Customer Company Size
Large Corporate
Region
- Europe
- America
- Asia
Country
- Switzerland
- Japan
- Russia
Product
- NAVEX One GRC Software
- EthicsPoint Incident Management
- NAVEXEngage Software for Online Ethics & Compliance Training
- NAVEX ESG
Tech Stack
- Compliance Management Software
- Incident Management Software
- Online Training Software
- ESG Management Software
Implementation Scale
- Enterprise-wide Deployment
Impact Metrics
- Cost Savings
- Brand Awareness
- Customer Satisfaction
Technology Category
- Application Infrastructure & Middleware - API Integration & Management
Applicable Functions
- Human Resources
- Business Operation
Use Cases
- Regulatory Compliance Monitoring
- Remote Collaboration
Services
- Cloud Planning, Design & Implementation Services
- Data Science Services
- System Integration
About The Customer
Castolin Eutectic is a leading wear protection company that provides sustainable solutions and a full range of consumables, equipment, and services in Maintenance & Repair welding, brazing, and coating technologies globally. The company is a technology and application know-how leader, increasing industrial components’ lifespan, maximizing plant uptime, and optimizing total cost of ownership for approximately 40,000 customers around the world. With over 100 years’ experience, Castolin Eutectic has outstanding brand recognition and a reputation for technological competence and reliability. The company has the largest and best trained in-house sales force, with unique technical capabilities covering all relevant industries worldwide (cement, oil and gas, iron and steel, power generation, recycling, and mining). It has a broad and highly diversified customer base with long-standing and intimate relationships supplying and servicing over 50 industries across the globe.
The Challenge
Castolin Eutectic, an industrial Maintenance and Repair technology company, needed a more holistic view of its compliance strategy. The company required a new code of conduct, compliance with the incoming EU Whistleblowing Directive, and an ESG framework to effectively manage how it measures multiple important factors. The company's most recent code of conduct was outdated and needed a new version that complied with regulations and would overcome barriers between regions. Castolin Eutectic was also in need of an incident management platform, as required by the EU Whistleblowing Directive. The challenge was finding a cultural fit across different regions, as not every market felt it would be suitable. Other parts of this revamp were to educate employees about ethics and compliance, to improve the organization’s culture and for its compliance suite to be effective.
The Solution
NAVEX worked closely with Castolin Eutectic to design an interactive PDF code of conduct as a source of work standards information. The code incorporated policies, ethics training, behavioral expectations, and hotline reporting communication to reinforce values and regulatory requirements. To comply with the upcoming EU Whistleblowing Directive, NAVEX introduced EthicsPoint across the business. This whistleblowing hotline service provides employees, customers, and suppliers with a safe place to speak up about workplace concerns. NAVEXEngage, NAVEX’s online ethics and compliance training solution, provides legally vetted and topical content that helps with compliance and employee adoption. Training addresses compliance, conduct, employment law and information security risks. The online platform is available in multiple languages and is easy for employees to access, wherever and whenever is most convenient to them.
Operational Impact
Quantitative Benefit
Case Study missing?
Start adding your own!
Register with your work email and create a new case study profile for your business.
Related Case Studies.
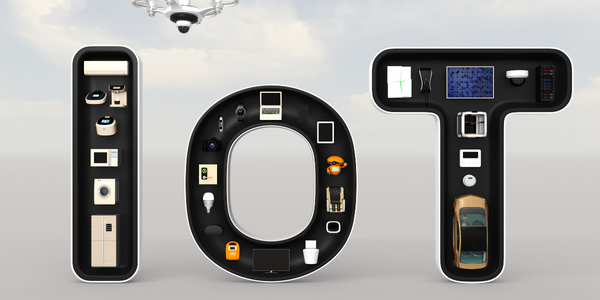
Case Study
Premium Appliance Producer Innovates with Internet of Everything
Sub-Zero faced the largest product launch in the company’s history:It wanted to launch 60 new products as scheduled while simultaneously opening a new “greenfield” production facility, yet still adhering to stringent quality requirements and manage issues from new supply-chain partners. A the same time, it wanted to increase staff productivity time and collaboration while reducing travel and costs.
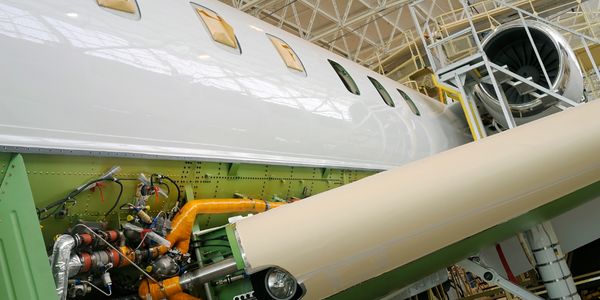
Case Study
Aerospace & Defense Case Study Airbus
For the development of its new wide-body aircraft, Airbus needed to ensure quality and consistency across all internal and external stakeholders. Airbus had many challenges including a very aggressive development schedule and the need to ramp up production quickly to satisfy their delivery commitments. The lack of communication extended design time and introduced errors that drove up costs.
