Customer Company Size
SME
Region
- Europe
Country
- Germany
Product
- DocuWare
- MFG/PRO
- Tobit
- Ascent Capture
Tech Stack
- Document Management System
- ERP System
- Communication Software
- Form Recognition Software
Implementation Scale
- Enterprise-wide Deployment
Impact Metrics
- Productivity Improvements
- Customer Satisfaction
- Cost Savings
Technology Category
- Application Infrastructure & Middleware - Data Exchange & Integration
- Analytics & Modeling - Process Analytics
Applicable Industries
- Aerospace
- Automotive
- Chemicals
Applicable Functions
- Discrete Manufacturing
- Quality Assurance
- Sales & Marketing
Use Cases
- Manufacturing System Automation
- Supply Chain Visibility
Services
- System Integration
- Software Design & Engineering Services
About The Customer
Georg Fischer DEKA GmbH is a pipe system specialist based in Dautphetal, Germany. The company is known for its custom manufacturing to meet the special needs of different industries. Customers from around the world depend on the modern plastic piping systems generated by Georg Fischer DEKA. The company's competitive advantages include its emphasis on top quality and creating very custom products. For example, this plastics manufacturer provides a pipe system for cabin air ventilation on the Airbus 340 and 380. A quick turnaround of products is a key criteria: replacement parts must be delivered within 24 hours. The company has a warehouse filled with more than 500 different pipe dimensions that are all made from a variety of materials, mass-produced or custom-made. The company has a staff of 112 employees.
The Challenge
Georg Fischer DEKA GmbH, a pipe system specialist, was facing a challenge due to the extensive production data they had to archive. The laws surrounding product liability required that all manufacturing documentation is securely retained for more than 50 years. The company was looking for an alternative to archiving with paper due to the increasing storage space requirements. Additionally, the company saw this as an opportunity to re-think and reorganize the way their company communicates. In the past, each work group as well as each individual staffer had their own filing system. Records were manually organized, copied and filed in binders. Then after each year, the documents would be placed in a central storage space, which only an authorized employee could access. The search for any older records was rather difficult and took a lot of time. Any exchange of documents between departments was often problematic and even more time-consuming. Customer inquiries could not be handled quickly, since documents had to be moved within the building via “tube mail.“
The Solution
The company’s leadership decided to create an electronic archive with the help of DocuWare’s sales partner, DMS Vertriebs GmbH. Employees in Order Processing tested the fully automatic filing system for records handled by their ERP system, MFG/PRO from QAD. Within two weeks, the document management system (DMS) was working flawlessly. Today, all of the company’s departments are using the central document pool: Sales, Production, Quality Control, Accounting, Maintenance, Shipping and the Warehouse. Every day about 200 processes – that involve up to 600 sheets of paper – are archived. Various records generated by the ERP system, such as order forms, shipping documents, accounts receivable invoices used to be printed out, photocopied, hole-punched and placed in binders. Now the process happens fully automatically, and all these documents are indexed, using built-in customer numbers and names, organized and safely stored. Any authorized personnel can then access these same documents with a click of a mouse. Invoices can still be printed and sent by mail to a customer. Records from the central document pool can also be printed into an electronic basket and then sent by fax or e-mail using the communication software Tobit.
Operational Impact
Quantitative Benefit
Case Study missing?
Start adding your own!
Register with your work email and create a new case study profile for your business.
Related Case Studies.
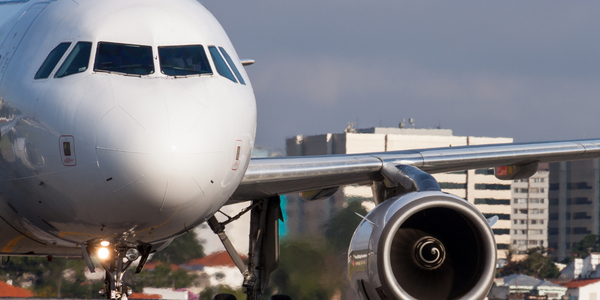
Case Study
Airbus Soars with Wearable Technology
Building an Airbus aircraft involves complex manufacturing processes consisting of thousands of moving parts. Speed and accuracy are critical to business and competitive advantage. Improvements in both would have high impact on Airbus’ bottom line. Airbus wanted to help operators reduce the complexity of assembling cabin seats and decrease the time required to complete this task.
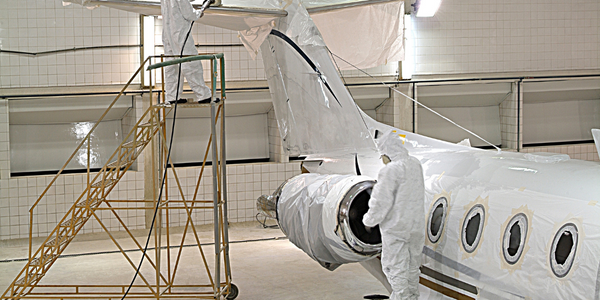
Case Study
Aircraft Predictive Maintenance and Workflow Optimization
First, aircraft manufacturer have trouble monitoring the health of aircraft systems with health prognostics and deliver predictive maintenance insights. Second, aircraft manufacturer wants a solution that can provide an in-context advisory and align job assignments to match technician experience and expertise.
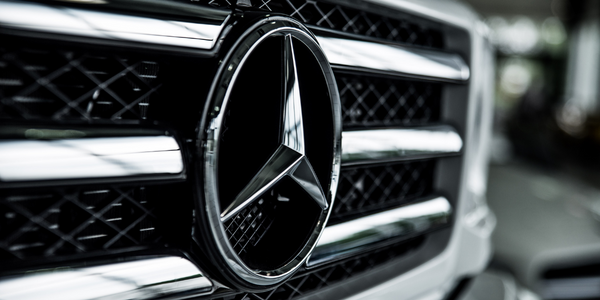
Case Study
Integral Plant Maintenance
Mercedes-Benz and his partner GAZ chose Siemens to be its maintenance partner at a new engine plant in Yaroslavl, Russia. The new plant offers a capacity to manufacture diesel engines for the Russian market, for locally produced Sprinter Classic. In addition to engines for the local market, the Yaroslavl plant will also produce spare parts. Mercedes-Benz Russia and his partner needed a service partner in order to ensure the operation of these lines in a maintenance partnership arrangement. The challenges included coordinating the entire maintenance management operation, in particular inspections, corrective and predictive maintenance activities, and the optimizing spare parts management. Siemens developed a customized maintenance solution that includes all electronic and mechanical maintenance activities (Integral Plant Maintenance).
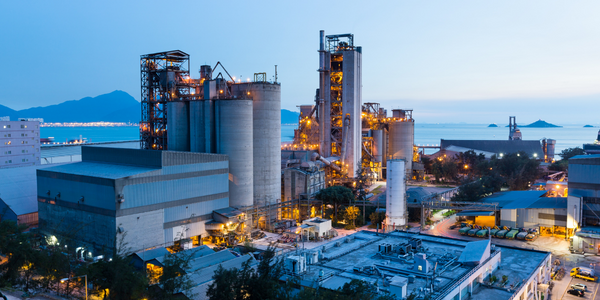
Case Study
Honeywell - Tata Chemicals Improves Data Accessibility with OneWireless
Tata was facing data accessibility challenges in the cement plant control room tapping signals from remote process control areas and other distant locations, including the gas scrubber. Tata needed a wireless solution to extend its control network securely to remote locations that would also provide seamless communication with existing control applications.