Customer Company Size
Large Corporate
Country
- United States
Product
- Domo Everywhere
Tech Stack
- IoT sensors
- ERP
- Marketing automation system
Implementation Scale
- Enterprise-wide Deployment
Impact Metrics
- Productivity Improvements
- Customer Satisfaction
Technology Category
- Platform as a Service (PaaS) - Data Management Platforms
Applicable Industries
- Food & Beverage
- Pharmaceuticals
Applicable Functions
- Logistics & Transportation
- Quality Assurance
Use Cases
- Real-Time Location System (RTLS)
- Remote Asset Management
- Supply Chain Visibility
Services
- Data Science Services
About The Customer
Emerson is a manufacturing company with a revenue of $17 billion. The company's Cold Chain business helps a wide range of businesses, from dairies to convenience stores to pharmaceutical manufacturers, maintain the perfect temperature for their perishable products. This is achieved by ensuring that these products stay at the required temperature as they travel throughout the supply chain. Emerson uses real-time traceability throughout the global perishable supply chain to keep products like ice cream solid, food safe, and critical vaccines viable as they make their way from the lab to the pharmacy. The company uses Domo to capture the data its technology creates to ensure its products operate at peak performance. Domo Everywhere allows Emerson to share this data back to customers so they can track and verify temperatures across the supply chain for themselves.
The Challenge
Emerson’s Cold Chain business helps businesses ranging from dairies to convenience stores to pharmaceutical manufacturers to not only keep their perishable products at the perfect temperature, but ensure those products stay at that temperature as they travel throughout the supply chain. Real-time traceability throughout the global perishable supply chain keeps your ice cream solid, your food safe, and critical vaccines viable as they make their way from the lab to the pharmacy. Emerson relies on Domo to capture the data its technology creates to ensure its products operate at peak performance. In addition, Domo Everywhere lets Emerson share this data back to customers so that they can track and verify temperatures across the supply chain for themselves. Dashboards turn the raw data into easily understandable insights that customers can use to make decisions.
The Solution
Emerson uses Domo to enable self-serve analytics so its internal staff can better understand how its products are used. The company also uses Domo to manage its critical business and operations data. For example, the marketing team uses Domo to track how its marketing spend impacts business performance. Emerson connected Domo to its marketing automation system, ERP, content centralization platform and social media platforms. This lets the marketing team track and optimize how and where they are communicating so they can focus on their most productive content and channels. In addition to using Domo to provide more insight to customers, Emerson leverages the data it collects in Domo to serve its customers smarter, ultimately improving the customer experience and allowing it to grow its relationships.
Operational Impact
Case Study missing?
Start adding your own!
Register with your work email and create a new case study profile for your business.
Related Case Studies.
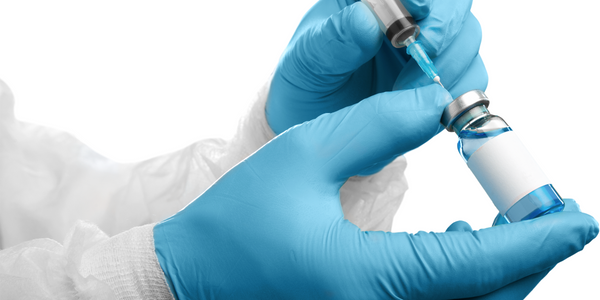
Case Study
Case Study: Pfizer
Pfizer’s high-performance computing software and systems for worldwide research and development support large-scale data analysis, research projects, clinical analytics, and modeling. Pfizer’s computing services are used across the spectrum of research and development efforts, from the deep biological understanding of disease to the design of safe, efficacious therapeutic agents.

Case Study
The Kellogg Company
Kellogg keeps a close eye on its trade spend, analyzing large volumes of data and running complex simulations to predict which promotional activities will be the most effective. Kellogg needed to decrease the trade spend but its traditional relational database on premises could not keep up with the pace of demand.
