Advance Auto Parts Turns to JDA to Increase Product Availability — Leading to Both Revenue and Service Gains
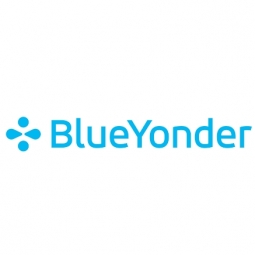
Customer Company Size
Large Corporate
Region
- America
Country
- United States
Product
- JDA Advanced Store Replenishment
- JDA Advanced Warehouse Replenishment
- JDA Category Knowledge Base
- JDA Floor Planning
- JDA Space Automation
- JDA Space Planning
- JDA Transportation Management
- JDA Warehouse Labor Management
- JDA Warehouse Management
Tech Stack
- Supply Chain Management Software
- Warehouse Management System
- Transportation Management System
- Labor Management System
- Space Planning Software
Implementation Scale
- Enterprise-wide Deployment
Impact Metrics
- Customer Satisfaction
- Productivity Improvements
- Revenue Growth
Technology Category
- Functional Applications - Enterprise Resource Planning Systems (ERP)
- Functional Applications - Transportation Management Systems (TMS)
- Functional Applications - Warehouse Management Systems (WMS)
Applicable Industries
- Retail
- Automotive
Applicable Functions
- Logistics & Transportation
- Warehouse & Inventory Management
Use Cases
- Inventory Management
- Supply Chain Visibility
- Warehouse Automation
Services
- System Integration
- Training
About The Customer
Advance Auto Parts is a leading automotive aftermarket retailer of parts, accessories, batteries and maintenance items. The company serves both the do-it-yourself consumer and professional installer. With more than 3,900 stores across the United States, Advance serves these locations via a strategic network of distribution centers (DCs) focused on delivering excellent service. In recent years, Advance’s retail segment has shifted from do-it-yourself consumers to do-it-for-me commercial customers, placing added pressure on Advance to ensure immediate product availability. The company was already using JDA Software’s solutions for space and category management, as well as replenishment, to manage its nationwide supply chain when it decided to embark on a supply chain transformation project.
The Challenge
Advance Auto Parts, a leading automotive aftermarket retailer, was facing a shift in its retail segment from do-it-yourself consumers to do-it-for-me commercial customers. This shift placed added pressure on Advance to ensure immediate product availability. The company was already using JDA Software’s solutions for space and category management, as well as replenishment, to manage its nationwide supply chain when it decided to embark on a supply chain transformation project. In 2010, Advance made a strategic decision to expand the role of these solutions, add physical supply chain infrastructure, and incorporate new technology solutions and business processes to optimize its warehouse, workforce, execution and performance management. To increase service and availability over a large geographic area, Advance decided to retrofit its existing distribution centers (DCs), while also constructing a new 550,000 square-foot facility that would provide daily replenishments to stores in a targeted rollout region.
The Solution
To support these facility expansions, as well as its new daily replenishment strategy, Advance added JDA Warehouse Management and JDA Warehouse Labor Management from JDA’s Intelligent Fulfillment™ solution. The company shifted from a 36- to 48-hour sale-to-replenish cycle time to as little as 12 hours. This shift in strategy represented a significant change in the way Advance serviced its stores, and ultimately, its customers. The company built the new building, processes, and all of the solution components from the ground up. In addition, Advance relied on the deep experience of the JDA Services team. The JDA Services team helped coach Advance on the technology and guide how they configured it, how they implemented it. The JDA solutions position Advance to be able to respond to change quicker. The company often has 10 to 15 configuration changes in a week, showing how flexible the system is, and how they’re able to make those changes and fine-tune the process.
Operational Impact
Quantitative Benefit
Case Study missing?
Start adding your own!
Register with your work email and create a new case study profile for your business.
Related Case Studies.
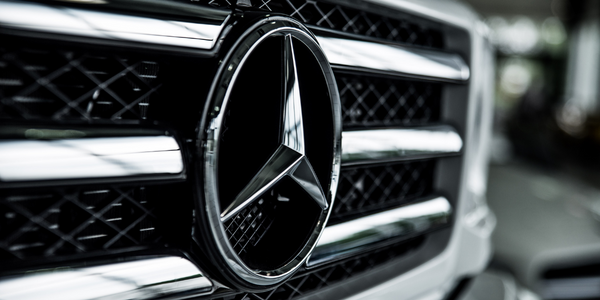
Case Study
Integral Plant Maintenance
Mercedes-Benz and his partner GAZ chose Siemens to be its maintenance partner at a new engine plant in Yaroslavl, Russia. The new plant offers a capacity to manufacture diesel engines for the Russian market, for locally produced Sprinter Classic. In addition to engines for the local market, the Yaroslavl plant will also produce spare parts. Mercedes-Benz Russia and his partner needed a service partner in order to ensure the operation of these lines in a maintenance partnership arrangement. The challenges included coordinating the entire maintenance management operation, in particular inspections, corrective and predictive maintenance activities, and the optimizing spare parts management. Siemens developed a customized maintenance solution that includes all electronic and mechanical maintenance activities (Integral Plant Maintenance).
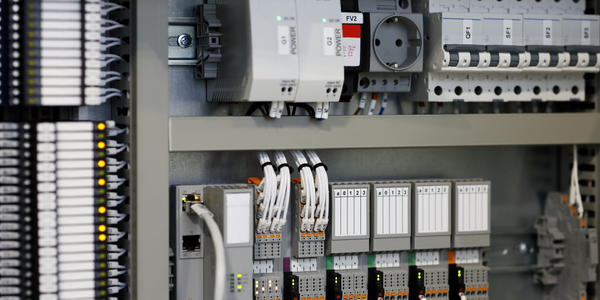
Case Study
Improving Production Line Efficiency with Ethernet Micro RTU Controller
Moxa was asked to provide a connectivity solution for one of the world's leading cosmetics companies. This multinational corporation, with retail presence in 130 countries, 23 global braches, and over 66,000 employees, sought to improve the efficiency of their production process by migrating from manual monitoring to an automatic productivity monitoring system. The production line was being monitored by ABB Real-TPI, a factory information system that offers data collection and analysis to improve plant efficiency. Due to software limitations, the customer needed an OPC server and a corresponding I/O solution to collect data from additional sensor devices for the Real-TPI system. The goal is to enable the factory information system to more thoroughly collect data from every corner of the production line. This will improve its ability to measure Overall Equipment Effectiveness (OEE) and translate into increased production efficiencies. System Requirements • Instant status updates while still consuming minimal bandwidth to relieve strain on limited factory networks • Interoperable with ABB Real-TPI • Small form factor appropriate for deployment where space is scarce • Remote software management and configuration to simplify operations