Customer Company Size
Mid-size Company
Region
- Asia
Country
- Singapore
Product
- FlowForma Process Automation
Tech Stack
- Microsoft 365
- SharePoint
Implementation Scale
- Enterprise-wide Deployment
Impact Metrics
- Productivity Improvements
- Cost Savings
Technology Category
- Platform as a Service (PaaS) - Application Development Platforms
Applicable Functions
- Human Resources
Use Cases
- Process Control & Optimization
Services
- Software Design & Engineering Services
About The Customer
TOUCH Community Services is a not-for-profit organization based in Singapore. Established in 1986, the charity runs various support groups and clubs for people across all age groups. The organization has transformed the lives of low-income families that struggle to make ends meet. However, like many non-profit organizations, it faces the constant challenge of trying to improve services without incurring excessive costs. The organization has 300 employees spread across multiple locations, which adds to the complexity of its operations.
The Challenge
TOUCH Community Services, a non-profit organization based in Singapore, was struggling with inefficient manual processes for HR and finance forms. The forms were a mix of word documents, spreadsheets, and paperwork, and the approval process was time-consuming and depended on local and centrally-based managers. The organization has 300 employees across multiple locations, making the logistics of getting anything done quickly a challenge. For example, a training request process was done manually in a Microsoft Excel spreadsheet, making it difficult to track and not always up to date.
The Solution
TOUCH Community Services decided to implement FlowForma Process Automation, a product that is fully integrated with the Microsoft suite and more competitively priced. The solution was chosen because it was code-free and intuitive to use. To get up and running quicker, the organization took advantage of FlowForma SureStart, an onboarding program run over five days across two months. An Implementation Specialist and Client Manager were always available as they went on the journey from setting it up to 'going live'. The organization has devised a total of six processes – four around HR and two in finance – that range from training requests to staff and purchase requisitions.
Operational Impact
Quantitative Benefit
Case Study missing?
Start adding your own!
Register with your work email and create a new case study profile for your business.
Related Case Studies.
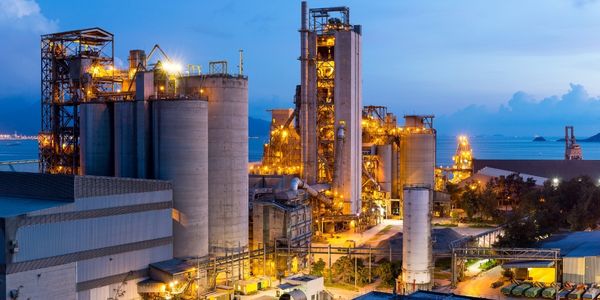
Case Study
System 800xA at Indian Cement Plants
Chettinad Cement recognized that further efficiencies could be achieved in its cement manufacturing process. It looked to investing in comprehensive operational and control technologies to manage and derive productivity and energy efficiency gains from the assets on Line 2, their second plant in India.
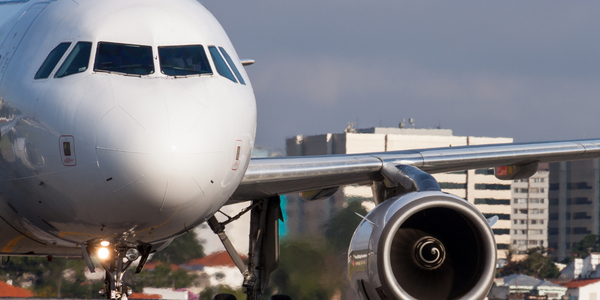
Case Study
Airbus Soars with Wearable Technology
Building an Airbus aircraft involves complex manufacturing processes consisting of thousands of moving parts. Speed and accuracy are critical to business and competitive advantage. Improvements in both would have high impact on Airbus’ bottom line. Airbus wanted to help operators reduce the complexity of assembling cabin seats and decrease the time required to complete this task.
