技术
- 功能应用 - 计算机化维护管理系统 (CMMS)
- 传感器 - 环境传感器
适用行业
- 石油和天然气
- 可再生能源
适用功能
- 维护
- 产品研发
用例
- 农场监控与精准农业
- 室内空气质量监测
关于客户
本案例研究中的主要客户是 Equinor(前身为 Statoil),一家挪威跨国能源公司。 Equinor大力投资浮动式风力发电机的开发,于2017年安装了第一个全面运营的浮动式风电场Hywind Scotland。该公司致力于降低浮动式海上风电的成本并提高效率。 Equinor 还关注其运营对环境的影响,与环保组织密切合作,以减轻鸟类迁徙的潜在危害。该公司在浮动风力涡轮机领域的努力使其成为可再生能源领域的领导者。
挑战
海上风能行业正在将浮动风力涡轮机视为可再生能源的未来。挪威是一个在石油和天然气行业拥有强大背景的国家,在这一发展方面处于领先地位。然而,浮动风力涡轮机的实施面临着一些挑战。挪威海岸附近的海洋深度需要使用浮动涡轮机,与固定涡轮机相比,浮动涡轮机的开发更加复杂且成本更高。此外,围绕这些结构的环境、技术和经济挑战也很严峻。其中包括它们对鸟类迁徙造成的潜在危害、在远海维护结构的难度以及开发和安装这些大型钢结构相关的高成本。
解决方案
尽管存在这些挑战,浮动风力涡轮机的开发仍在取得进展。自 2007 年以来,原型机已安装在多个国家的沿海地区,包括挪威、意大利、葡萄牙、瑞典、日本和美国。 2017 年,第一个全面运营的浮动风电场 Hywind Scotland 在阿伯丁海岸安装。 Hywind 由挪威石油天然气公司 Statoil(现为 Equinor)开发,拥有六台浮动涡轮机,总容量为 30 MW。为了解决鸟类迁徙问题,我们正在与环保组织合作,以确保涡轮机不会对当地生态系统产生负面影响。此外,正在开发技术以提高效率并降低成本。 Equinor 的目标是到 2030 年将浮动海上风电的成本降至每兆瓦时 50-74 美元。
运营影响
数量效益
Case Study missing?
Start adding your own!
Register with your work email and create a new case study profile for your business.
相关案例.

Case Study
Remote Monitoring & Predictive Maintenance App for a Solar Energy System
The maintenance & tracking of various modules was an overhead for the customer due to the huge labor costs involved. Being an advanced solar solutions provider, they wanted to ensure early detection of issues and provide the best-in-class customer experience. Hence they wanted to automate the whole process.
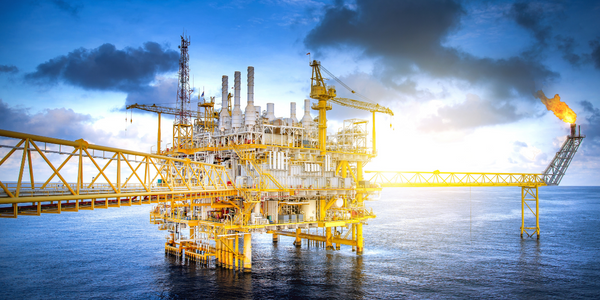
Case Study
Taking Oil and Gas Exploration to the Next Level
DownUnder GeoSolutions (DUG) wanted to increase computing performance by 5 to 10 times to improve seismic processing. The solution must build on current architecture software investments without sacrificing existing software and scale computing without scaling IT infrastructure costs.
