Technology Category
- Infrastructure as a Service (IaaS) - Cloud Computing
- Networks & Connectivity - RF Transceivers
Applicable Industries
- Aerospace
- Metals
Applicable Functions
- Procurement
- Product Research & Development
Use Cases
- Virtual Prototyping & Product Testing
- Virtual Reality
Services
- Hardware Design & Engineering Services
- System Integration
About The Customer
Optisys is a Utah-based startup specializing in the design, printing, and testing of metal 3D-printed antennas and RF components. The company focuses on RF and antenna components, integrating several parts into a single 3D print to improve size, weight, performance, and cost of the system. Optisys uses a unique fabrication process that allows it to generate designs and geometries that were not possible just a few years ago. The company's products are designed to withstand extreme environmental and mechanical conditions. Optisys competes with established RF suppliers, leveraging its agility and innovative approach to disrupt the market.
The Challenge
Optisys, a small radiofrequency (RF) antenna design company based in Utah, faced several challenges in its operations. The company specializes in 3D printing custom RF antenna solutions for military and commercial applications, a field that requires intensive simulations. However, the company's IT infrastructure was not up to the task. Optisys' team members were spread across different regions of the US, making it difficult to collaborate effectively. The company was also limited by the need to set up electromagnetics licenses and mechanical package licenses on local workstations, which meant only one person could use them at a time. Furthermore, the company did not want to invest in setting up a local intranet and server to check out licenses, as this was outside of their core competency. Another challenge was the need to purchase new high-performance computers for simulations every two to three years, a costly and inefficient process.
The Solution
Optisys found a solution to its challenges in Rescale, a cloud computing platform. Rescale allowed Optisys to run simulations on-demand from anywhere, eliminating the need for a local intranet and server. The platform also eliminated the need for Optisys to purchase and maintain high-performance computers, as Rescale provided the necessary hardware resources. Optisys could scale its hardware solution depending on the work it was performing on any given week. Rescale also supported ITAR simulations, a critical requirement for Optisys' industry. The company primarily used Rescale for ANSYS HFSS and ANSYS Mechanical simulations. The platform allowed Optisys to set up models locally, verify their functionality, set up an optimization, and then send it to Rescale to run the optimization. This freed up local machines for other tasks, boosting productivity. Rescale also enabled Optisys to tackle larger problem sizes and optimize them quickly.
Operational Impact
Quantitative Benefit
Case Study missing?
Start adding your own!
Register with your work email and create a new case study profile for your business.
Related Case Studies.
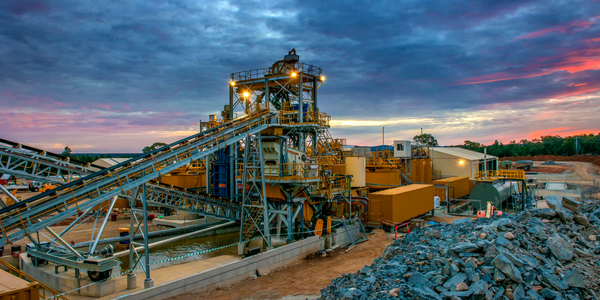
Case Study
Goldcorp: Internet of Things Enables the Mine of the Future
Goldcorp is committed to responsible mining practices and maintaining maximum safety for its workers. At the same time, the firm is constantly exploring ways to improve the efficiency of its operations, extend the life of its assets, and control costs. Goldcorp needed technology that can maximize production efficiency by tracking all mining operations, keep employees safe with remote operations and monitoring of hazardous work areas and control production costs through better asset and site management.
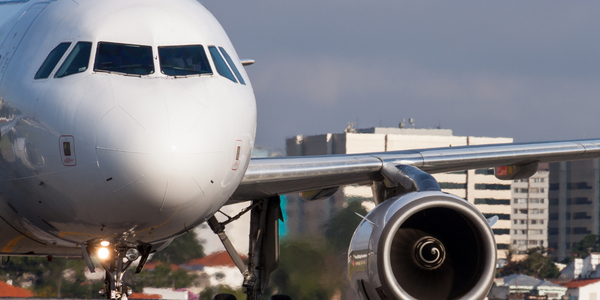
Case Study
Airbus Soars with Wearable Technology
Building an Airbus aircraft involves complex manufacturing processes consisting of thousands of moving parts. Speed and accuracy are critical to business and competitive advantage. Improvements in both would have high impact on Airbus’ bottom line. Airbus wanted to help operators reduce the complexity of assembling cabin seats and decrease the time required to complete this task.
