Customer Company Size
SME
Region
- America
Country
- United States
Product
- E2 Web-based Shop System
Tech Stack
- SaaS
Implementation Scale
- Enterprise-wide Deployment
Impact Metrics
- Productivity Improvements
- Cost Savings
Technology Category
- Platform as a Service (PaaS) - Connectivity Platforms
Applicable Functions
- Discrete Manufacturing
Use Cases
- Inventory Management
- Remote Asset Management
Services
- Cloud Planning, Design & Implementation Services
- Training
About The Customer
The National Flag Company is a custom flag manufacturing company based in the United States. The company has a rich history and tradition, having been in operation for 150 years. Despite their long history, they have largely been making flags the same way they did in the 1950s. The company was looking for a major upgrade that would help them communicate better in the shop, log profit margins, and track employee time. They do a lot of custom manufacturing jobs and were struggling with tracking their orders.
The Challenge
The National Flag Company was struggling with a lack of communication in the shop, inability to log profit margins, and difficulty tracking employee time. They were doing a lot of custom manufacturing jobs but had no system in place to track their orders. Their old system did not allow them to track jobs or costs, and they had to manually back up their data and host it on their own server, which incurred additional costs. They were also unable to work remotely, which limited their flexibility and efficiency.
The Solution
The National Flag Company implemented the E2 Web-based Shop System, a SaaS product that allowed them to track inventory and see where they were making or losing money on jobs. The system improved their production process by allowing orders to move easily through modules from estimating to shipping, improving communication between departments. The company also benefited from the system's remote capabilities, which allowed them to check in on job statuses and day-to-day operations from anywhere with an internet connection. The company took advantage of several different training methods to learn how to use the system, including online classes, phone-in classes, and the Shoptech Community.
Operational Impact
Case Study missing?
Start adding your own!
Register with your work email and create a new case study profile for your business.
Related Case Studies.
.png)
Case Study
Improving Vending Machine Profitability with the Internet of Things (IoT)
The vending industry is undergoing a sea change, taking advantage of new technologies to go beyond just delivering snacks to creating a new retail location. Intelligent vending machines can be found in many public locations as well as company facilities, selling different types of goods and services, including even computer accessories, gold bars, tickets, and office supplies. With increasing sophistication, they may also provide time- and location-based data pertaining to sales, inventory, and customer preferences. But at the end of the day, vending machine operators know greater profitability is driven by higher sales and lower operating costs.
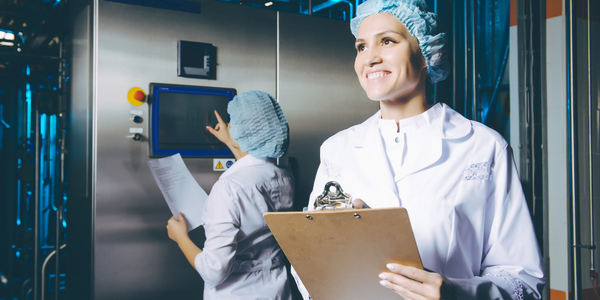
Case Study
Remote Wellhead Monitoring
Each wellhead was equipped with various sensors and meters that needed to be monitored and controlled from a central HMI, often miles away from the assets in the field. Redundant solar and wind generators were installed at each wellhead to support the electrical needs of the pumpstations, temperature meters, cameras, and cellular modules. In addition to asset management and remote control capabilities, data logging for remote surveillance and alarm notifications was a key demand from the customer. Terra Ferma’s solution needed to be power efficient, reliable, and capable of supporting high-bandwidth data-feeds. They needed a multi-link cellular connection to a central server that sustained reliable and redundant monitoring and control of flow meters, temperature sensors, power supply, and event-logging; including video and image files. This open-standard network needed to interface with the existing SCADA and proprietary network management software.
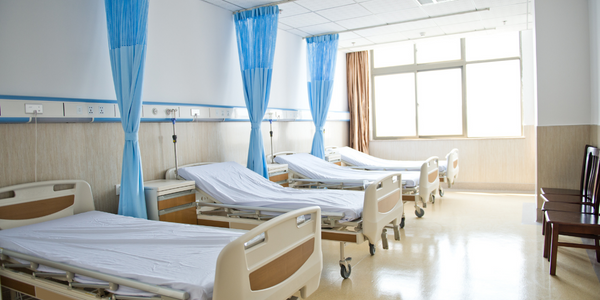
Case Study
Hospital Inventory Management
The hospital supply chain team is responsible for ensuring that the right medical supplies are readily available to clinicians when and where needed, and to do so in the most efficient manner possible. However, many of the systems and processes in use at the cancer center for supply chain management were not best suited to support these goals. Barcoding technology, a commonly used method for inventory management of medical supplies, is labor intensive, time consuming, does not provide real-time visibility into inventory levels and can be prone to error. Consequently, the lack of accurate and real-time visibility into inventory levels across multiple supply rooms in multiple hospital facilities creates additional inefficiency in the system causing over-ordering, hoarding, and wasted supplies. Other sources of waste and cost were also identified as candidates for improvement. Existing systems and processes did not provide adequate security for high-cost inventory within the hospital, which was another driver of cost. A lack of visibility into expiration dates for supplies resulted in supplies being wasted due to past expiry dates. Storage of supplies was also a key consideration given the location of the cancer center’s facilities in a dense urban setting, where space is always at a premium. In order to address the challenges outlined above, the hospital sought a solution that would provide real-time inventory information with high levels of accuracy, reduce the level of manual effort required and enable data driven decision making to ensure that the right supplies were readily available to clinicians in the right location at the right time.