Technology Category
- Sensors - Chemical Sensors
- Sensors - Liquid Detection Sensors
Applicable Industries
- Chemicals
- Healthcare & Hospitals
Applicable Functions
- Procurement
Use Cases
- Onsite Human Safety Management
- Personnel Tracking & Monitoring
About The Customer
Oslo University Hospital (OUH) is the largest hospital in Norway and Scandinavia, with over 24,000 employees. The hospital provides high-quality services for the citizens of Oslo and is in charge of extensive regional and local hospital assignments. OUH carries out more than 1.2 million patient treatments annually and conducts a significant percentage of the medical research carried out at Norwegian medical centres. The hospital's main challenge was managing its chemical safety, particularly the countless chemical Safety Data Sheets (SDS), conducting risk assessments, and making substitutions to reduce hazardous chemicals.
The Challenge
Oslo University Hospital (OUH), the largest hospital in Norway and Scandinavia, was facing a significant challenge in managing its chemical safety. The hospital, which carries out over 1.2 million patient treatments annually and conducts a significant percentage of medical research in Norwegian medical centres, was struggling with the management of countless chemical Safety Data Sheets (SDS), conducting risk assessments, and making substitutions to reduce hazardous chemicals. The process of managing chemicals throughout their lifecycle, from procurement to waste management, was slow, costly, and often required external support. The scale and urgency of OUH's needs were critical, and a digital solution was needed to replace and secure its SDS.
The Solution
OUH partnered with EcoOnline, a company that provides digital solutions for chemical safety management. The hospital implemented EcoOnline's Chemical Safety, a platform that allowed for comprehensive and improved management of chemicals throughout their lifecycle. The solution was tailored to OUH's needs, including a section in the SDS that specified each type of waste alongside standardised EAL codes. This digital solution empowered staff to declare hazardous waste safely and quickly. The platform also increased safety awareness across the team and helped to strengthen the safety culture at OUH. It enabled staff to make safer decisions about chemicals, such as classifying chemicals according to their risk level, creating a safer working environment for all, particularly pregnant employees.
Operational Impact
Quantitative Benefit
Case Study missing?
Start adding your own!
Register with your work email and create a new case study profile for your business.
Related Case Studies.
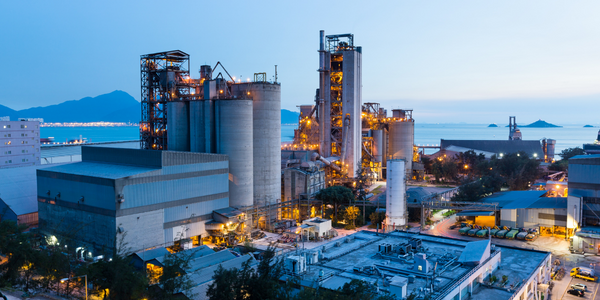
Case Study
Honeywell - Tata Chemicals Improves Data Accessibility with OneWireless
Tata was facing data accessibility challenges in the cement plant control room tapping signals from remote process control areas and other distant locations, including the gas scrubber. Tata needed a wireless solution to extend its control network securely to remote locations that would also provide seamless communication with existing control applications.