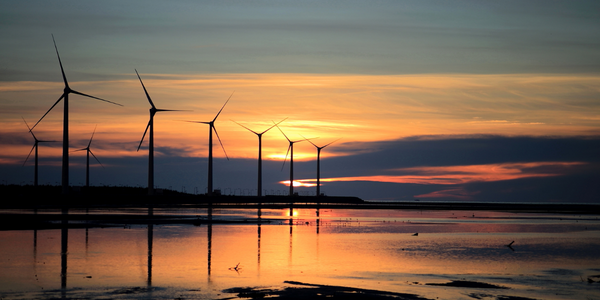
Case Study
Vestas: Turning Climate into Capital with Big Data
Making wind a reliable source of energy depends greatly on the placement of the wind turbines used to produce electricity. Turbulence is a significant factor as it strains turbine components, making them more likely to fail. Vestas wanted to pinpoint the optimal location for wind turbines to maximize power generation and reduce energy costs.
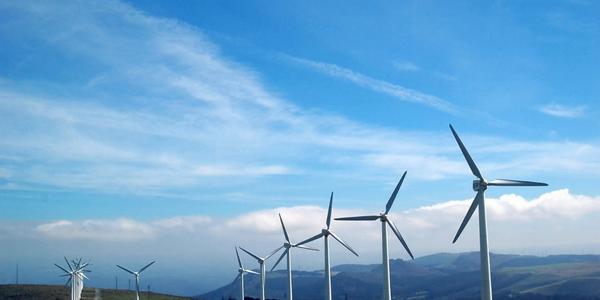
Case Study
Siemens Wind Power
Wind provides clean, renewable energy. The core concept is simple: wind turbines spin blades to generate power. However, today's systems are anything but simple. Modern wind turbines have blades that sweep a 120 meter circle, cost more than 1 million dollars and generate multiple megawatts of power. Each turbine may include up to 1,000 sensors and actuators – integrating strain gages, bearing monitors and power conditioning technology. The turbine can control blade speed and power generation by altering the blade pitch and power extraction. Controlling the turbine is a sophisticated job requiring many cooperating processors closing high-speed loops and implementing intelligent monitoring and optimization algorithms. But the real challenge is integrating these turbines so that they work together. A wind farm may include hundreds of turbines. They are often installed in difficult-to-access locations at sea. The farm must implement a fundamentally and truly distributed control system. Like all power systems, the goal of the farm is to match generation to load. A farm with hundreds of turbines must optimize that load by balancing the loading and generation across a wide geography. Wind, of course, is dynamic. Almost every picture of a wind farm shows a calm sea and a setting sun. But things get challenging when a storm goes through the wind farm. In a storm, the control system must decide how to take energy out of gusts to generate constant power. It must intelligently balance load across many turbines. And a critical consideration is the loading and potential damage to a half-billion-dollar installed asset. This is no environment for a slow or undependable control system. Reliability and performance are crucial.
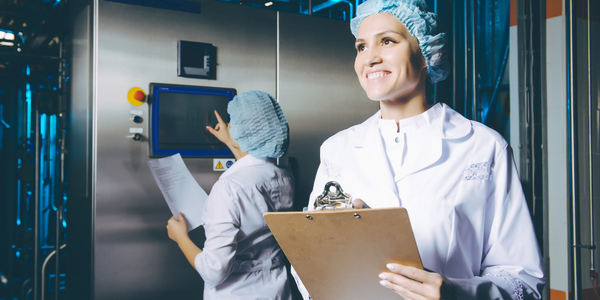
Case Study
Remote Wellhead Monitoring
Each wellhead was equipped with various sensors and meters that needed to be monitored and controlled from a central HMI, often miles away from the assets in the field. Redundant solar and wind generators were installed at each wellhead to support the electrical needs of the pumpstations, temperature meters, cameras, and cellular modules. In addition to asset management and remote control capabilities, data logging for remote surveillance and alarm notifications was a key demand from the customer. Terra Ferma’s solution needed to be power efficient, reliable, and capable of supporting high-bandwidth data-feeds. They needed a multi-link cellular connection to a central server that sustained reliable and redundant monitoring and control of flow meters, temperature sensors, power supply, and event-logging; including video and image files. This open-standard network needed to interface with the existing SCADA and proprietary network management software.