Technology Category
- Functional Applications - Computerized Maintenance Management Systems (CMMS)
Applicable Industries
- Paper & Pulp
Applicable Functions
- Maintenance
- Product Research & Development
Use Cases
- Supply Chain Visibility
- Time Sensitive Networking
Services
- Testing & Certification
About The Customer
GG Group, also known as Gebauer & Griller, is a leading global manufacturer of cables, wires, and cable harnesses. The company's products are used in most of today's vehicles and many of the world's elevators, transformers, motors, and photovoltaic arrays. Founded in 1940 as a family-run trading agency for raw materials and semi-finished products, GG Group has since expanded its product lines and office locations into 13 different locations, including the United States, Germany, India, China, and Mexico. The company employs 4,500 people across the globe.
The Challenge
GG Group, a global manufacturer of cables, wires, and cable harnesses, faced significant challenges in its budget allocation and process standardization. The company relied heavily on spreadsheets and paper forms to prepare budgets and allocate resources, which resulted in a lack of visibility and wasted time in status meetings. The company's operations were fragmented due to various methods of project management employed by its employees. Additionally, GG Group faced the challenge of ensuring consistency across its 4,500 employees worldwide. The company's key engineering process, Variant Development, was heavily dependent on individual employees and their personal knowledge of various processes. This resulted in a process that took six to 12 months and required more than 100 employees across multiple locations.
The Solution
GG Group implemented K2 Software to transform its financial approval process and Variant Development. The software accelerated the financial approval process, cutting the time for investment requests in half and saving a significant number of employee hours each year. This led to faster business decisions, more strategic funding allocation, and instant visibility into operations. In terms of process standardization, K2 Software automated up to 60 individual process steps in Variant Development. This resulted in product variations being fully tested and ready for production on time. The software also ensured that all employees followed the same standardized processes, removing inconsistencies and redundancies. The automated workflows managed themselves, freeing up employees to be more efficient and ensuring consistent product quality.
Operational Impact
Quantitative Benefit
Case Study missing?
Start adding your own!
Register with your work email and create a new case study profile for your business.
Related Case Studies.
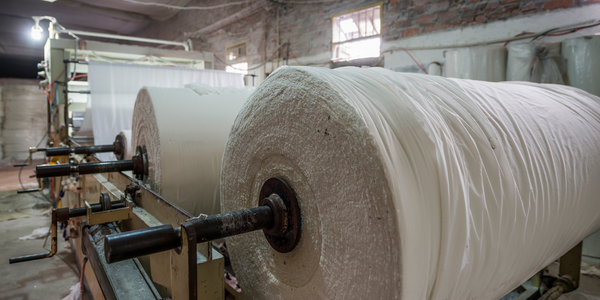
Case Study
Wireless Improves Efficiency in Compressed Air Systems
Hollingsworth and Vose wanted to improve the efficiency of their compressed air system, lower the electricity expense component of manufacturing cost in their commodity industry, and conserve energy leading to lowered greenhouse gas emissions. Compressed air systems degrade over time and become leaky and inefficient. Hollingsworth and Vose wanted to increase the frequency of system inspections without paying the high cost of manual labor.
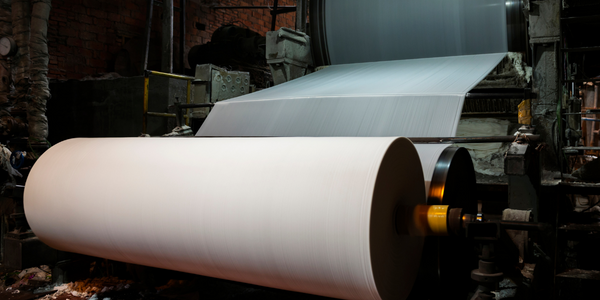
Case Study
Process Predictive Analysis in Pulp and Paper Mill
Common paper breaks consequently lead up to 60 minutes of downtime, delaying a potential $10K per hour of production value process. Thus, defective products cause financial and damage company's reputation. Improving quality and reducing defect rates can generate millions of dollars of revenue per year for your company.
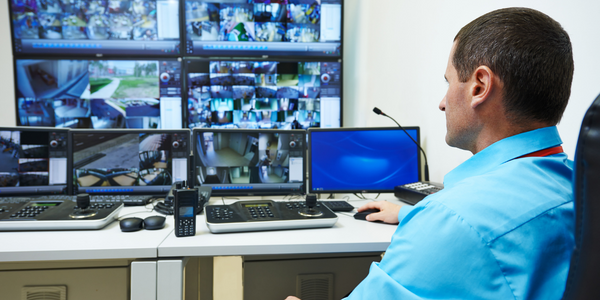
Case Study
Industrial Video Monitoring for Security and Regulatory Compliance
Because of the Stevenson mill’s proximity to the Tennessee River, WestRock was required by the USCG to comply with the Maritime Security 33CFR (MARSEC) regulations. WestRock needed a video security system but wanted to add other applications not required by the government, such as video process monitoring, condition monitoring, and wireless network management. WestRock needed a reliable video solution to avoid the compliance fines and possible security risks – but the solution needed to be implemented in the most cost-effective manner possible.
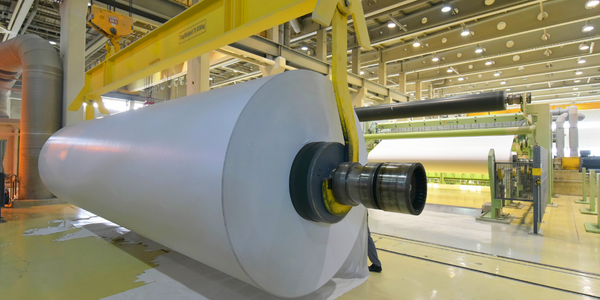
Case Study
ECOsine Active Increased Reliability in the Paper Industry
The paper and pulp industry is interlinking intelligent hi-tech machines to highly efficient production lines. Higher power DC and AC motor drives perform the automation tasks. Every kind of interference that negatively affects the reliability and safety of the installation may lead to production downtime and consequently to significant financial losses. AC and DC motor drives are so-called non-linear loads as they draw a nonsinusoidal current from the grid. Resulting harmonics of current and voltage can interfere with the operation of nearby consumers and overload the electrical infrastructure. In this particular application, the load cycles of the drives often caused interruptions in the production process because of disturbances coupling into the fieldbus system.