Study
Market Change Results in Lost Sales Due to “Inflexible” Fixed Tooling Assembly Systems
A global automotive manufacturer was facing a sudden shift in market demand due to changes in fuel prices. The demand for 4-cylinder engines increased overnight, while the demand for 6-cylinder engines dropped. The manufacturer's assembly lines, which were highly automated and fixed for 4-and 6-cylinder engine assembly, were not flexible enough to adapt to this change. The 4-cylinder line was running around the clock but could not increase its capacity beyond its original design capabilities. The 6-cylinder line was meeting production requirements by 10 am and sitting idle for the rest of the day. This inflexibility resulted in lost sales opportunities.