Customer Company Size
Mid-size Company
Region
- Europe
Country
- Germany
Product
- DocuWare for Invoice Processing
Tech Stack
- Microsoft Dynamics NAV 2018
- Microsoft Exchange Server
Implementation Scale
- Enterprise-wide Deployment
Impact Metrics
- Productivity Improvements
- Digital Expertise
Technology Category
- Functional Applications - Enterprise Resource Planning Systems (ERP)
Applicable Industries
- Retail
- Automotive
Applicable Functions
- Sales & Marketing
Use Cases
- Inventory Management
- Fraud Detection
Services
- System Integration
- Cloud Planning, Design & Implementation Services
About The Customer
Konrad GmbH operates eight motor vehicle specialist stores around greater Munich. The company offers a broad range of services to its customers, including spare part sales, equipping of repair shops, and renting of automotive equipment. They also have an online presence. The company has a staff of approximately 160. In a very innovative industry, automotive parts retailer Konrad has to be ready to face new trends and challenges every day. This applies not only to the range of spare parts and services offered to customers, but also to the organization and administration of the company.
The Challenge
Konrad GmbH, a motor vehicle specialist store operating in greater Munich, faced the challenge of meeting rigorous legal requirements for retention periods and unaltered commercial documents. The company, which operates in a highly innovative industry, needed to be ready to face new trends and challenges every day. This applied not only to the range of spare parts and services offered to customers, but also to the organization and administration of the company. The main purpose of investing in a Document Management System (DMS) was to ensure that the company could meet these legal requirements.
The Solution
To optimize business processes, Konrad has been using a cloud-based document management system since the beginning of 2019 in addition to an Automotive-IT industry solution implemented on the basis of Microsoft Dynamics NAV 2018. DocuWare is directly connected to the auto parts dealer’s ERP system via an integrated interface. All commercial documents created there are transferred, automatically indexed, and stored in a tamper-free manner. Account assignment and invoice information is transferred to the accounting department for further processing. All authorized employees can now access the documents in the central document pool from their familiar working environment. A preconfigured workflow was also implemented for fast and reliable verification of all incoming invoices.
Operational Impact
Quantitative Benefit
Case Study missing?
Start adding your own!
Register with your work email and create a new case study profile for your business.
Related Case Studies.
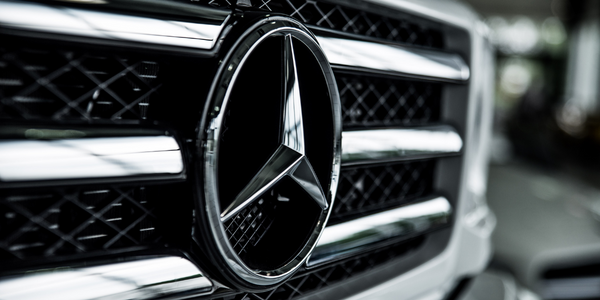
Case Study
Integral Plant Maintenance
Mercedes-Benz and his partner GAZ chose Siemens to be its maintenance partner at a new engine plant in Yaroslavl, Russia. The new plant offers a capacity to manufacture diesel engines for the Russian market, for locally produced Sprinter Classic. In addition to engines for the local market, the Yaroslavl plant will also produce spare parts. Mercedes-Benz Russia and his partner needed a service partner in order to ensure the operation of these lines in a maintenance partnership arrangement. The challenges included coordinating the entire maintenance management operation, in particular inspections, corrective and predictive maintenance activities, and the optimizing spare parts management. Siemens developed a customized maintenance solution that includes all electronic and mechanical maintenance activities (Integral Plant Maintenance).
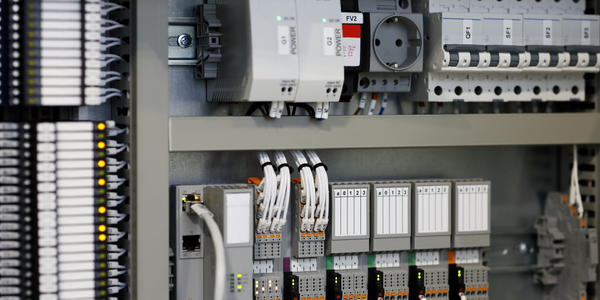
Case Study
Improving Production Line Efficiency with Ethernet Micro RTU Controller
Moxa was asked to provide a connectivity solution for one of the world's leading cosmetics companies. This multinational corporation, with retail presence in 130 countries, 23 global braches, and over 66,000 employees, sought to improve the efficiency of their production process by migrating from manual monitoring to an automatic productivity monitoring system. The production line was being monitored by ABB Real-TPI, a factory information system that offers data collection and analysis to improve plant efficiency. Due to software limitations, the customer needed an OPC server and a corresponding I/O solution to collect data from additional sensor devices for the Real-TPI system. The goal is to enable the factory information system to more thoroughly collect data from every corner of the production line. This will improve its ability to measure Overall Equipment Effectiveness (OEE) and translate into increased production efficiencies. System Requirements • Instant status updates while still consuming minimal bandwidth to relieve strain on limited factory networks • Interoperable with ABB Real-TPI • Small form factor appropriate for deployment where space is scarce • Remote software management and configuration to simplify operations