Customer Company Size
Large Corporate
Region
- Europe
Country
- United Kingdom
Product
- ICONICS GENESIS64™
Tech Stack
- Microsoft Azure
- Azure Table storage
- Azure Event Hub
- PowerBI
Implementation Scale
- Enterprise-wide Deployment
Impact Metrics
- Productivity Improvements
- Cost Savings
- Environmental Impact Reduction
Technology Category
- Platform as a Service (PaaS) - Data Management Platforms
- Analytics & Modeling - Real Time Analytics
Applicable Functions
- Facility Management
Use Cases
- Building Automation & Control
- Building Energy Management
- Predictive Maintenance
Services
- Cloud Planning, Design & Implementation Services
- Data Science Services
About The Customer
The Department for Business, Energy & Industrial Strategy (BEIS), formerly The Department for Business, Innovation, and Skills (BIS) is the department for business, science, and innovation within the UK Government. The department invests in skills and education to promote trade, boost innovation and help people to start and grow a business. To this end there are 49 partner organisations that sit under BIS, each with their own estates and facilities related datasets and challenges. The Property Asset Management Team was created in April 2014 to manage a portfolio of estate across the partner organisations and BIS. A significant part of this was to ensure evidence based decision making and to optimise the performance of buildings across the office estate. With around 2,500 staff working for the core BIS Department alone, and in excess of 14,500 people working across the partner organisations, there are offices across London, Sheffield, Cardiff, Manchester, Nottingham and a variety of other UK cities.
The Challenge
The Department for Business, Energy & Industrial Strategy (BEIS), formerly The Department for Business, Innovation, and Skills (BIS) is the department for business, science, and innovation within the UK Government. The Department’s holistic aim was to rationalise their building portfolio and shrink their carbon footprint by reducing the number of buildings they own and introducing more flexible work hours for their staff. But, in order to have any chance of shrinking their footprint, BIS realised that they needed to be able to analyse the performance of their estate, detect trends and use data to drive proactive estate management. The challenge was that the data and reporting processes for their entire building portfolio was completely fragmented. BIS did make sure to monitor the performance of their buildings. However, their manual data collection processes were so complex that they didn’t have the time or resources to digest the data and act accordingly.
The Solution
The Azure-hosted solution provides an integrated view of all BIS building assets. The Property Asset Management Team (PAM), can now drill down to any building, by geographical area, and see over 70 different data types in building dashboard summaries within Azure. There’s no longer a need to trawl through hundreds of different spreadsheets to see the buildings occupancy counts, energy consumption statistics, or lease agreements. This is data now accessible within a couple of clicks. BIS can manage all the data entry through a web upload interface, where they can upload their disparate spreadsheets; the solution offers a complete picture across multiple datasets and a single version of the truth. In utilising Microsoft’s Azure Table storage and Event Hub, ICONICS configured a truly scalable cloud solution, meaning that adding data sources in the future, and growing BIS’ audience across the government, isn’t going to be costly.
Operational Impact
Quantitative Benefit
Case Study missing?
Start adding your own!
Register with your work email and create a new case study profile for your business.
Related Case Studies.
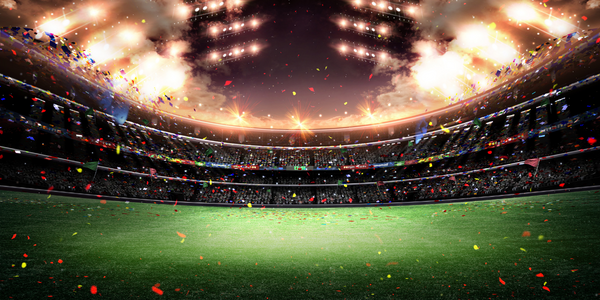
Case Study
Turning A Stadium Into A Smart Building
Honeywell created what it called the “intelligent system” for the National Stadium in Beijing, China, turning the venue for the opening and closing events at the 2008 Summer Olympics into a “smart building.” Designed by highly controversial artist Ai Weiwei, the “Bird’s Nest” remains one of the most impressive feats of stadium architecture in the world. The 250,000 square meter structure housed more than 100,000 athletes and spectators at a time. To accommodate such capacity, China turned to Honeywell’s EBI Integrated Building Management System to create an integrated “intelligent system” for improved building security, safety and energy efficiency.

Case Study
Remote Monitoring & Predictive Maintenance App for a Solar Energy System
The maintenance & tracking of various modules was an overhead for the customer due to the huge labor costs involved. Being an advanced solar solutions provider, they wanted to ensure early detection of issues and provide the best-in-class customer experience. Hence they wanted to automate the whole process.
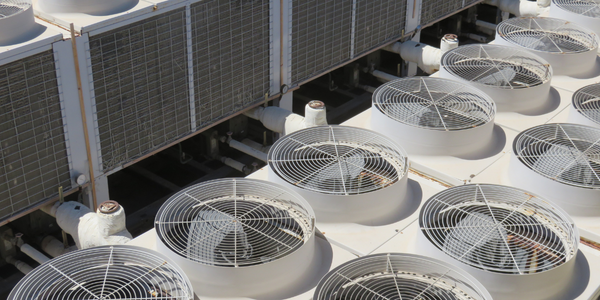
Case Study
Predictive Maintenance for Industrial Chillers
For global leaders in the industrial chiller manufacturing, reliability of the entire production process is of the utmost importance. Chillers are refrigeration systems that produce ice water to provide cooling for a process or industrial application. One of those leaders sought a way to respond to asset performance issues, even before they occur. The intelligence to guarantee maximum reliability of cooling devices is embedded (pre-alarming). A pre-alarming phase means that the cooling device still works, but symptoms may appear, telling manufacturers that a failure is likely to occur in the near future. Chillers who are not internet connected at that moment, provide little insight in this pre-alarming phase.
