Customer Company Size
Mid-size Company
Region
- America
Country
- United States
Product
- DocuWare
- QuickBooks
- Outlook
- PSIcapture
Tech Stack
- Workflow Automation
- Document Management
- Email Integration
Implementation Scale
- Enterprise-wide Deployment
Impact Metrics
- Productivity Improvements
- Cost Savings
- Customer Satisfaction
Technology Category
- Application Infrastructure & Middleware - Data Exchange & Integration
- Functional Applications - Enterprise Resource Planning Systems (ERP)
Applicable Industries
- Automotive
Services
- System Integration
- Training
About The Customer
Carubba Collision is the largest body shop conglomerate in upstate New York. The company was established in 1955 and is dedicated to assisting customers with insurance claims and restoring their vehicles to pre-accident condition. Carubba Collision has been in a high growth phase, opening 4-6 new locations a year. To manage this growth, the company's CFO, Sean Penner, reviewed DocuWare’s functionality to determine which features could best be used by Carubba.
The Challenge
Carubba Collision, a body shop conglomerate in upstate New York, was experiencing a high growth phase, opening 4-6 new locations a year. This rapid expansion posed a challenge for the company's accounting department, which was struggling to manage the increasing volume of invoices and other financial documents. The company was using PSIcapture to transfer invoices into QuickBooks for processing, but the management team felt that a tighter integration between platforms could be achieved by implementing DocuWare’s workflow automation capabilities.
The Solution
Carubba Collision decided to implement DocuWare's workflow automation capabilities to streamline its accounting processes. The company integrated DocuWare with QuickBooks and Outlook, enabling accounting staff to easily send, receive, and upload documents via email. The company also implemented an 'Invoice Look Up' button in QuickBooks, which takes accounting staff directly to the required invoice in DocuWare. All employees received hands-on training on the use of DocuWare, which helped to increase employee buy-in and improve the efficiency of the accounting department.
Operational Impact
Quantitative Benefit
Case Study missing?
Start adding your own!
Register with your work email and create a new case study profile for your business.
Related Case Studies.
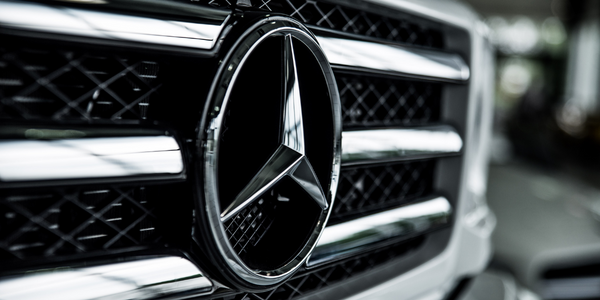
Case Study
Integral Plant Maintenance
Mercedes-Benz and his partner GAZ chose Siemens to be its maintenance partner at a new engine plant in Yaroslavl, Russia. The new plant offers a capacity to manufacture diesel engines for the Russian market, for locally produced Sprinter Classic. In addition to engines for the local market, the Yaroslavl plant will also produce spare parts. Mercedes-Benz Russia and his partner needed a service partner in order to ensure the operation of these lines in a maintenance partnership arrangement. The challenges included coordinating the entire maintenance management operation, in particular inspections, corrective and predictive maintenance activities, and the optimizing spare parts management. Siemens developed a customized maintenance solution that includes all electronic and mechanical maintenance activities (Integral Plant Maintenance).
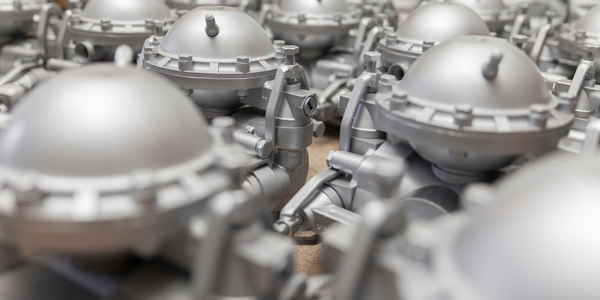
Case Study
Monitoring of Pressure Pumps in Automotive Industry
A large German/American producer of auto parts uses high-pressure pumps to deburr machined parts as a part of its production and quality check process. They decided to monitor these pumps to make sure they work properly and that they can see any indications leading to a potential failure before it affects their process.