Technology Category
- Functional Applications - Computerized Maintenance Management Systems (CMMS)
- Sensors - Environmental Sensors
Applicable Industries
- Oil & Gas
- Renewable Energy
Applicable Functions
- Maintenance
- Product Research & Development
Use Cases
- Farm Monitoring & Precision Farming
- Indoor Air Quality Monitoring
About The Customer
The primary customer in this case study is Equinor, formerly known as Statoil, a Norwegian multinational energy company. Equinor is heavily invested in the development of floating wind turbines, having installed the first fully-operational floating wind farm, Hywind Scotland, in 2017. The company is committed to driving down the costs of floating offshore wind and improving efficiency. Equinor is also mindful of the environmental impact of their operations, working closely with environmental organizations to mitigate potential hazards to bird migrations. The company's efforts in the field of floating wind turbines position it as a leader in the renewable energy sector.
The Challenge
The offshore wind energy sector is looking towards floating wind turbines as the future of renewable energy. Norway, a country with a strong background in the oil and gas industry, is leading the way in this development. However, the implementation of floating wind turbines presents several challenges. The depth of the ocean off the Norwegian coast necessitates the use of floating turbines, which are more complex and costly to develop than their fixed counterparts. Additionally, the environmental, technical, and economic challenges surrounding these structures are significant. These include the potential hazard they pose to bird migrations, the difficulty of maintaining structures far out at sea, and the high costs associated with developing and mounting these massive steel structures.
The Solution
Despite these challenges, progress is being made in the development of floating wind turbines. Since 2007, prototypes have been installed off the coasts of several countries, including Norway, Italy, Portugal, Sweden, Japan, and the United States. In 2017, the first fully-operational floating wind farm, Hywind Scotland, was installed off the coast of Aberdeen. Developed by Norwegian oil and gas company, Statoil (now Equinor), Hywind has six floating turbines with a total capacity of 30 MW. To address the issue of bird migrations, collaborations with environmental organizations are underway to ensure that the turbines do not negatively impact local ecosystems. Furthermore, technology is being developed to improve efficiency and drive down costs. Equinor aims to bring the cost of floating offshore wind down to $50–74 per MWh by 2030.
Operational Impact
Quantitative Benefit
Case Study missing?
Start adding your own!
Register with your work email and create a new case study profile for your business.
Related Case Studies.

Case Study
Remote Monitoring & Predictive Maintenance App for a Solar Energy System
The maintenance & tracking of various modules was an overhead for the customer due to the huge labor costs involved. Being an advanced solar solutions provider, they wanted to ensure early detection of issues and provide the best-in-class customer experience. Hence they wanted to automate the whole process.
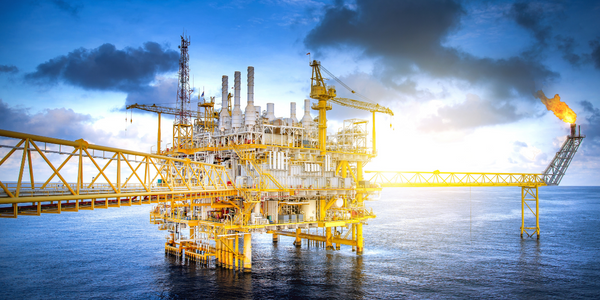
Case Study
Taking Oil and Gas Exploration to the Next Level
DownUnder GeoSolutions (DUG) wanted to increase computing performance by 5 to 10 times to improve seismic processing. The solution must build on current architecture software investments without sacrificing existing software and scale computing without scaling IT infrastructure costs.
