Customer Company Size
Mid-size Company
Region
- America
- Asia
- Europe
Country
- Canada
- China
- Taiwan
- United Kingdom
- United States
Product
- Acumatica Financial Management
- Acumatica Distribution Management
- Acumatica Intercompany Module
- Acumatica Fixed Assets
Tech Stack
- Acumatica ERP
- Sugar CRM
Implementation Scale
- Enterprise-wide Deployment
Impact Metrics
- Productivity Improvements
- Customer Satisfaction
- Digital Expertise
Technology Category
- Platform as a Service (PaaS) - Data Management Platforms
- Application Infrastructure & Middleware - Data Exchange & Integration
Applicable Functions
- Discrete Manufacturing
- Logistics & Transportation
Use Cases
- Supply Chain Visibility
- Inventory Management
Services
- Cloud Planning, Design & Implementation Services
- System Integration
About The Customer
Antenova is a multinational company headquartered in Hertfordshire, UK, with manufacturing, design, and technical operations in Taipei. The company also has sales and additional support offices in Santa Rosa, CA, Ottawa, Canada, and Shanghai, China. Antenova operates in the high-tech manufacturing industry, specifically in the production of high-performing standard antennas and RF antenna modules for wireless machine-to-machine, IoT, and consumer electronic devices. The company was previously using two separate systems for its operations: Sage50 for finance and Orderwise for purchase orders, sales, and warehouse management. However, the company decided to invest in an integrated ERP system to improve the efficiency of its operations and provide detailed business intelligence to its executive managers.
The Challenge
Antenova, a multinational company that manufactures high-performing standard antennas and RF antenna modules, was previously operating with two separate systems: Sage50 for finance and Orderwise for purchase orders, sales, and warehouse management. This setup posed challenges as the two systems did not work together, leading to manual data input from one system to the other. Some reports also had to be constructed in MS Excel to get the desired information. As the company grew and the IoT market expanded, Antenova needed to keep pace by renewing its website and digital marketing tools. This led to the need for a cloud-based ERP system that would enable Antenova to grow efficiently to meet these challenges.
The Solution
Antenova enlisted the help of systems partner YJ Jiang of Lumina Technology Co., Ltd., to evaluate newer Sage and other software packages. The company chose Acumatica's cloud-based ERP system due to its unlimited user pricing, ease-of-use, multicurrencies, and highly integrated functionality. The Acumatica solution included Financial Management, Distribution Management, Intercompany Module, and Fixed Assets. This new system allowed Antenova's teams to operate as if they were in the same office, with employees throughout the world gaining real-time access to the financial and warehouse systems. Executives also had instant access to the company's current financial status, which was previously only available when data was transferred from one system to the other, a slow and error-prone manual process.
Operational Impact
Case Study missing?
Start adding your own!
Register with your work email and create a new case study profile for your business.
Related Case Studies.
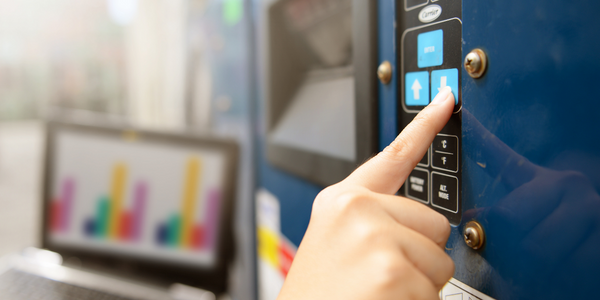
Case Study
Remote Temperature Monitoring of Perishable Goods Saves Money
RMONI was facing temperature monitoring challenges in a cold chain business. A cold chain must be established and maintained to ensure goods have been properly refrigerated during every step of the process, making temperature monitoring a critical business function. Manual registration practice can be very costly, labor intensive and prone to mistakes.
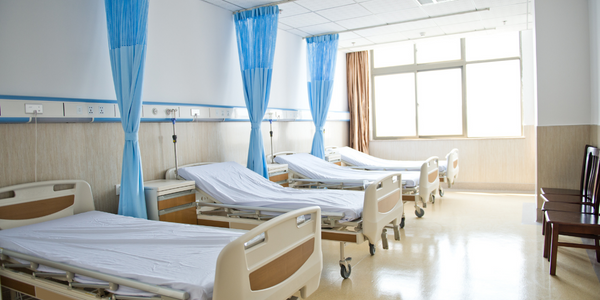
Case Study
Hospital Inventory Management
The hospital supply chain team is responsible for ensuring that the right medical supplies are readily available to clinicians when and where needed, and to do so in the most efficient manner possible. However, many of the systems and processes in use at the cancer center for supply chain management were not best suited to support these goals. Barcoding technology, a commonly used method for inventory management of medical supplies, is labor intensive, time consuming, does not provide real-time visibility into inventory levels and can be prone to error. Consequently, the lack of accurate and real-time visibility into inventory levels across multiple supply rooms in multiple hospital facilities creates additional inefficiency in the system causing over-ordering, hoarding, and wasted supplies. Other sources of waste and cost were also identified as candidates for improvement. Existing systems and processes did not provide adequate security for high-cost inventory within the hospital, which was another driver of cost. A lack of visibility into expiration dates for supplies resulted in supplies being wasted due to past expiry dates. Storage of supplies was also a key consideration given the location of the cancer center’s facilities in a dense urban setting, where space is always at a premium. In order to address the challenges outlined above, the hospital sought a solution that would provide real-time inventory information with high levels of accuracy, reduce the level of manual effort required and enable data driven decision making to ensure that the right supplies were readily available to clinicians in the right location at the right time.