Customer Company Size
Large Corporate
Country
- United States
Product
- Honeywell Forge Production Intelligence
- Experion Operations Assistant
- Field Process Knowledge System
Tech Stack
- Generative AI
- Cloud-native platform
- Advanced analytics
Implementation Scale
- Enterprise-wide Deployment
Impact Metrics
- Productivity Improvements
- Digital Expertise
- Innovation Output
Technology Category
- Analytics & Modeling - Generative AI
- Functional Applications - Remote Monitoring & Control Systems
Applicable Functions
- Process Manufacturing
- Business Operation
Use Cases
- Predictive Maintenance
- Process Control & Optimization
- Root Cause Analysis & Diagnosis
Services
- Software Design & Engineering Services
- System Integration
About The Customer
The target customers for Honeywell's latest generative AI assistance are industrial operators, production managers, engineers, plant managers, and business leaders in large corporate settings. These customers are typically involved in complex industrial operations where performance monitoring and troubleshooting are critical to maintaining efficiency and productivity. They require advanced tools that can provide key insights through natural language prompts, enabling them to visualize, trend, and troubleshoot production issues effectively. The customers are likely to be part of industries that demand high levels of operational efficiency and innovation, where the integration of AI-enabled solutions can significantly enhance their capabilities.
The Challenge
Industrial operators and production managers face challenges in automating tasks and troubleshooting problems efficiently. The need for seamless integration of performance monitoring with advanced analytics is crucial to enhance productivity and operational efficiency. Traditional methods of accessing insights and troubleshooting production issues can be time-consuming and complex, requiring a more intuitive and user-friendly approach. The industry demands solutions that can provide rapid root cause analysis and support closed-loop collaboration workflows to streamline operations.
The Solution
Honeywell has introduced the latest release of Honeywell Forge Production Intelligence, a cloud-native platform that integrates performance monitoring with advanced analytics and a new generative AI assistant. The Intelligent Assistant is designed to enhance user experience by allowing users to access key insights through simple, natural language prompts. This tool enables industrials to visualize, trend, and troubleshoot production issues from KPI deviation contributors and asset relationships. The platform supports rapid root cause analysis of production issues, enhancing AI insights with greater explainability and usability. It also facilitates closed-loop collaboration workflows with case management integration, streamlining operations and improving productivity.
Operational Impact
Case Study missing?
Start adding your own!
Register with your work email and create a new case study profile for your business.
Related Case Studies.

Case Study
Remote Monitoring & Predictive Maintenance App for a Solar Energy System
The maintenance & tracking of various modules was an overhead for the customer due to the huge labor costs involved. Being an advanced solar solutions provider, they wanted to ensure early detection of issues and provide the best-in-class customer experience. Hence they wanted to automate the whole process.
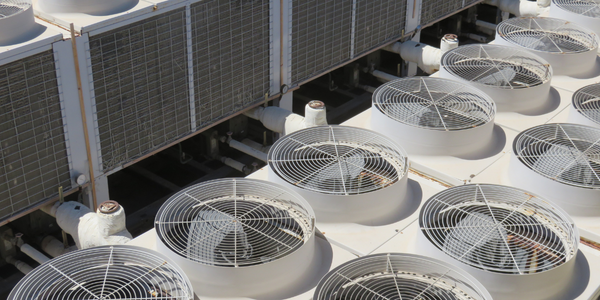
Case Study
Predictive Maintenance for Industrial Chillers
For global leaders in the industrial chiller manufacturing, reliability of the entire production process is of the utmost importance. Chillers are refrigeration systems that produce ice water to provide cooling for a process or industrial application. One of those leaders sought a way to respond to asset performance issues, even before they occur. The intelligence to guarantee maximum reliability of cooling devices is embedded (pre-alarming). A pre-alarming phase means that the cooling device still works, but symptoms may appear, telling manufacturers that a failure is likely to occur in the near future. Chillers who are not internet connected at that moment, provide little insight in this pre-alarming phase.
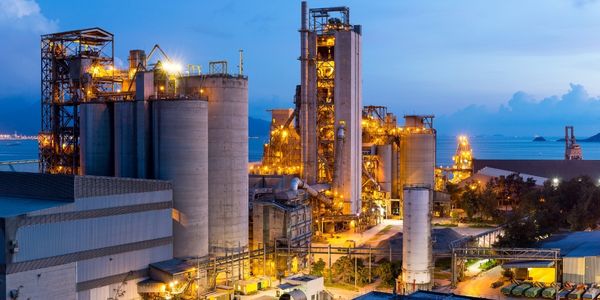
Case Study
System 800xA at Indian Cement Plants
Chettinad Cement recognized that further efficiencies could be achieved in its cement manufacturing process. It looked to investing in comprehensive operational and control technologies to manage and derive productivity and energy efficiency gains from the assets on Line 2, their second plant in India.
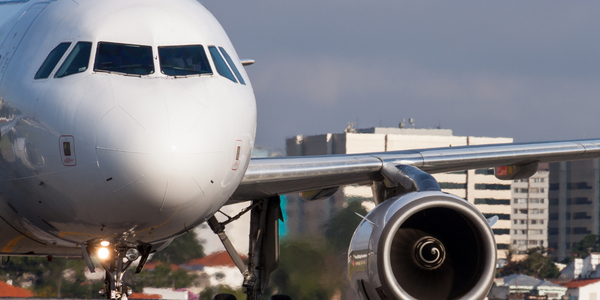
Case Study
Airbus Soars with Wearable Technology
Building an Airbus aircraft involves complex manufacturing processes consisting of thousands of moving parts. Speed and accuracy are critical to business and competitive advantage. Improvements in both would have high impact on Airbus’ bottom line. Airbus wanted to help operators reduce the complexity of assembling cabin seats and decrease the time required to complete this task.
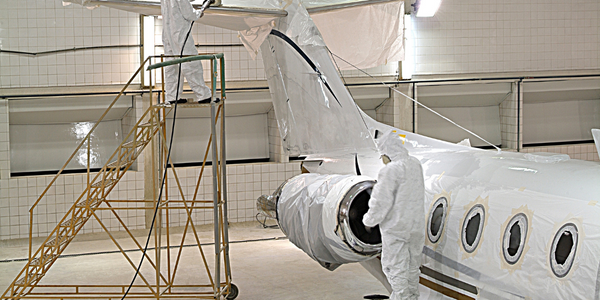
Case Study
Aircraft Predictive Maintenance and Workflow Optimization
First, aircraft manufacturer have trouble monitoring the health of aircraft systems with health prognostics and deliver predictive maintenance insights. Second, aircraft manufacturer wants a solution that can provide an in-context advisory and align job assignments to match technician experience and expertise.