Customer Company Size
SME
Region
- Europe
Country
- United Kingdom
Product
- DocuWare Solution
- Destiny Digital Pen
- Destiny Digital Pad
- Solarvista software
Tech Stack
- Bluetooth
- Infrared Camera
- Digital Paper Technology
- Server Technology
Impact Metrics
- Productivity Improvements
- Cost Savings
- Customer Satisfaction
Technology Category
- Application Infrastructure & Middleware - Data Exchange & Integration
Applicable Functions
- Field Services
- Human Resources
Use Cases
- Remote Asset Management
- Inventory Management
Services
- System Integration
- Software Design & Engineering Services
About The Customer
Serviceline is a company founded in 1989 that works closely with the food service industry to maintain kitchen/catering equipment and appliances. The company provides installation, warranty, and emergency service support for all major makes of commercial catering equipment found in establishments like restaurants, hospitals, and stadiums. Serviceline has 173 employees, of which 120 are engineers. These engineers are equipped with a digital pen and pad to complete their Field Service Reports (FSRs). The company has won the annual International Safety Award consecutively since 2005, which may be due in part to its well-organised documentation processes.
The Challenge
Serviceline, a company that provides maintenance and repair services for kitchen/catering equipment, was facing several challenges. The company was dealing with a high volume of paper-based Field Service Reports (FSRs) that were sent in by mail, taking at least two to three days to arrive. These reports then had to be manually indexed by a Job Manager. This process was time-consuming and inefficient. Additionally, the company was required to retain information for its customers and suppliers, which led to a need for a large amount of physical storage space. The company was also looking to improve its customer service and invoice control processes.
The Solution
Serviceline implemented a solution that combined the DocuWare Solution, a Destiny Digital Pen and Pad, and Solarvista software. The digital pen and pad allowed engineers to complete their FSRs and send them in electronically, significantly reducing the time it took for these reports to be received and processed. The DocuWare Solution served as a repository for these reports, as well as other documents such as HR files, purchase orders, and invoices. The Solarvista software was used for correct indexing and tracking of labour hours. The solution also allowed for photos of old parts to be taken and emailed to the FSR, ensuring that exact replacement parts could be purchased right away. The solution was implemented across the entire company.
Operational Impact
Quantitative Benefit
Case Study missing?
Start adding your own!
Register with your work email and create a new case study profile for your business.
Related Case Studies.
.png)
Case Study
Improving Vending Machine Profitability with the Internet of Things (IoT)
The vending industry is undergoing a sea change, taking advantage of new technologies to go beyond just delivering snacks to creating a new retail location. Intelligent vending machines can be found in many public locations as well as company facilities, selling different types of goods and services, including even computer accessories, gold bars, tickets, and office supplies. With increasing sophistication, they may also provide time- and location-based data pertaining to sales, inventory, and customer preferences. But at the end of the day, vending machine operators know greater profitability is driven by higher sales and lower operating costs.
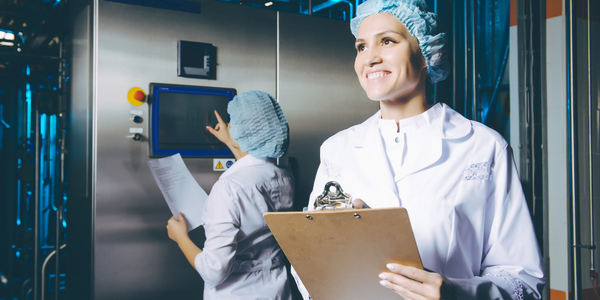
Case Study
Remote Wellhead Monitoring
Each wellhead was equipped with various sensors and meters that needed to be monitored and controlled from a central HMI, often miles away from the assets in the field. Redundant solar and wind generators were installed at each wellhead to support the electrical needs of the pumpstations, temperature meters, cameras, and cellular modules. In addition to asset management and remote control capabilities, data logging for remote surveillance and alarm notifications was a key demand from the customer. Terra Ferma’s solution needed to be power efficient, reliable, and capable of supporting high-bandwidth data-feeds. They needed a multi-link cellular connection to a central server that sustained reliable and redundant monitoring and control of flow meters, temperature sensors, power supply, and event-logging; including video and image files. This open-standard network needed to interface with the existing SCADA and proprietary network management software.
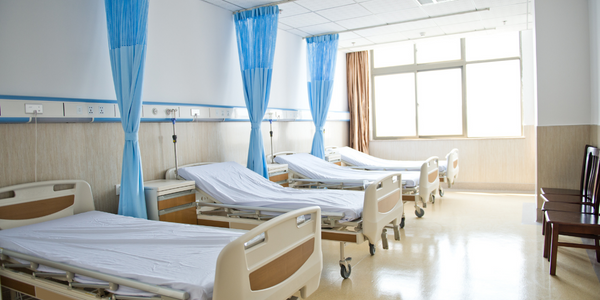
Case Study
Hospital Inventory Management
The hospital supply chain team is responsible for ensuring that the right medical supplies are readily available to clinicians when and where needed, and to do so in the most efficient manner possible. However, many of the systems and processes in use at the cancer center for supply chain management were not best suited to support these goals. Barcoding technology, a commonly used method for inventory management of medical supplies, is labor intensive, time consuming, does not provide real-time visibility into inventory levels and can be prone to error. Consequently, the lack of accurate and real-time visibility into inventory levels across multiple supply rooms in multiple hospital facilities creates additional inefficiency in the system causing over-ordering, hoarding, and wasted supplies. Other sources of waste and cost were also identified as candidates for improvement. Existing systems and processes did not provide adequate security for high-cost inventory within the hospital, which was another driver of cost. A lack of visibility into expiration dates for supplies resulted in supplies being wasted due to past expiry dates. Storage of supplies was also a key consideration given the location of the cancer center’s facilities in a dense urban setting, where space is always at a premium. In order to address the challenges outlined above, the hospital sought a solution that would provide real-time inventory information with high levels of accuracy, reduce the level of manual effort required and enable data driven decision making to ensure that the right supplies were readily available to clinicians in the right location at the right time.