Customer Company Size
Large Corporate
Region
- America
Country
- United States
Product
- Okta Access Gateway
- Okta Single Sign-On
- Okta Multi-Factor Authentication
- Okta Device Trust
Tech Stack
- SAML
- OpenID Connect
- Oracle Access Management
Implementation Scale
- Enterprise-wide Deployment
Impact Metrics
- Productivity Improvements
- Customer Satisfaction
- Digital Expertise
Technology Category
- Cybersecurity & Privacy - Identity & Authentication Management
- Application Infrastructure & Middleware - API Integration & Management
Applicable Industries
- Consumer Goods
- Retail
- Healthcare & Hospitals
Applicable Functions
- Business Operation
- Quality Assurance
Services
- System Integration
- Cloud Planning, Design & Implementation Services
About The Customer
Avery Dennison is a global materials science company specializing in the design and manufacture of a wide variety of labeling and functional materials. Founded by Stan Avery and Dorothy Durfee Avery, the company has grown from a small enterprise into a large corporation with over 32,000 employees in more than 50 countries. Avery Dennison's products are used in nearly every major industry and include pressure-sensitive materials for labels and graphic applications, tapes and bonding solutions for industrial, medical, and retail applications, tags, labels, and embellishments for apparel, and RFID solutions serving retail apparel and other markets. Headquartered in Glendale, California, Avery Dennison is committed to innovation and addressing challenges head-on, as reflected in its approach to technology and digital strategy.
The Challenge
Avery Dennison faced challenges in managing a complex IT landscape due to multiple acquisitions, which introduced new systems, apps, and user accounts. The company aimed to consolidate its IT stack, streamline cloud-based user sign-on and authentication processes, and enhance security. The influx of new apps and solutions brought inconsistent and hard-to-remember usernames and passwords, prompting Avery Dennison to explore ways to simplify the authentication process for employees and customers. The company needed a solution that could integrate with existing systems and provide a seamless user experience while maintaining high security standards.
The Solution
Avery Dennison selected Okta as its identity solution due to its pre-built integrations, which facilitated a quick and secure rollout without disrupting users. The company began by providing secure Single Sign-On access to G Suite and Kontiki, then expanded to other cloud-based applications with Okta's Multi-Factor Authentication. Avery Dennison also integrated Okta Access Gateway to provide a simple and secure experience for users accessing a wide variety of cloud-based and on-prem apps. The implementation of Okta Access Gateway allowed Avery Dennison to avoid normalizing 4,700+ user IDs across their environment, updating Single Sign-On IDs in just two hours. The company also adopted Okta's Adaptive Multi-Factor Authentication and API Access Management to enhance security and provide token validation and exchange for business-to-business endpoints. Avery Dennison's decision to use Okta Access Gateway was driven by its simplicity and ability to integrate more apps using SAML or OpenID Connect, reducing implementation steps and simplifying the user experience.
Operational Impact
Quantitative Benefit
Case Study missing?
Start adding your own!
Register with your work email and create a new case study profile for your business.
Related Case Studies.
.png)
Case Study
Improving Vending Machine Profitability with the Internet of Things (IoT)
The vending industry is undergoing a sea change, taking advantage of new technologies to go beyond just delivering snacks to creating a new retail location. Intelligent vending machines can be found in many public locations as well as company facilities, selling different types of goods and services, including even computer accessories, gold bars, tickets, and office supplies. With increasing sophistication, they may also provide time- and location-based data pertaining to sales, inventory, and customer preferences. But at the end of the day, vending machine operators know greater profitability is driven by higher sales and lower operating costs.
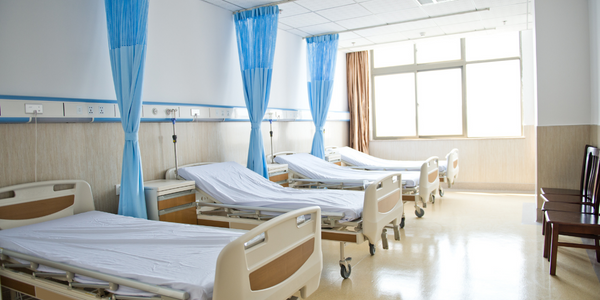
Case Study
Hospital Inventory Management
The hospital supply chain team is responsible for ensuring that the right medical supplies are readily available to clinicians when and where needed, and to do so in the most efficient manner possible. However, many of the systems and processes in use at the cancer center for supply chain management were not best suited to support these goals. Barcoding technology, a commonly used method for inventory management of medical supplies, is labor intensive, time consuming, does not provide real-time visibility into inventory levels and can be prone to error. Consequently, the lack of accurate and real-time visibility into inventory levels across multiple supply rooms in multiple hospital facilities creates additional inefficiency in the system causing over-ordering, hoarding, and wasted supplies. Other sources of waste and cost were also identified as candidates for improvement. Existing systems and processes did not provide adequate security for high-cost inventory within the hospital, which was another driver of cost. A lack of visibility into expiration dates for supplies resulted in supplies being wasted due to past expiry dates. Storage of supplies was also a key consideration given the location of the cancer center’s facilities in a dense urban setting, where space is always at a premium. In order to address the challenges outlined above, the hospital sought a solution that would provide real-time inventory information with high levels of accuracy, reduce the level of manual effort required and enable data driven decision making to ensure that the right supplies were readily available to clinicians in the right location at the right time.
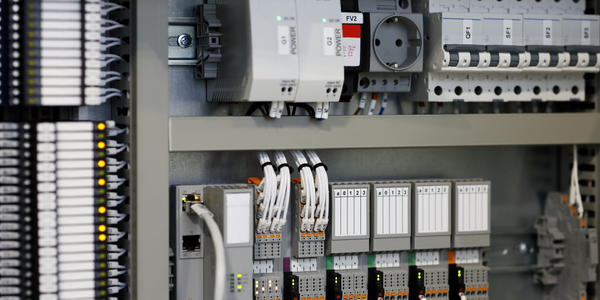
Case Study
Improving Production Line Efficiency with Ethernet Micro RTU Controller
Moxa was asked to provide a connectivity solution for one of the world's leading cosmetics companies. This multinational corporation, with retail presence in 130 countries, 23 global braches, and over 66,000 employees, sought to improve the efficiency of their production process by migrating from manual monitoring to an automatic productivity monitoring system. The production line was being monitored by ABB Real-TPI, a factory information system that offers data collection and analysis to improve plant efficiency. Due to software limitations, the customer needed an OPC server and a corresponding I/O solution to collect data from additional sensor devices for the Real-TPI system. The goal is to enable the factory information system to more thoroughly collect data from every corner of the production line. This will improve its ability to measure Overall Equipment Effectiveness (OEE) and translate into increased production efficiencies. System Requirements • Instant status updates while still consuming minimal bandwidth to relieve strain on limited factory networks • Interoperable with ABB Real-TPI • Small form factor appropriate for deployment where space is scarce • Remote software management and configuration to simplify operations