Customer Company Size
Mid-size Company
Region
- Europe
Country
- United Kingdom
Product
- Stream
Tech Stack
- Web-based Mapping Software
- Google Maps
- Sage
Implementation Scale
- Enterprise-wide Deployment
Impact Metrics
- Productivity Improvements
- Customer Satisfaction
Technology Category
- Functional Applications - Remote Monitoring & Control Systems
- Analytics & Modeling - Real Time Analytics
Applicable Functions
- Logistics & Transportation
- Warehouse & Inventory Management
Use Cases
- Fleet Management
- Predictive Maintenance
- Supply Chain Visibility
Services
- Software Design & Engineering Services
- System Integration
About The Customer
Contract Furniture Group is a leading manufacturer and distributor of high-quality furnishings, fixtures, and fittings for the hospitality industry in the United Kingdom and Europe. The company serves a diverse clientele, including hotels, restaurants, pubs, and clubs, providing them with a wide range of furniture solutions. As a prominent player in the industry, Contract Furniture Group has established a reputation for delivering exceptional products and services to its customers. The company has experienced significant growth over the years, expanding its workforce from 15-20 employees to 60, and increasing its operational capacity to meet rising customer demand. With a focus on quality and customer satisfaction, Contract Furniture Group continuously seeks innovative solutions to enhance its logistics operations and maintain its competitive edge in the market.
The Challenge
Contract Furniture Group faced significant challenges in their logistics operations, primarily due to the labor-intensive process of planning delivery routes. As the business expanded, the existing system, which relied on web-based mapping software and manual processes, became cumbersome and inefficient. The logistics team had to deal with frequent changes to delivery runs, which required constant reprinting and adjustments. Additionally, the lack of real-time visibility into order status and inventory levels made it difficult to track and manage deliveries effectively. This situation was further complicated by the need to coordinate various elements of each order, which could come from different sources, including in-house assembly, direct factory shipments, or supplier components. The absence of a streamlined system to manage these complexities led to inefficiencies and increased the risk of errors in the delivery process.
The Solution
To address the challenges in their logistics operations, Contract Furniture Group implemented Stream, a delivery management system designed to streamline planning and enhance order visibility. Stream provided the company with real-time insights into their logistics processes, allowing them to efficiently manage delivery routes and track order status. The system's mapping feature enabled the logistics team to visually plan deliveries by selecting pins on a route planning map, ensuring that all orders were accounted for and delivered on time. Stream's integration with existing systems, such as Sage, allowed for seamless data exchange and analysis, enabling the company to monitor delivery efficiency and driver hours. The implementation of Stream not only reduced the time spent on planning but also improved the overall accuracy and reliability of the logistics operations. As a result, Contract Furniture Group was able to scale its operations effectively, meeting increased customer demand while maintaining high standards of service.
Operational Impact
Quantitative Benefit
Case Study missing?
Start adding your own!
Register with your work email and create a new case study profile for your business.
Related Case Studies.

Case Study
Remote Monitoring & Predictive Maintenance App for a Solar Energy System
The maintenance & tracking of various modules was an overhead for the customer due to the huge labor costs involved. Being an advanced solar solutions provider, they wanted to ensure early detection of issues and provide the best-in-class customer experience. Hence they wanted to automate the whole process.
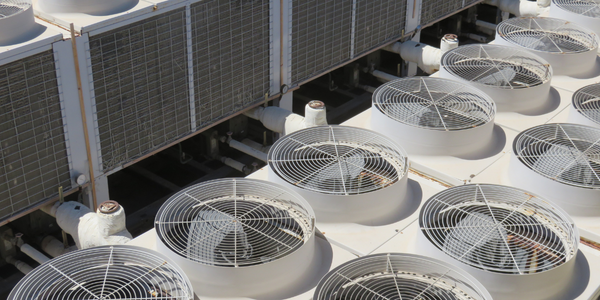
Case Study
Predictive Maintenance for Industrial Chillers
For global leaders in the industrial chiller manufacturing, reliability of the entire production process is of the utmost importance. Chillers are refrigeration systems that produce ice water to provide cooling for a process or industrial application. One of those leaders sought a way to respond to asset performance issues, even before they occur. The intelligence to guarantee maximum reliability of cooling devices is embedded (pre-alarming). A pre-alarming phase means that the cooling device still works, but symptoms may appear, telling manufacturers that a failure is likely to occur in the near future. Chillers who are not internet connected at that moment, provide little insight in this pre-alarming phase.
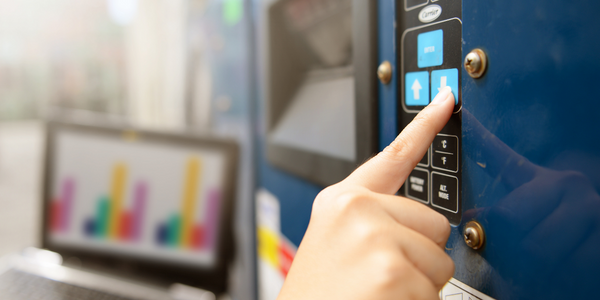
Case Study
Remote Temperature Monitoring of Perishable Goods Saves Money
RMONI was facing temperature monitoring challenges in a cold chain business. A cold chain must be established and maintained to ensure goods have been properly refrigerated during every step of the process, making temperature monitoring a critical business function. Manual registration practice can be very costly, labor intensive and prone to mistakes.
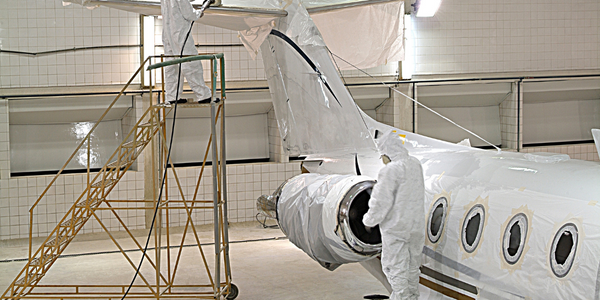
Case Study
Aircraft Predictive Maintenance and Workflow Optimization
First, aircraft manufacturer have trouble monitoring the health of aircraft systems with health prognostics and deliver predictive maintenance insights. Second, aircraft manufacturer wants a solution that can provide an in-context advisory and align job assignments to match technician experience and expertise.
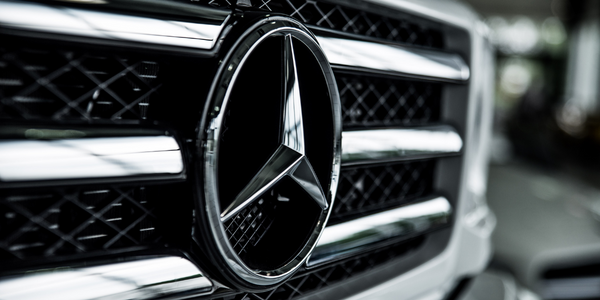
Case Study
Integral Plant Maintenance
Mercedes-Benz and his partner GAZ chose Siemens to be its maintenance partner at a new engine plant in Yaroslavl, Russia. The new plant offers a capacity to manufacture diesel engines for the Russian market, for locally produced Sprinter Classic. In addition to engines for the local market, the Yaroslavl plant will also produce spare parts. Mercedes-Benz Russia and his partner needed a service partner in order to ensure the operation of these lines in a maintenance partnership arrangement. The challenges included coordinating the entire maintenance management operation, in particular inspections, corrective and predictive maintenance activities, and the optimizing spare parts management. Siemens developed a customized maintenance solution that includes all electronic and mechanical maintenance activities (Integral Plant Maintenance).