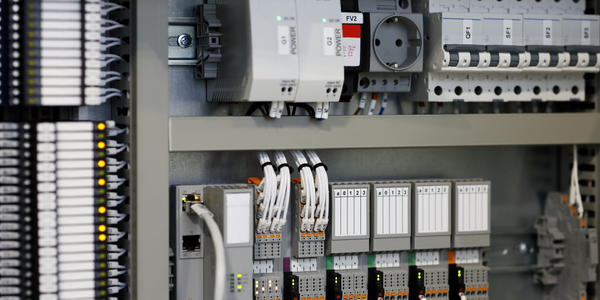
Case Study
Improving Production Line Efficiency with Ethernet Micro RTU Controller
Moxa was asked to provide a connectivity solution for one of the world's leading cosmetics companies. This multinational corporation, with retail presence in 130 countries, 23 global braches, and over 66,000 employees, sought to improve the efficiency of their production process by migrating from manual monitoring to an automatic productivity monitoring system. The production line was being monitored by ABB Real-TPI, a factory information system that offers data collection and analysis to improve plant efficiency. Due to software limitations, the customer needed an OPC server and a corresponding I/O solution to collect data from additional sensor devices for the Real-TPI system. The goal is to enable the factory information system to more thoroughly collect data from every corner of the production line. This will improve its ability to measure Overall Equipment Effectiveness (OEE) and translate into increased production efficiencies. System Requirements • Instant status updates while still consuming minimal bandwidth to relieve strain on limited factory networks • Interoperable with ABB Real-TPI • Small form factor appropriate for deployment where space is scarce • Remote software management and configuration to simplify operations
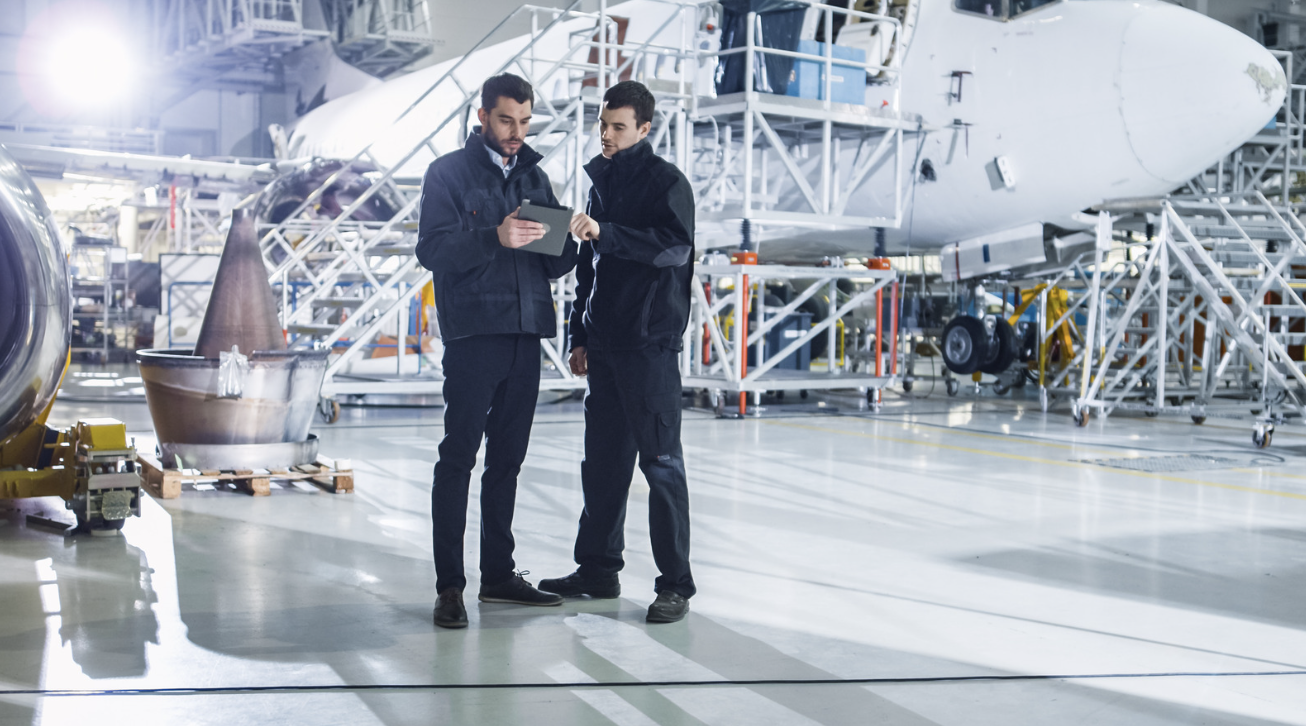
Case Study
Developing Smart Tools for the Airbus Factory
Manufacturing and assembly of aircraft, which involves tens of thousands of steps that must be followed by the operators, and a single mistake in the process could cost hundreds of thousands of dollars to fix, makes the room for error very small.