Technology Category
- Application Infrastructure & Middleware - Event-Driven Application
- Functional Applications - Warehouse Management Systems (WMS)
Applicable Industries
- Buildings
- Retail
Applicable Functions
- Warehouse & Inventory Management
Use Cases
- Picking, Sorting & Positioning
- Time Sensitive Networking
About The Customer
Stitch Fix is a personal styling service that offers customers a curated shopping experience based on their unique tastes and preferences. The company operates in the retail ecommerce industry and has between 5,000 to 10,000 employees. Headquartered in San Francisco, California, Stitch Fix operates fulfillment centers in locations across the nation. The company is known for its personalized approach to shopping, offering customers a unique and tailored experience. As an ecommerce company, Stitch Fix relies heavily on its warehouse operations, requiring a large volume of workers to staff these warehouses.
The Challenge
Stitch Fix, an ecommerce company operating fulfillment centers across the United States, faced a significant challenge in staffing these warehouses with large volumes of workers. The hiring process for Warehouse Associates was mostly manual, requiring substantial time and energy from both recruiters and candidates. Candidates were manually screened, moved forward to the next stage, and scheduled for an interview by the team, which could sometimes take up to a week based on availability and speed. The time between the initial application to the new hire’s first day of work was approximately three weeks, attributed to mostly manual processes and a still-growing recruitment team. Stitch Fix needed a solution that could streamline and automate their hiring process, while still maintaining a personalized touch in their recruitment.
The Solution
Stitch Fix enrolled in Fountain’s Proof of Concept Program (PoC), a short-term partnership that allowed them to pilot the high volume hiring solution for three months. Fountain’s Sales and Customer Success team members guided Stitch Fix through a quick and seamless implementation and maintained a hands-on approach as Stitch Fix recruiters tested the platform’s features. Fountain’s dynamic drag-and-drop workflows enabled regional hiring teams to A/B test different features—like questionnaires, applicant routing rules, and the automated scheduling tool—and make changes on the fly to find the best hiring process for each geography. Stitch Fix also used Fountain as a communication platform before, during, and after their onsite hiring event in Salt Lake City. With Fountain, hiring teams can create rules that automatically move applicants to the next stage, allowing Stitch Fix to get workers in the door while also concentrating on other parts of the business.
Operational Impact
Quantitative Benefit
Case Study missing?
Start adding your own!
Register with your work email and create a new case study profile for your business.
Related Case Studies.
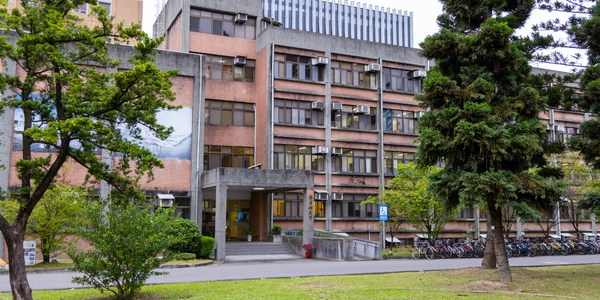
Case Study
Energy Saving & Power Monitoring System
Recently a university in Taiwan was experiencing dramatic power usage increases due to its growing number of campus buildings and students. Aiming to analyze their power consumption and increase their power efficiency across 52 buildings, the university wanted to build a power management system utilizing web-based hardware and software. With these goals in mind, they contacted Advantech to help them develop their system and provide them with the means to save energy in the years to come.
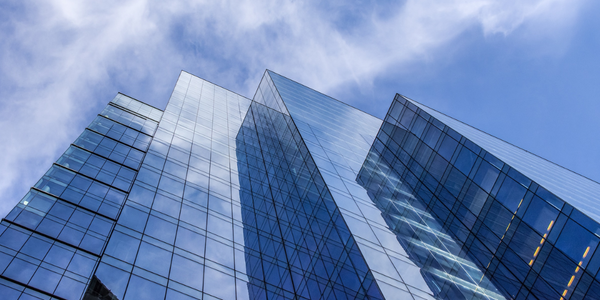
Case Study
Intelligent Building Automation System and Energy Saving Solution
One of the most difficult problems facing the world is conserving energy in buildings. However, it is not easy to have a cost-effective solution to reduce energy usage in a building. One solution for saving energy is to implement an intelligent building automation system (BAS) which can be controlled according to its schedule. In Indonesia a large university with a five floor building and 22 classrooms wanted to save the amount of energy being used.
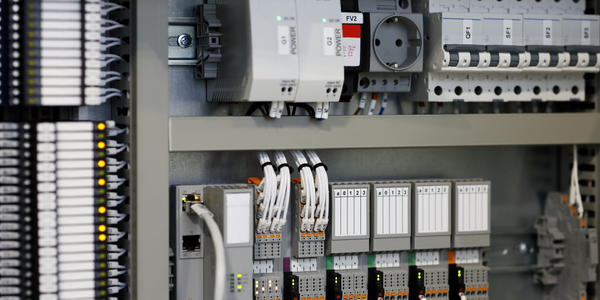
Case Study
Improving Production Line Efficiency with Ethernet Micro RTU Controller
Moxa was asked to provide a connectivity solution for one of the world's leading cosmetics companies. This multinational corporation, with retail presence in 130 countries, 23 global braches, and over 66,000 employees, sought to improve the efficiency of their production process by migrating from manual monitoring to an automatic productivity monitoring system. The production line was being monitored by ABB Real-TPI, a factory information system that offers data collection and analysis to improve plant efficiency. Due to software limitations, the customer needed an OPC server and a corresponding I/O solution to collect data from additional sensor devices for the Real-TPI system. The goal is to enable the factory information system to more thoroughly collect data from every corner of the production line. This will improve its ability to measure Overall Equipment Effectiveness (OEE) and translate into increased production efficiencies. System Requirements • Instant status updates while still consuming minimal bandwidth to relieve strain on limited factory networks • Interoperable with ABB Real-TPI • Small form factor appropriate for deployment where space is scarce • Remote software management and configuration to simplify operations
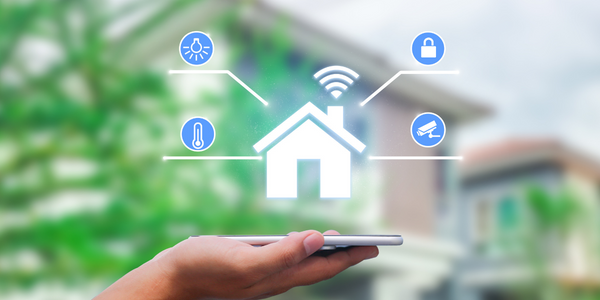
Case Study
Powering Smart Home Automation solutions with IoT for Energy conservation
Many industry leaders that offer Smart Energy Management products & solutions face challenges including:How to build a scalable platform that can automatically scale-up to on-board ‘n’ number of Smart home devicesData security, solution availability, and reliability are the other critical factors to deal withHow to create a robust common IoT platform that handles any kind of smart devicesHow to enable data management capabilities that would help in intelligent decision-making