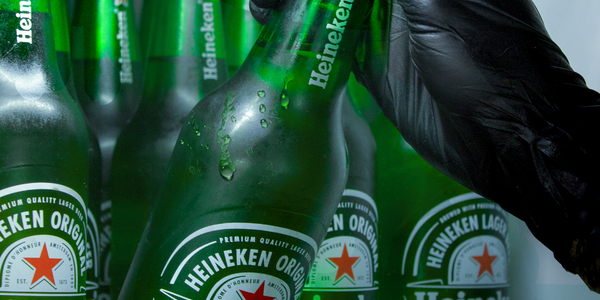
Case Study
HEINEKEN Uses the Cloud to Reach 10.5 Million Consumers
For 2012 campaign, the Bond promotion, it planned to launch the campaign at the same time everywhere on the planet. That created unprecedented challenges for HEINEKEN—nowhere more so than in its technology operation. The primary digital content for the campaign was a 100-megabyte movie that had to play flawlessly for millions of viewers worldwide. After all, Bond never fails. No one was going to tolerate a technology failure that might bruise his brand.Previously, HEINEKEN had supported digital media at its outsourced datacenter. But that datacenter lacked the computing resources HEINEKEN needed, and building them—especially to support peak traffic that would total millions of simultaneous hits—would have been both time-consuming and expensive. Nor would it have provided the geographic reach that HEINEKEN needed to minimize latency worldwide.
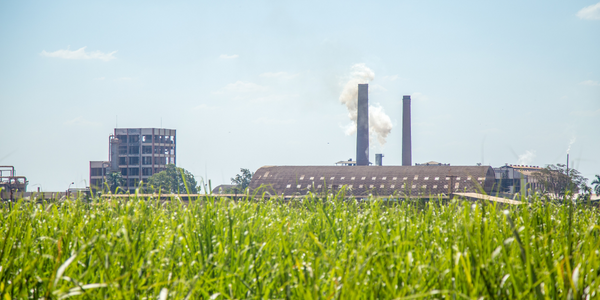
Case Study
Energy Management System at Sugar Industry
The company wanted to use the information from the system to claim under the renewable energy certificate scheme. The benefit to the company under the renewable energy certificates is Rs 75 million a year. To enable the above, an end-to-end solution for load monitoring, consumption monitoring, online data monitoring, automatic meter data acquisition which can be exported to SAP and other applications is required.
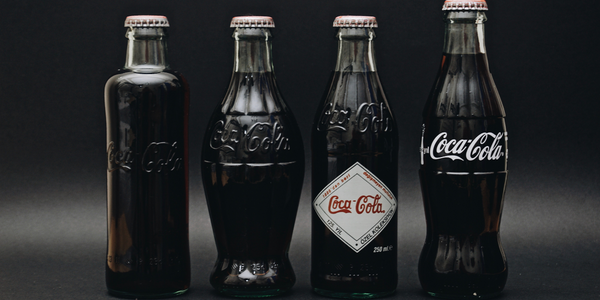
Case Study
Coca Cola Swaziland Conco Case Study
Coco Cola Swaziland, South Africa would like to find a solution that would enable the following results: - Reduce energy consumption by 20% in one year. - Formulate a series of strategic initiatives that would enlist the commitment of corporate management and create employee awareness while helping meet departmental targets and investing in tools that assist with energy management. - Formulate a series of tactical initiatives that would optimize energy usage on the shop floor. These would include charging forklifts and running cold rooms only during off-peak periods, running the dust extractors only during working hours and basing lights and air-conditioning on someone’s presence. - Increase visibility into the factory and other processes. - Enable limited, non-intrusive control functions for certain processes.
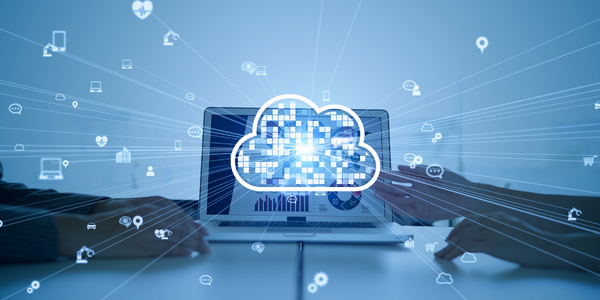
Case Study
Fusion Middleware Integration on Cloud for Pharma Major
Customer wanted a real-time, seamless, cloud based integration between the existing on premise and cloud based application using SOA technology on Oracle Fusion Middleware Platform, a Contingent Worker Solution to collect, track, manage and report information for on-boarding, maintenance and off-boarding of contingent workers using a streamlined and Integrated business process, and streamlining of integration to the back-end systems and multiple SaaS applications.