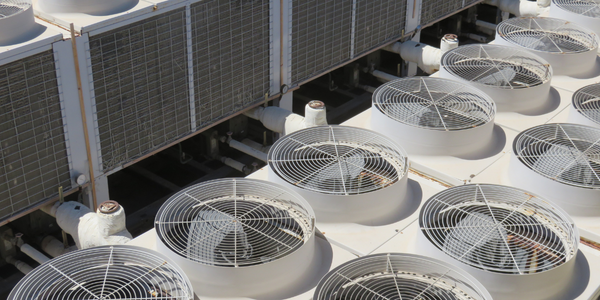
- Analytics & Modeling - Predictive Analytics
- Analytics & Modeling - Real Time Analytics
- Functional Applications - Enterprise Asset Management Systems (EAM)
- Networks & Connectivity - LoRa
- Sensors - Pressure Sensors
- Sensors - Temperature Sensors
- Equipment & Machinery
- Maintenance
- Predictive Maintenance
For global leaders in the industrial chiller manufacturing, reliability of the entire production process is of the utmost importance. Chillers are refrigeration systems that produce ice water to provide cooling for a process or industrial application. One of those leaders sought a way to respond to asset performance issues, even before they occur. The intelligence to guarantee maximum reliability of cooling devices is embedded (pre-alarming). A pre-alarming phase means that the cooling device still works, but symptoms may appear, telling manufacturers that a failure is likely to occur in the near future. Chillers who are not internet connected at that moment, provide little insight in this pre-alarming phase.
A failing device not only results in downtime, but as well in faulty chiller components. Chiller connectivity however, guarantees process stability, process reliability and energy efficiency, since all parameters (pressure, temperature, current values…) are monitored and visualized on our dashboard. This way, we can make a prediction regarding the amount of days within the failure is likely to occur.
Case Study missing?
Start adding your own!
Register with your work email and create a new case study profile for your business.
Related Case Studies.
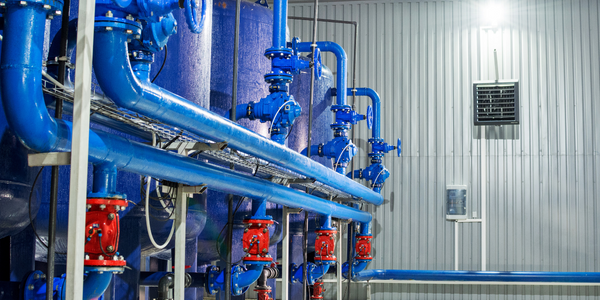
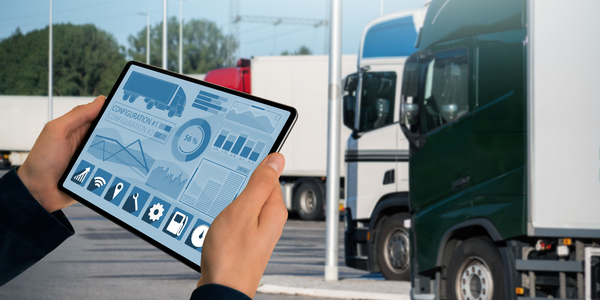
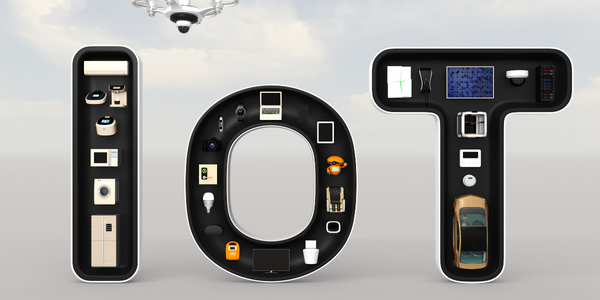
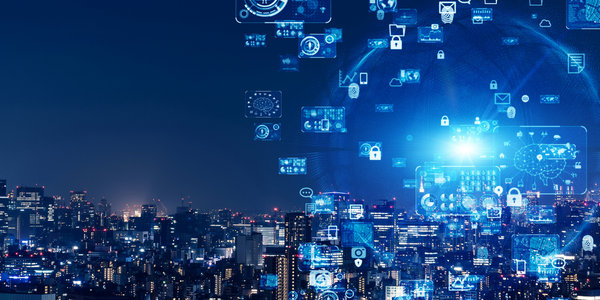
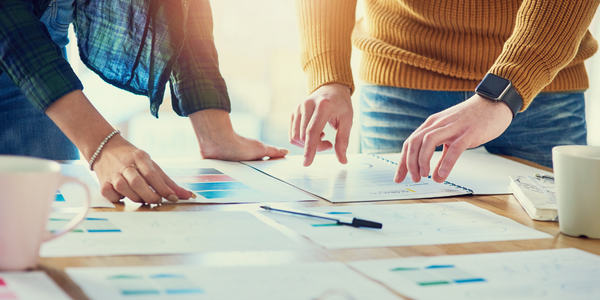
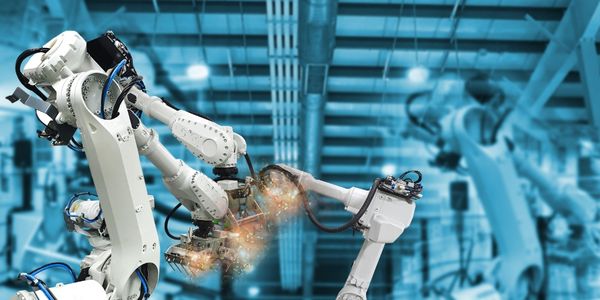