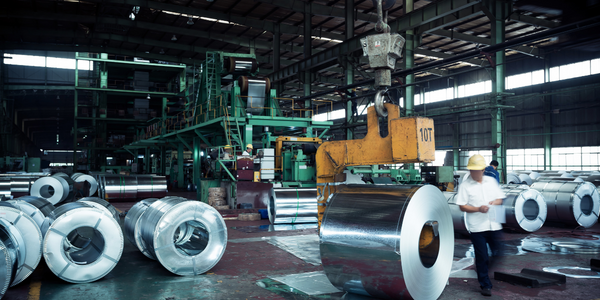
Case Study
KSP Steel Decentralized Control Room
While on-site in Pavlodar, Kazakhstan, the DAQRI team of Business Development and Solutions Architecture personnel worked closely with KSP Steel’s production leadership to understand the steel production process, operational challenges, and worker pain points.
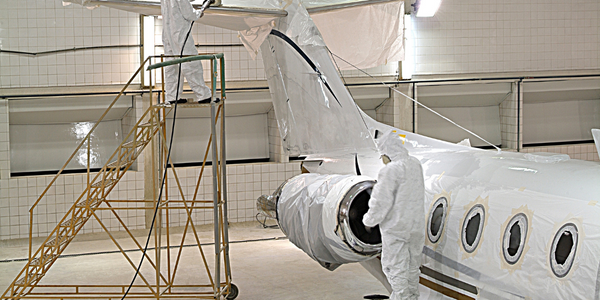
Case Study
Aircraft Predictive Maintenance and Workflow Optimization
First, aircraft manufacturer have trouble monitoring the health of aircraft systems with health prognostics and deliver predictive maintenance insights. Second, aircraft manufacturer wants a solution that can provide an in-context advisory and align job assignments to match technician experience and expertise.
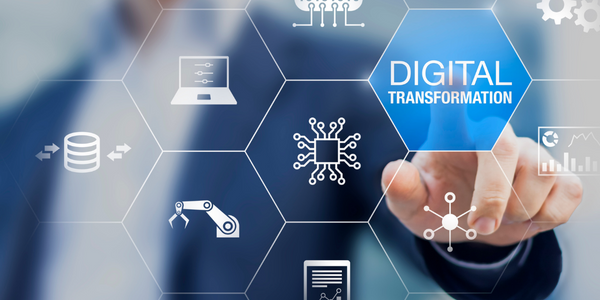
Case Study
Bluescope Steel on Path to Digitally Transform Operations and IT
Increasing competition and fluctuations in the construction market prompted BlueScope Steel to look toward digital transformation of its four businesses, including modern core applications and IT infrastructure. BlueScope needed to modernize its infrastructure and adopt new technologies to improve operations and supply chain efficiency while maintaining and updating an aging application portfolio.
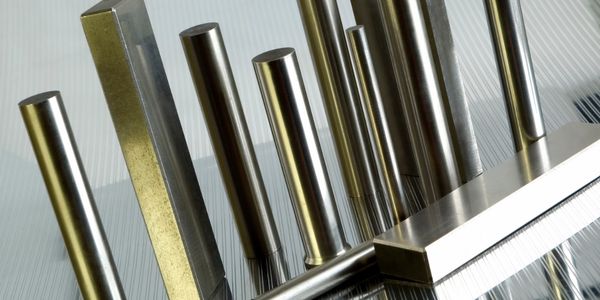
Case Study
RobotStudio Case Study: Benteler Automobiltechnik
Benteler has a small pipe business area for which they produce fuel lines and coolant lines made of aluminum for Porsche and other car manufacturers. One of the problems in production was that when Benteler added new products, production had too much downtime.