Technology Category
- Platform as a Service (PaaS) - Application Development Platforms
Applicable Industries
- Apparel
- Electronics
About The Customer
JioMart's customers are primarily Indian citizens who are looking for a simple and convenient way of online shopping. They are willing to make purchases on social platforms and expect personalized experiences similar to those they receive in stores. They are interested in a range of products across different categories such as consumer electronics, apparel, footwear, grocery, and general merchandise. The customers value convenience and are attracted to the ease of use offered by the JioMart's WhatsApp Bot. They are also responsive to notifications about new offers and promotions.
The Challenge
JioMart, an online shopping platform developed by Reliance Industries, aimed to provide a simple and convenient online shopping experience to millions of Indian citizens. The platform offered a range of products across various categories such as consumer electronics, apparel, footwear, grocery, and general merchandise. As the customer base expanded, the team at JioMart recognized the importance of prioritizing customer satisfaction and convenience. They identified the need for an omnichannel approach to make shopping easy for every Indian citizen. The primary challenge was to simplify online shopping and capture a previously untapped market. They also needed to meet the increasing expectations of customers who were willing to make purchases on social platforms and expected personalized experiences. In addition to new customer acquisition, JioMart also prioritized customer retention, repeat purchases, and loyalty. They also sought to diversify beyond just groceries and promote their offerings in other categories.
The Solution
To address these challenges, JioMart introduced the first-ever end-to-end shopping experience on WhatsApp. They developed a WhatsApp Bot, in collaboration with Haptik, that allowed users to complete their grocery shopping on WhatsApp. The chatbot made it easy for users to discover products and add them to their cart in just a few clicks. Users could seamlessly confirm delivery information and pay using any payment method. The JioMart team effectively used WhatsApp notifications to increase repeat usage and promote new offers. Together, Haptik and JioMart developed a strategy to encourage adoption and promote the WhatsApp phone number throughout the country. To reach a wider customer base, the JioMart bot was also made available in Hindi.
Operational Impact
Quantitative Benefit
Case Study missing?
Start adding your own!
Register with your work email and create a new case study profile for your business.
Related Case Studies.
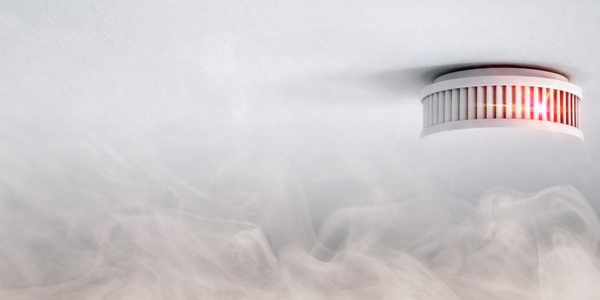
Case Study
Fire Alarm System and Remote Monitoring Sytem
Fire alarm systems are essential in providing an early warning in the event of fire. They help to save lives and protect property whilst also fulfilling the needs of insurance companies and government departments.Fire alarm systems typically consist of several inter-linked components, such as smoke detectors, heat detector, carbon monoxide, manual call points, sounders, alarm and buzzer. The fire alarm system should give immediate information in order to prevent the fire spread and protect live and property.To get maximum protection a shoe manufacturer in Indonesia opted for a new fire alarm system to monitor 13 production sites spread over 160 hectars. Although the company had an existing fire alarm system, it could not be monitored remotely.It was essential that the new system would be able to be monitored from a central control room. It needed to be able to connect to the existing smoke detector and manual call point. Information should be easily collected and passed on to the Supervisory Control and Data Acquisition (SCADA) system. Furthermore, the system should have several features such as alarm management, auto reporting, being connected to many client computers without additional cost, and run 24/7 without fails. The company also needed a system which could be implemented without changing the architecture of the existing fire alarm system.
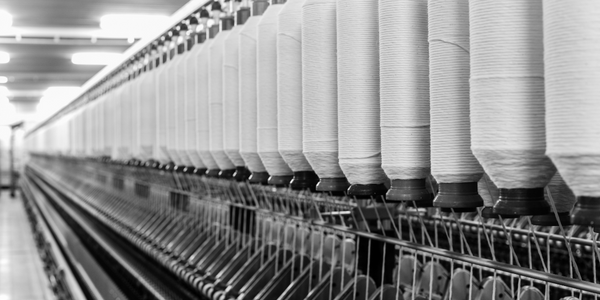
Case Study
IoT Applications and Upgrades in Textile Plant
At any given time, the textile company’s manufacturing facility has up to 2,000 textile carts in use. These carts are pushed from room to room, carrying materials or semi-finished products. Previously, a paper with a hand-written description was attached to each cart. This traditional method of processing made product tracking extremely difficult. Additionally, making sure that every cart of materials or semi-finished products went to its correct processing work station was also a problem. Therefore, the company desired an intelligent solution for tracking assets at their factories. They also wanted a solution that would help them collect process data so they could improve their manufacturing efficiency.
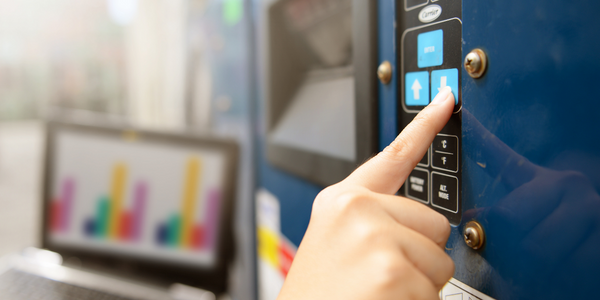
Case Study
Remote Temperature Monitoring of Perishable Goods Saves Money
RMONI was facing temperature monitoring challenges in a cold chain business. A cold chain must be established and maintained to ensure goods have been properly refrigerated during every step of the process, making temperature monitoring a critical business function. Manual registration practice can be very costly, labor intensive and prone to mistakes.
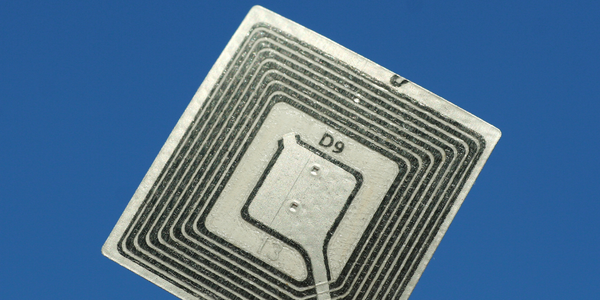
Case Study
Retailer Uses RFID Scanner to Improve Efficiency
Patrizia Pepe wished to improve the logistics of their warehouse: accepting incoming goods from their production sites, movement of items throughout
the warehouse, and packaging of goods for distribution to the retail locations. They initially tried to use barcodes for this function. Because barcodes must be individually scanned within a line-of-sight, the acceptance of goods coming into the warehouse was too time consuming. Working with the University of Florence, Patrizia Pepe instituted a five-month pilot project beginning in August of 2009 to test the validity of an RFID solution. The pilot involved tagging of about 60,000 items for the second seasonal collection, and convinced the company to move forward with tagging all items.