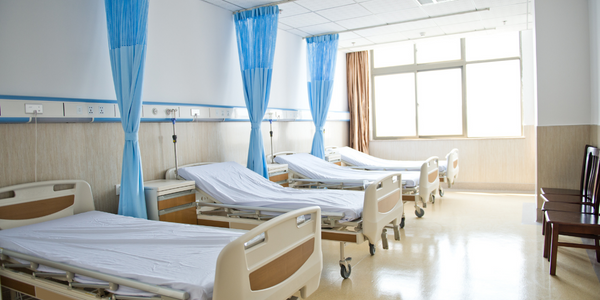
Case Study
Hospital Inventory Management
The hospital supply chain team is responsible for ensuring that the right medical supplies are readily available to clinicians when and where needed, and to do so in the most efficient manner possible. However, many of the systems and processes in use at the cancer center for supply chain management were not best suited to support these goals. Barcoding technology, a commonly used method for inventory management of medical supplies, is labor intensive, time consuming, does not provide real-time visibility into inventory levels and can be prone to error. Consequently, the lack of accurate and real-time visibility into inventory levels across multiple supply rooms in multiple hospital facilities creates additional inefficiency in the system causing over-ordering, hoarding, and wasted supplies. Other sources of waste and cost were also identified as candidates for improvement. Existing systems and processes did not provide adequate security for high-cost inventory within the hospital, which was another driver of cost. A lack of visibility into expiration dates for supplies resulted in supplies being wasted due to past expiry dates. Storage of supplies was also a key consideration given the location of the cancer center’s facilities in a dense urban setting, where space is always at a premium. In order to address the challenges outlined above, the hospital sought a solution that would provide real-time inventory information with high levels of accuracy, reduce the level of manual effort required and enable data driven decision making to ensure that the right supplies were readily available to clinicians in the right location at the right time.

Case Study
Advanced Elastomer Systems Upgrades Production
In order to maintain its share of the international market for thermoplastic elastomers AES recently expanded its Florida plant by adding a new production line. While the existing lines were operating satisfactorily using a PROVOX distributed control system with traditional analog I/O, AES wanted advanced technology on the new line for greater economy, efficiency, and reliability. AES officials were anxious to get this line into production to meet incoming orders, but two hurricanes slowed construction.
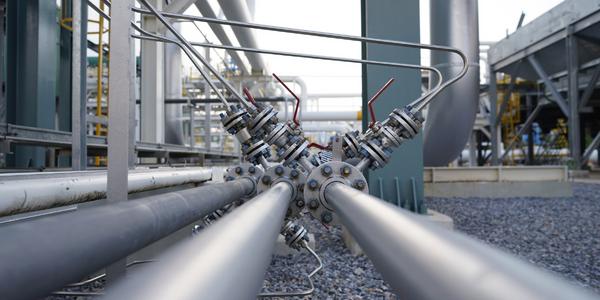
Case Study
Gas Pipeline Monitoring System for Hospitals
This system integrator focuses on providing centralized gas pipeline monitoring systems for hospitals. The service they provide makes it possible for hospitals to reduce both maintenance and labor costs. Since hospitals may not have an existing network suitable for this type of system, GPRS communication provides an easy and ready-to-use solution for remote, distributed monitoring systems System Requirements - GPRS communication - Seamless connection with SCADA software - Simple, front-end control capability - Expandable I/O channels - Combine AI, DI, and DO channels
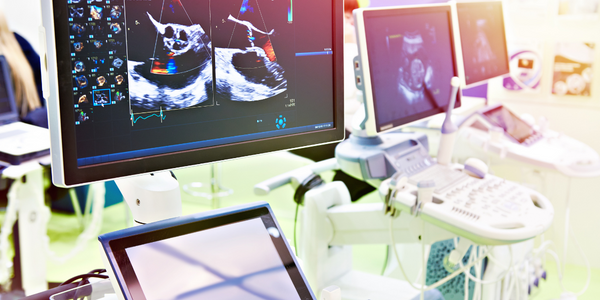
Case Study
Driving Digital Transformations for Vitro Diagnostic Medical Devices
Diagnostic devices play a vital role in helping to improve healthcare delivery. In fact, an estimated 60 percent of the world’s medical decisions are made with support from in vitrodiagnostics (IVD) solutions, such as those provided by Roche Diagnostics, an industry leader. As the demand for medical diagnostic services grows rapidly in hospitals and clinics across China, so does the market for IVD solutions. In addition, the typically high cost of these diagnostic devices means that comprehensive post-sales services are needed. Wanteed to improve three portions of thr IVD:1. Remotely monitor and manage IVD devices as fixed assets.2. Optimizing device availability with predictive maintenance.3. Recommending the best IVD solution for a customer’s needs.