Technology Category
- Application Infrastructure & Middleware - Data Exchange & Integration
- Functional Applications - Enterprise Resource Planning Systems (ERP)
Applicable Industries
- Electronics
- Retail
Applicable Functions
- Quality Assurance
- Sales & Marketing
Use Cases
- Inventory Management
- Retail Store Automation
Services
- Data Science Services
- System Integration
About The Customer
Bing Lee is a consumer electronics retail chain with more than 35 stores across New South Wales, Australia. Family-owned and founded in 1957, Bing Lee is known for affordability and a radio jingle that has become part of the local pop culture. Its annual turnover is almost 500 million AUD. Though a traditional family business, Bing Lee recognized a need to change with the times and began a technology transformation. The company invested in a new cloud-based ERP and developed their own Point of Sale (POS) system. A new reporting tool was also selected to improve user experience for employees.
The Challenge
Bing Lee, a consumer electronics retail chain in Australia, was facing a significant challenge in integrating business data during a complex digital transformation project. The company's legacy ERP had become a highly customized system, dependent on a single point of failure. Its data was unstructured, and problematic processes were making the data generated by the system unreliable. Bing Lee invested in a new cloud-based ERP and developed their own Point of Sale (POS) system. A new reporting tool was also selected to improve user experience for employees. However, the transition to the new ERP was slowed down by the Covid-19 pandemic, and the company's sales and number of transactions substantially grew, increasing the volume of data through its systems.
The Solution
Bing Lee decided to use BizCubed’s Data Engineering and Enablement Platform (DEEP) for data management, with Hitachi Vantara’s Pentaho Data Integration (part of the Pentaho Platform Suite) as the engine for ETL design and orchestration. This solution is provided as-a-service, which allows Bing Lee to continually update its data processing at the pace of business. The project team uses Pentaho to generate ETL processes that successfully merge and blend daily reporting data from two ERP solutions and more than 45 different API sources. BizCubed’s methodology provides a framework for rapid data acquisition, monitoring, recovery, and governance. This means that Bing Lee can have confidence in the reliability and accessibility of its data, every single day.
Operational Impact
Quantitative Benefit
Case Study missing?
Start adding your own!
Register with your work email and create a new case study profile for your business.
Related Case Studies.
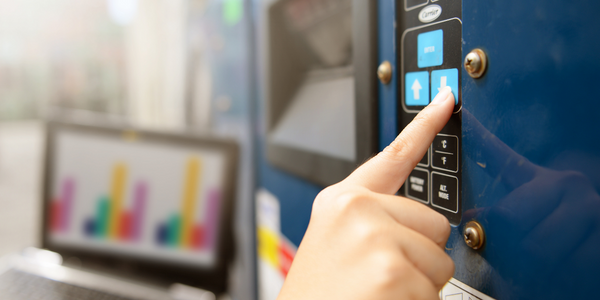
Case Study
Remote Temperature Monitoring of Perishable Goods Saves Money
RMONI was facing temperature monitoring challenges in a cold chain business. A cold chain must be established and maintained to ensure goods have been properly refrigerated during every step of the process, making temperature monitoring a critical business function. Manual registration practice can be very costly, labor intensive and prone to mistakes.
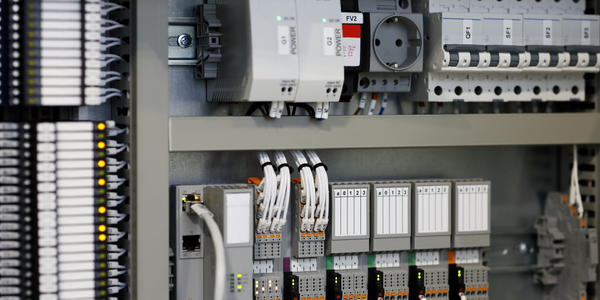
Case Study
Improving Production Line Efficiency with Ethernet Micro RTU Controller
Moxa was asked to provide a connectivity solution for one of the world's leading cosmetics companies. This multinational corporation, with retail presence in 130 countries, 23 global braches, and over 66,000 employees, sought to improve the efficiency of their production process by migrating from manual monitoring to an automatic productivity monitoring system. The production line was being monitored by ABB Real-TPI, a factory information system that offers data collection and analysis to improve plant efficiency. Due to software limitations, the customer needed an OPC server and a corresponding I/O solution to collect data from additional sensor devices for the Real-TPI system. The goal is to enable the factory information system to more thoroughly collect data from every corner of the production line. This will improve its ability to measure Overall Equipment Effectiveness (OEE) and translate into increased production efficiencies. System Requirements • Instant status updates while still consuming minimal bandwidth to relieve strain on limited factory networks • Interoperable with ABB Real-TPI • Small form factor appropriate for deployment where space is scarce • Remote software management and configuration to simplify operations
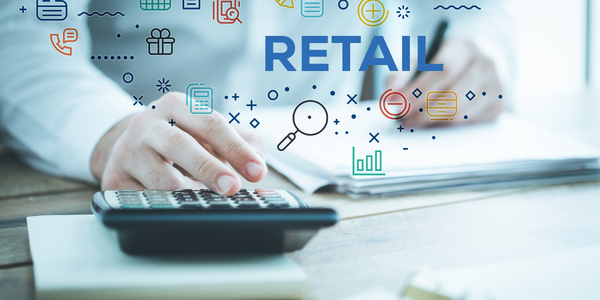
Case Study
Digital Retail Security Solutions
Sennco wanted to help its retail customers increase sales and profits by developing an innovative alarm system as opposed to conventional connected alarms that are permanently tethered to display products. These traditional security systems were cumbersome and intrusive to the customer shopping experience. Additionally, they provided no useful data or analytics.
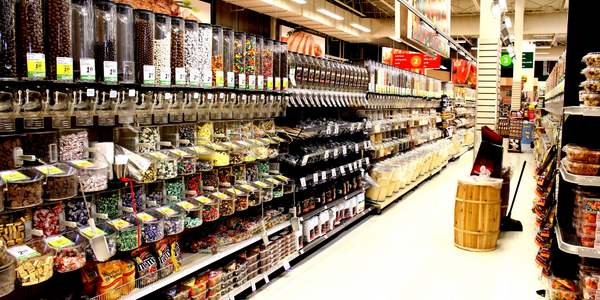
Case Study
How Sirqul’s IoT Platform is Crafting Carrefour’s New In-Store Experiences
Carrefour Taiwan’s goal is to be completely digital by end of 2018. Out-dated manual methods for analysis and assumptions limited Carrefour’s ability to change the customer experience and were void of real-time decision-making capabilities. Rather than relying solely on sales data, assumptions, and disparate systems, Carrefour Taiwan’s CEO led an initiative to find a connected IoT solution that could give the team the ability to make real-time changes and more informed decisions. Prior to implementing, Carrefour struggled to address their conversion rates and did not have the proper insights into the customer decision-making process nor how to make an immediate impact without losing customer confidence.