Technology Category
- Platform as a Service (PaaS) - Application Development Platforms
- Sensors - Utility Meters
Applicable Industries
- Oil & Gas
- Transportation
Applicable Functions
- Procurement
- Product Research & Development
Use Cases
- Autonomous Transport Systems
- Transportation Simulation
Services
- System Integration
About The Customer
Dockwise Shipping B.V., a wholly owned subsidiary of Royal Boskalis Westminster N.V., is a company that develops innovative solutions for heavy transport and installation (T&I) in the maritime infrastructure sector. With a fleet of 23 semi-submersible vessels and two floating super pallets, Dockwise operates worldwide with its headquarters in Breda, The Netherlands. The company was selected as the T&I contractor for the SHWE field development project in the Bay of Bengal, Myanmar, setting a weight record with the installation of the nearly 22,000-metric ton jacket and 30,000-metric ton topsides with deck support frame for the SHWE platform.
The Challenge
Dockwise, a subsidiary of Royal Boskalis Westminster N.V., was tasked with the installation of the nearly 22,000-metric ton jacket and 30,000-metric ton topsides with deck support frame for the SHWE platform in the Bay of Bengal, Myanmar. This was part of the USD 1.5 billion SHWE field development project. The installation involved one of the largest jackets and one of the heaviest topsides in the world, pushing the limits of the installation barge. The barge's unique bottle shape satisfied the stability and jacket footprint requirements but posed challenges for the mooring arrangement and transportation global strength needs. The short, fat, and heavy jacket also brought challenges to the launch operation. The project was distributed across three office centers in The Netherlands, United States, and China, which posed challenges in data access, accuracy, traceability, and workflow, especially for the final product design drawings.
The Solution
Dockwise utilized Bentley’s offshore platform analysis, design, and installation software, MOSES and SACS, to tackle the engineering challenges. MOSES, a comprehensive suite of analysis software for the installation of offshore structures, was used to calculate all the time-history hydrodynamic-related information such as float-over impact force and motions. SACS, an integrated suite of software for structural analysis and design of offshore structures, was used to dynamically iterate designs, comply with offshore design criteria, and visualize complex results. The data transfer between SACS and MOSES increased project efficiency, enabling the project team to do extensive analysis to verify the ideas in an effective manner. For data management, the project team used MicroStation and ProjectWise. The full integration of MicroStation and ProjectWise provided a natural and easy process for the drawing being transferred between different departments at different locations. It also facilitated the workflow for the review and approval process.
Operational Impact
Quantitative Benefit
Case Study missing?
Start adding your own!
Register with your work email and create a new case study profile for your business.
Related Case Studies.
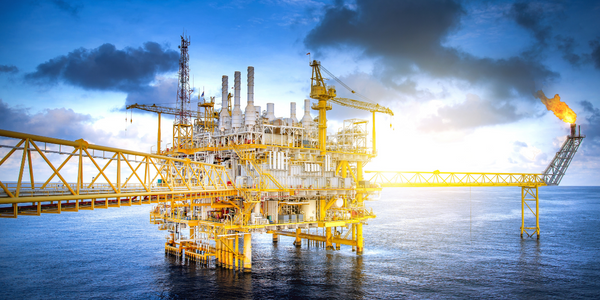
Case Study
Taking Oil and Gas Exploration to the Next Level
DownUnder GeoSolutions (DUG) wanted to increase computing performance by 5 to 10 times to improve seismic processing. The solution must build on current architecture software investments without sacrificing existing software and scale computing without scaling IT infrastructure costs.
