Applicable Industries
- Oil & Gas
Applicable Functions
- Quality Assurance
Use Cases
- Visual Quality Detection
Services
- Testing & Certification
About The Customer
HubSpot is a global leader in the provision of inbound marketing, sales, and service software. The company is publicly traded on the New York Stock Exchange under the ticker symbol HUBS. HubSpot's talent acquisition team is committed to recruiting the right people and using a personalized approach to achieve that. They value interactions that are useful and relevant, and they strive to maintain a strong pipeline of diverse candidates. The company's commitment to quality over quantity in their recruitment process led them to seek a solution that could streamline their sourcing processes and improve the quality of their outreach.
The Challenge
HubSpot, a leading provider of inbound marketing, sales, and service software, faced significant challenges in its recruitment process. The process of gathering candidate information was manual and time-consuming, often involving extensive searches through Google, Stack Overflow, GitHub, and other platforms. This made it difficult to engage passive candidates through cold outreach, as the messages often lacked personalization and relevance. Additionally, HubSpot had a pressing need to source diverse candidates and maintain a strong pipeline of candidates, which was proving to be a difficult task with their existing methods.
The Solution
HubSpot turned to Entelo, a recruitment platform that provides access to a rich database of social profiles, to address their recruitment challenges. Entelo's software provided HubSpot with access to millions of candidates, complete with their social footprints, all in a single interface. This allowed HubSpot's team to source candidates from underrepresented groups right within the platform. Furthermore, Entelo's email analytics solution enabled HubSpot to boost candidate response rates by double-digit percentages. The platform also allowed HubSpot's team to personalize their outreach, making candidates feel like the messages were directly targeted at them. This focus on quality over quantity aligned perfectly with HubSpot's talent acquisition strategy.
Operational Impact
Quantitative Benefit
Case Study missing?
Start adding your own!
Register with your work email and create a new case study profile for your business.
Related Case Studies.
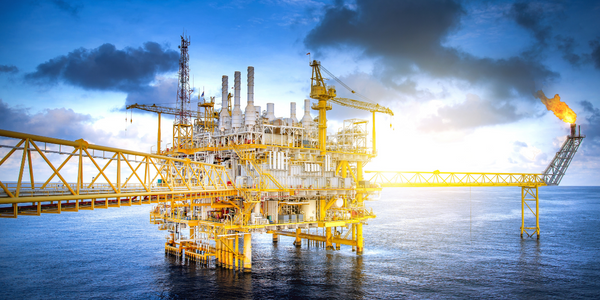
Case Study
Taking Oil and Gas Exploration to the Next Level
DownUnder GeoSolutions (DUG) wanted to increase computing performance by 5 to 10 times to improve seismic processing. The solution must build on current architecture software investments without sacrificing existing software and scale computing without scaling IT infrastructure costs.
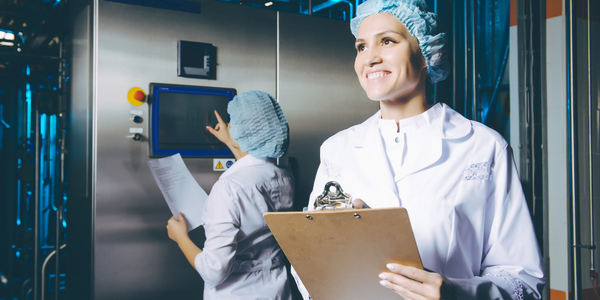
Case Study
Remote Wellhead Monitoring
Each wellhead was equipped with various sensors and meters that needed to be monitored and controlled from a central HMI, often miles away from the assets in the field. Redundant solar and wind generators were installed at each wellhead to support the electrical needs of the pumpstations, temperature meters, cameras, and cellular modules. In addition to asset management and remote control capabilities, data logging for remote surveillance and alarm notifications was a key demand from the customer. Terra Ferma’s solution needed to be power efficient, reliable, and capable of supporting high-bandwidth data-feeds. They needed a multi-link cellular connection to a central server that sustained reliable and redundant monitoring and control of flow meters, temperature sensors, power supply, and event-logging; including video and image files. This open-standard network needed to interface with the existing SCADA and proprietary network management software.
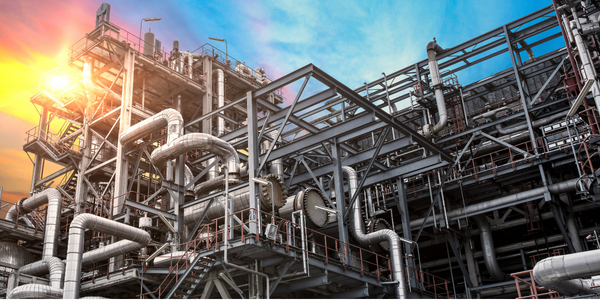
Case Study
Refinery Saves Over $700,000 with Smart Wireless
One of the largest petroleum refineries in the world is equipped to refine various types of crude oil and manufacture various grades of fuel from motor gasoline to Aviation Turbine Fuel. Due to wear and tear, eight hydrogen valves in each refinery were leaking, and each cost $1800 per ton of hydrogen vented. The plant also had leakage on nearly 30 flare control hydrocarbon valves. The refinery wanted a continuous, online monitoring system that could catch leaks early, minimize hydrogen and hydrocarbon production losses, and improve safety for maintenance.