Technology Category
- Platform as a Service (PaaS) - Application Development Platforms
Applicable Industries
- Automotive
- Finance & Insurance
Applicable Functions
- Maintenance
- Quality Assurance
Use Cases
- Inventory Management
- Usage-Based Insurance
Services
- System Integration
- Testing & Certification
About The Customer
SISA is a leading insurance and investment company based in El Salvador. Founded in 1962, the company offers a wide range of insurance products and has established itself as a market leader in the country. SISA's mission is to provide peace of mind and financial security to its customers through quality products, digital processes, and excellent service. The company is committed to maintaining its leadership in premiums and profitability in El Salvador. SISA's customer base includes individuals, insurance intermediaries, and suppliers such as garages, hospitals, and laboratories.
The Challenge
SISA, a leading insurance company in El Salvador, was grappling with the challenge of managing two different workflow systems for policy issuance and claims processes. This fragmented approach was causing delays, reducing responsiveness, and making it difficult to monitor tasks effectively. The company was also dealing with the inefficiency of manual data input, as customers had to write information on physical forms, which then had to be copied into the system. To address these issues, SISA decided to migrate to an integrated tool that could drive continuous improvement across all processes. The company also sought to decentralize operations and involve all participants in the processes, enabling information to be uploaded on electronic forms at each point of contact with clients, insurance intermediaries, and suppliers.
The Solution
SISA chose the AuraQuantic Low Code Applications Platform (LCAP) to drive its digital transformation. The platform integrated all internal and external process activities into business operations, enabling accurate monitoring of response standards and setting notifications and alerts in case of deviations. The old Intermediaries Portal was migrated to the new digital platform, which also included reports providing valuable information to agents and brokers. Further portals were created for other partners such as garages in the claims processes and hospitals and laboratories in the health processes. One of the key innovations was the service of assistance for automobile insurance, which collected all information on site and in real time. The customer could select the garage and initiate vehicle repair management, with SISA providing budget tracking for repairs, delivery times, etc.
Operational Impact
Quantitative Benefit
Case Study missing?
Start adding your own!
Register with your work email and create a new case study profile for your business.
Related Case Studies.
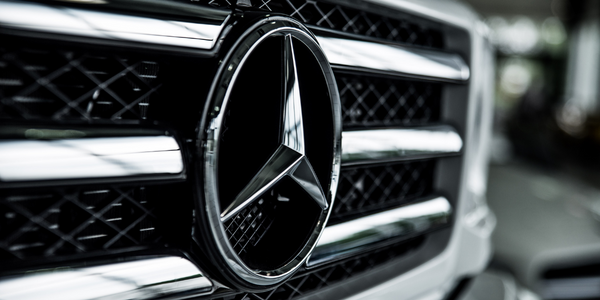
Case Study
Integral Plant Maintenance
Mercedes-Benz and his partner GAZ chose Siemens to be its maintenance partner at a new engine plant in Yaroslavl, Russia. The new plant offers a capacity to manufacture diesel engines for the Russian market, for locally produced Sprinter Classic. In addition to engines for the local market, the Yaroslavl plant will also produce spare parts. Mercedes-Benz Russia and his partner needed a service partner in order to ensure the operation of these lines in a maintenance partnership arrangement. The challenges included coordinating the entire maintenance management operation, in particular inspections, corrective and predictive maintenance activities, and the optimizing spare parts management. Siemens developed a customized maintenance solution that includes all electronic and mechanical maintenance activities (Integral Plant Maintenance).
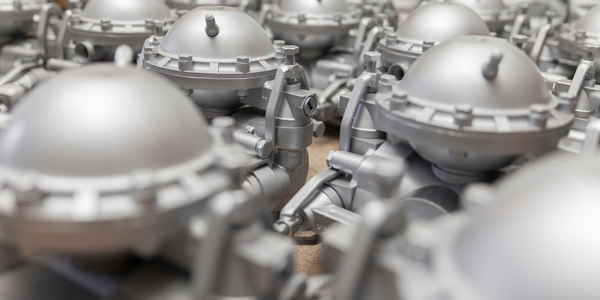
Case Study
Monitoring of Pressure Pumps in Automotive Industry
A large German/American producer of auto parts uses high-pressure pumps to deburr machined parts as a part of its production and quality check process. They decided to monitor these pumps to make sure they work properly and that they can see any indications leading to a potential failure before it affects their process.