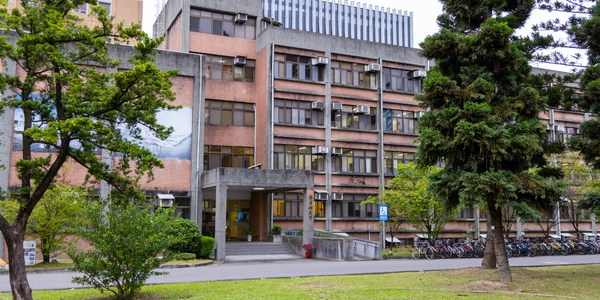
Case Study
Energy Saving & Power Monitoring System
Recently a university in Taiwan was experiencing dramatic power usage increases due to its growing number of campus buildings and students. Aiming to analyze their power consumption and increase their power efficiency across 52 buildings, the university wanted to build a power management system utilizing web-based hardware and software. With these goals in mind, they contacted Advantech to help them develop their system and provide them with the means to save energy in the years to come.
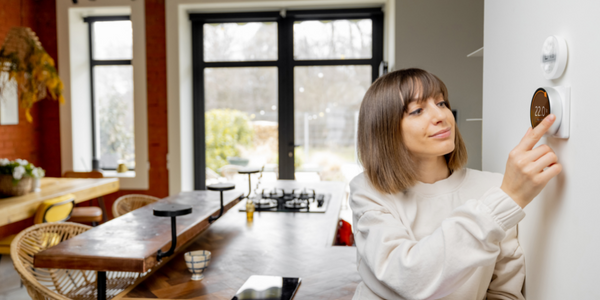
Case Study
BACnet enabled Wireless Temperature Monitoring System
Client offered a Temperature Monitoring System which consists of Wireless Transmitters and Application Software. Third party BACnet Application such as a Building Automation System needs access to vital parameter such as temperature, humidity, CO2, etc., measured by wireless sensor devices. Client needed a solution to allow data exchange from its Temperature Monitoring System with BMS.
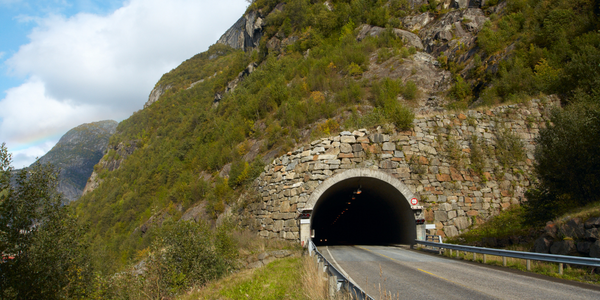
Case Study
IoT System for Tunnel Construction
The Zenitaka Corporation ('Zenitaka') has two major business areas: its architectural business focuses on structures such as government buildings, office buildings, and commercial facilities, while its civil engineering business is targeted at structures such as tunnels, bridges and dams. Within these areas, there presented two issues that have always persisted in regard to the construction of mountain tunnels. These issues are 'improving safety" and "reducing energy consumption". Mountain tunnels construction requires a massive amount of electricity. This is because there are many kinds of electrical equipment being used day and night, including construction machinery, construction lighting, and ventilating fan. Despite this, the amount of power consumption is generally not tightly managed. In many cases, the exact amount of power consumption is only ascertained when the bill from the power company becomes available. Sometimes, corporations install demand-monitoring equipment to help curb the maximum power demanded. However, even in these cases, the devices only allow the total volume of power consumption to be ascertained, or they may issue warnings to prevent the contracted volume of power from being exceeded. In order to tackle the issue of reducing power consumption, it was first necessary to obtain an accurate breakdown of how much power was being used in each particular area. In other words, we needed to be able to visualize the amount of power being consumed. Safety, was also not being managed very rigorously. Even now, tunnel construction sites often use a 'name label' system for managing entry into the work site. Specifically, red labels with white reverse sides that bear the workers' names on both sides are displayed at the tunnel work site entrance. The workers themselves then flip the name label to the appropriate side when entering or exiting from the work site to indicate whether or not they are working inside the tunnel at any given time. If a worker forgets to flip his or her name label when entering or exiting from the tunnel, management cannot be performed effectively. In order to tackle the challenges mentioned above, Zenitaka decided to build a system that could improve the safety of tunnel construction as well as reduce the amount of power consumed. In other words, this new system would facilitate a clear picture of which workers were working in each location at the mountain tunnel construction site, as well as which processes were being carried out at those respective locations at any given time. The system would maintain the safety of all workers while also carefully controlling the electrical equipment to reduce unnecessary power consumption. Having decided on the concept, our next concern was whether there existed any kind of robust hardware that would not break down at the construction work site, that could move freely in response to changes in the working environment, and that could accurately detect workers and vehicles using radio frequency identification (RFID). Given that this system would involve many components that were new to Zenitaka, we decided to enlist the cooperation of E.I.Sol Co., Ltd. ('E.I.Sol') as our joint development partner, as they had provided us with a highly practical proposal.