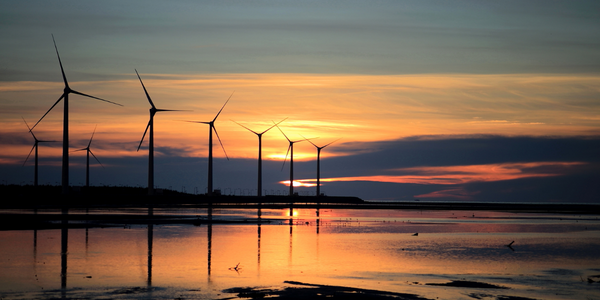
Case Study
Vestas: Turning Climate into Capital with Big Data
Making wind a reliable source of energy depends greatly on the placement of the wind turbines used to produce electricity. Turbulence is a significant factor as it strains turbine components, making them more likely to fail. Vestas wanted to pinpoint the optimal location for wind turbines to maximize power generation and reduce energy costs.
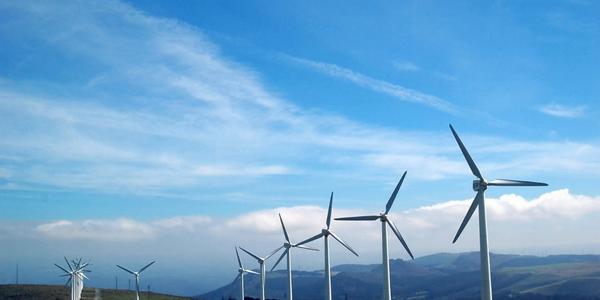
Case Study
Siemens Wind Power
Wind provides clean, renewable energy. The core concept is simple: wind turbines spin blades to generate power. However, today's systems are anything but simple. Modern wind turbines have blades that sweep a 120 meter circle, cost more than 1 million dollars and generate multiple megawatts of power. Each turbine may include up to 1,000 sensors and actuators – integrating strain gages, bearing monitors and power conditioning technology. The turbine can control blade speed and power generation by altering the blade pitch and power extraction. Controlling the turbine is a sophisticated job requiring many cooperating processors closing high-speed loops and implementing intelligent monitoring and optimization algorithms. But the real challenge is integrating these turbines so that they work together. A wind farm may include hundreds of turbines. They are often installed in difficult-to-access locations at sea. The farm must implement a fundamentally and truly distributed control system. Like all power systems, the goal of the farm is to match generation to load. A farm with hundreds of turbines must optimize that load by balancing the loading and generation across a wide geography. Wind, of course, is dynamic. Almost every picture of a wind farm shows a calm sea and a setting sun. But things get challenging when a storm goes through the wind farm. In a storm, the control system must decide how to take energy out of gusts to generate constant power. It must intelligently balance load across many turbines. And a critical consideration is the loading and potential damage to a half-billion-dollar installed asset. This is no environment for a slow or undependable control system. Reliability and performance are crucial.
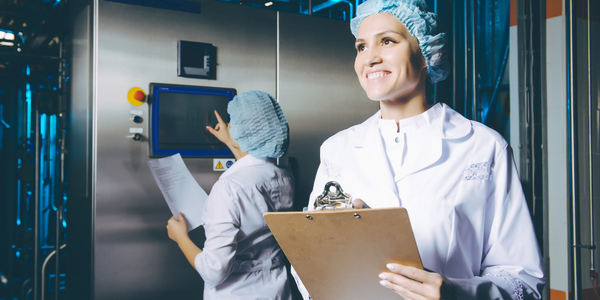
Case Study
Remote Wellhead Monitoring
Each wellhead was equipped with various sensors and meters that needed to be monitored and controlled from a central HMI, often miles away from the assets in the field. Redundant solar and wind generators were installed at each wellhead to support the electrical needs of the pumpstations, temperature meters, cameras, and cellular modules. In addition to asset management and remote control capabilities, data logging for remote surveillance and alarm notifications was a key demand from the customer. Terra Ferma’s solution needed to be power efficient, reliable, and capable of supporting high-bandwidth data-feeds. They needed a multi-link cellular connection to a central server that sustained reliable and redundant monitoring and control of flow meters, temperature sensors, power supply, and event-logging; including video and image files. This open-standard network needed to interface with the existing SCADA and proprietary network management software.