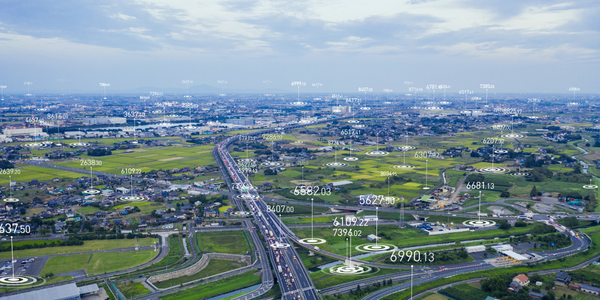
Case Study
Remote Monitoring for Environmental Compliance
Emerson wanted to provide a connected environmental analyzer to their customers. They wanted to leverage IoT technologies to provide a software solution that was easy to use, real-time and centralized. Compliance with pollution control board guidelines and the ability to remotely calibrate and troubleshoot these devices was the primary objective. Requirements - Centralized Remote Monitoring. - IoT Based Smart Environmental Analyzers. - Remote Calibration and Troubleshooting. - User Friendly Application. - Reporting & Dashboards. - Compliance with pollution control board guidelines.
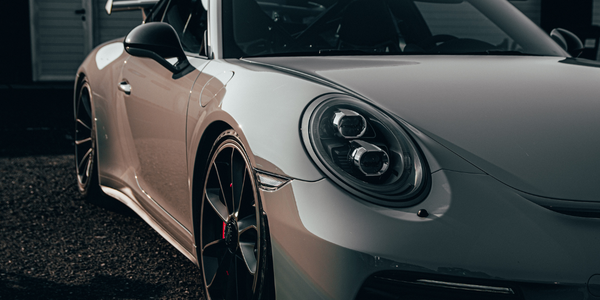
Case Study
Porsche Announces Augmented Reality at Scale, Powered by Atheer
The usual practice for car repairs at a Porsche car dealership is to have a factory representative or regional engineer visit to help diagnose the problem, and sometimes a faulty assembly is shipped back to company HQ for damage analysis. All that costs time and money for customers and dealers alike.
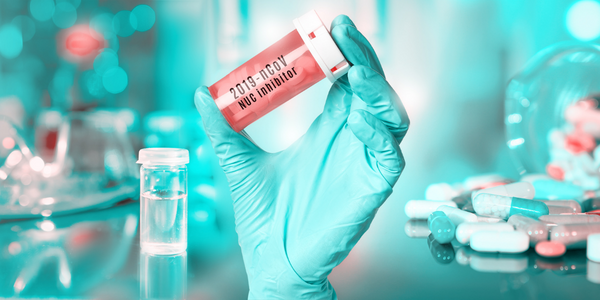
Case Study
ELI LILLY ADOPTS MICROMEDIA’S ALERT NOTIFICATION SYSTEM
Pharmaceutical production is subject to a strict set of enforced rules that must be adhered to and compliance to these standards is critically necessary. Due to the efforts of WIN 911’s strategic partner Micromedia, Lilly was able to adopt an alarm notification infrastructure that integrated smoothly with their existing workflows and emergency hardware and protocols. These raw energy sources enable the industrial process to function: electricity, WIN-911 Software | 4020 South Industrial Drive, Suite 120 | Austin, TX 78744 USA industrial steam, iced water, air mixtures of varying quality. Refrigeration towers, boilers and wastewater are monitored by ALERT. Eli Lilly identified 15000 potential variables, but limitations compelled them to chisel the variable list down to 300. This allowed all major alarms to be covered including pressure, discharge, quantity of waste water discharged,temperature, carbon dioxide content, oxygen & sulphur content, and the water’s pH.
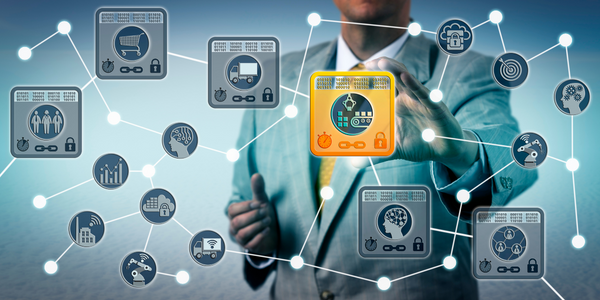
Case Study
Covisint Improves Mitsubishi's Collaboration With Its Supply Chain
Mitsubishi sought to improve supplier relationships on a global basis and to offer an easy-to-use solution to interact with them. In August 2004, Mitsubishi selected Covisint’s platform to help improve sharing of information and collaborative business processes with its global suppliers. Covisint enabled Mitsubishi to provide its suppliers with immediate access to information and applications to obtain more collaborative working relationships