Customer Company Size
Large Corporate
Country
- Other
Product
- Cognito
- Cognito Detect
- Vectra Threat Certainty Index
Tech Stack
- AI-based Network Detection and Response (NDR)
- Endpoint Detection and Response (EDR)
- Security Information and Event Management (SIEM)
Implementation Scale
- Enterprise-wide Deployment
Impact Metrics
- Productivity Improvements
- Digital Expertise
Technology Category
- Analytics & Modeling - Machine Learning
- Cybersecurity & Privacy - Network Security
Applicable Functions
- Discrete Manufacturing
- Business Operation
Use Cases
- Predictive Maintenance
- Cybersecurity
Services
- System Integration
- Data Science Services
About The Customer
INDEVCO is a multinational manufacturing and industrial consultancy group founded in 1955. The company produces a wide portfolio of corrugated, paper, and plastic raw materials and packaging, jumbo tissue rolls, consumer and away-from-home disposables, renewable energy solutions, converting machinery, and CNC machined parts. They serve a wide array of industries in nearly 90 countries worldwide, motivated by a grounding principle of sustainable development underscoring their dedication to integrating environmental sustainability and social responsibility in their operations. With over 38 manufacturing plants and 38 commercial companies across the globe, INDEVCO needed a solution to help them better protect data and keep their operations running smoothly.
The Challenge
INDEVCO, a multinational manufacturing and industrial consultancy group, was facing challenges in detecting internal threats, gaining visibility into their network, and maintaining network hygiene. They had an open-source security information and event management (SIEM) solution and an endpoint detection and response (EDR) solution, but these were not sufficient. The company needed a solution that could help them better protect data and keep their operations running smoothly across their 38 manufacturing plants and 38 commercial companies worldwide.
The Solution
INDEVCO chose Cognito, the AI-driven threat detection and response platform from Vectra, to develop a new security layer for their security operations center (SOC). The Cognito platform collects and stores the right network metadata and enriches it with unique security insights. Cognito Detect uses security enriched metadata and sophisticated machine learning techniques to detect and prioritize attacks in real time. It applies AI-derived machine learning algorithms to automatically detect and respond to in-progress cyberattack behaviors in cloud/SaaS, data center, IoT, and enterprise networks. The solution provides broad visibility into threat history and significantly reduces the chance that attackers can operate on the network long enough to accomplish their goals.
Operational Impact
Quantitative Benefit
Case Study missing?
Start adding your own!
Register with your work email and create a new case study profile for your business.
Related Case Studies.

Case Study
Remote Monitoring & Predictive Maintenance App for a Solar Energy System
The maintenance & tracking of various modules was an overhead for the customer due to the huge labor costs involved. Being an advanced solar solutions provider, they wanted to ensure early detection of issues and provide the best-in-class customer experience. Hence they wanted to automate the whole process.
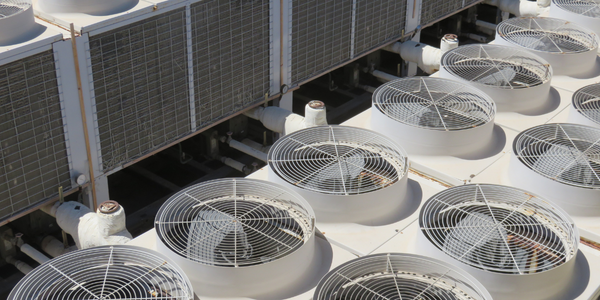
Case Study
Predictive Maintenance for Industrial Chillers
For global leaders in the industrial chiller manufacturing, reliability of the entire production process is of the utmost importance. Chillers are refrigeration systems that produce ice water to provide cooling for a process or industrial application. One of those leaders sought a way to respond to asset performance issues, even before they occur. The intelligence to guarantee maximum reliability of cooling devices is embedded (pre-alarming). A pre-alarming phase means that the cooling device still works, but symptoms may appear, telling manufacturers that a failure is likely to occur in the near future. Chillers who are not internet connected at that moment, provide little insight in this pre-alarming phase.
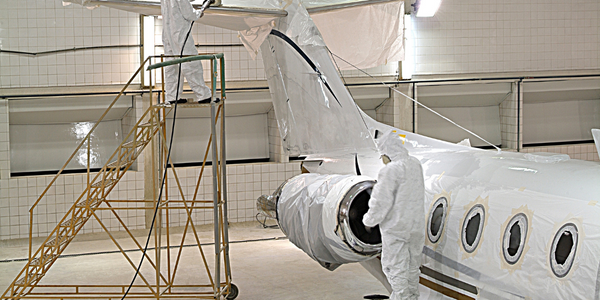
Case Study
Aircraft Predictive Maintenance and Workflow Optimization
First, aircraft manufacturer have trouble monitoring the health of aircraft systems with health prognostics and deliver predictive maintenance insights. Second, aircraft manufacturer wants a solution that can provide an in-context advisory and align job assignments to match technician experience and expertise.
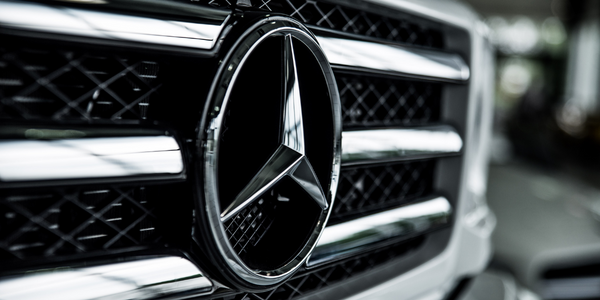
Case Study
Integral Plant Maintenance
Mercedes-Benz and his partner GAZ chose Siemens to be its maintenance partner at a new engine plant in Yaroslavl, Russia. The new plant offers a capacity to manufacture diesel engines for the Russian market, for locally produced Sprinter Classic. In addition to engines for the local market, the Yaroslavl plant will also produce spare parts. Mercedes-Benz Russia and his partner needed a service partner in order to ensure the operation of these lines in a maintenance partnership arrangement. The challenges included coordinating the entire maintenance management operation, in particular inspections, corrective and predictive maintenance activities, and the optimizing spare parts management. Siemens developed a customized maintenance solution that includes all electronic and mechanical maintenance activities (Integral Plant Maintenance).
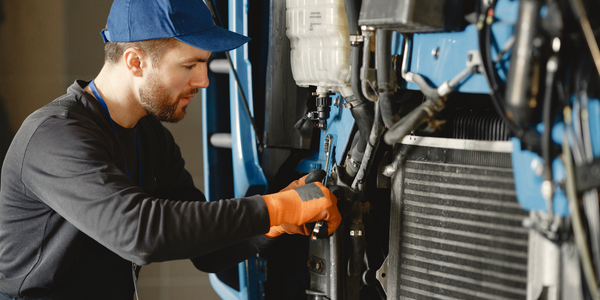
Case Study
Asset Management and Predictive Maintenance
The customer prides itself on excellent engineering and customer centric philosophy, allowing its customer’s minds to be at ease and not worry about machine failure. They can easily deliver the excellent maintenance services to their customers, but there are some processes that can be automated to deliver less downtime for the customer and more efficient maintenance schedules.