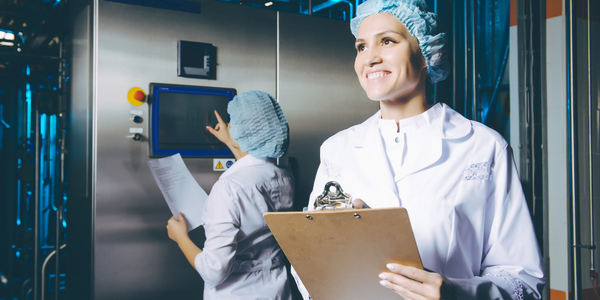
Case Study
Remote Wellhead Monitoring
Each wellhead was equipped with various sensors and meters that needed to be monitored and controlled from a central HMI, often miles away from the assets in the field. Redundant solar and wind generators were installed at each wellhead to support the electrical needs of the pumpstations, temperature meters, cameras, and cellular modules. In addition to asset management and remote control capabilities, data logging for remote surveillance and alarm notifications was a key demand from the customer. Terra Ferma’s solution needed to be power efficient, reliable, and capable of supporting high-bandwidth data-feeds. They needed a multi-link cellular connection to a central server that sustained reliable and redundant monitoring and control of flow meters, temperature sensors, power supply, and event-logging; including video and image files. This open-standard network needed to interface with the existing SCADA and proprietary network management software.
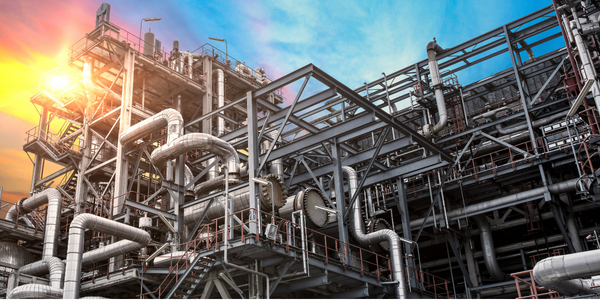
Case Study
Refinery Saves Over $700,000 with Smart Wireless
One of the largest petroleum refineries in the world is equipped to refine various types of crude oil and manufacture various grades of fuel from motor gasoline to Aviation Turbine Fuel. Due to wear and tear, eight hydrogen valves in each refinery were leaking, and each cost $1800 per ton of hydrogen vented. The plant also had leakage on nearly 30 flare control hydrocarbon valves. The refinery wanted a continuous, online monitoring system that could catch leaks early, minimize hydrogen and hydrocarbon production losses, and improve safety for maintenance.
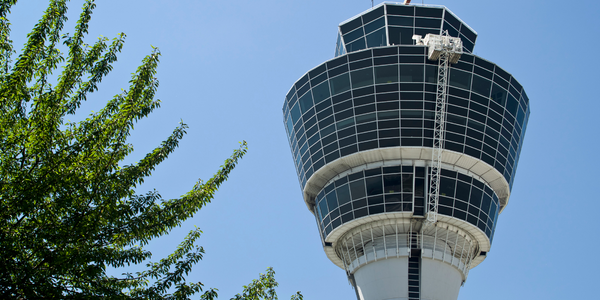
Case Study
Airport SCADA Systems Improve Service Levels
Modern airports are one of the busiest environments on Earth and rely on process automation equipment to ensure service operators achieve their KPIs. Increasingly airport SCADA systems are being used to control all aspects of the operation and associated facilities. This is because unplanned system downtime can cost dearly, both in terms of reduced revenues and the associated loss of customer satisfaction due to inevitable travel inconvenience and disruption.
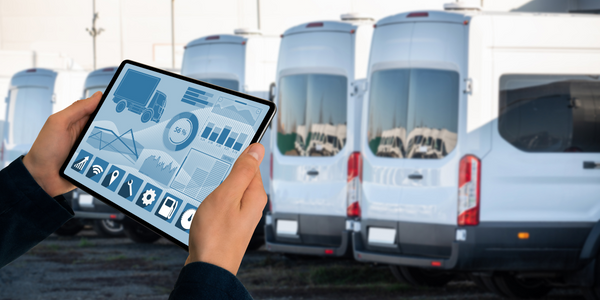
Case Study
IoT-based Fleet Intelligence Innovation
Speed to market is precious for DRVR, a rapidly growing start-up company. With a business model dependent on reliable mobile data, managers were spending their lives trying to negotiate data roaming deals with mobile network operators in different countries. And, even then, service quality was a constant concern.