Customer Company Size
Mid-size Company
Region
- America
Country
- United States
Product
- Brocade ICX 6430 Switches
- Brocade ICX 6450 Switches
- Brocade ICX 6610 Switches
- Brocade VDX 6720 Switches
Tech Stack
- Brocade VCS fabric technology
- Citrix Virtual Desktop Infrastructure
Implementation Scale
- Enterprise-wide Deployment
Impact Metrics
- Productivity Improvements
- Revenue Growth
Technology Category
- Networks & Connectivity - Ethernet
Applicable Functions
- Discrete Manufacturing
- Quality Assurance
Use Cases
- Manufacturing System Automation
- Predictive Maintenance
Services
- System Integration
About The Customer
Miller Welding & Machine Company is a family-owned business founded in 1963 by David R. Miller. The company started by repairing parts for local farmers and has since grown to provide metal fabrication, welding, machining, finishing, and mechanical assembly services for leading manufacturers. The company has grown because of its commitment to world-class service and by implementing technology solutions to empower its employees and processes, growing sales tenfold from 2003 to 2007. Miller Welding’s specialty is high-mix, low volume products. This means ensuring exceptional quality for small runs of many types of parts and consistently meeting high customer expectations for correct deliveries within narrow delivery windows. The network is critical to delivering the data needed to achieve these goals.
The Challenge
Miller Welding & Machine Company, a family-owned business providing metal fabrication, welding, machining, finishing, and mechanical assembly services for leading manufacturers, aimed to become a world-class supplier by using innovation to continually enhance operations and support growth. The company specializes in high-mix, low volume products, ensuring exceptional quality for small runs of many types of parts and consistently meeting high customer expectations for correct deliveries within narrow delivery windows. As the company grew, it needed to upgrade its network to an enterprise-class infrastructure to support next-generation manufacturing automation applications and services. High performance was the primary criteria, with high availability a close second. The network had to be able to withstand machine shock conditions and operate 24 hours a day at 99.999 percent availability. Miller Welding wanted integrated switching, wired, and wireless connectivity so that data was available everywhere—from warehouses and loading docks to representatives across the United States.
The Solution
Miller Welding turned to Advanticom, Inc., its trusted IT partner for the past 10 years, to upgrade its network. After evaluating four leading network brands for Miller Welding’s new network, Advanticom recommended Brocade. The new network interconnects three manufacturing and office locations. Two of these sites also host data centers. Stacked Brocade® ICX® 6610 Switches serve as a combined aggregation and core layer for the main site, delivering data traffic to the Internet, voice traffic across the MPLS core network, and other data traffic over a direct connection to the secondary site. All Brocade ICX Switches are configured to deliver Quality of Service (QoS) for the phone system. Brocade ICX 6430 Switches deliver PoE power to wireless access points, aggregate wireless traffic at the network edges, and forward it to Brocade ICX 6610 Switches at the aggregation layer. Brocade ICX 6450 Switches forward traffic to the Brocade ICX 6610 Switches in the main data center and operate as aggregation switches in the other two locations for wired, wireless, and Virtual Desktop Infrastructure (VDI) traffic transport.
Operational Impact
Quantitative Benefit
Case Study missing?
Start adding your own!
Register with your work email and create a new case study profile for your business.
Related Case Studies.

Case Study
Remote Monitoring & Predictive Maintenance App for a Solar Energy System
The maintenance & tracking of various modules was an overhead for the customer due to the huge labor costs involved. Being an advanced solar solutions provider, they wanted to ensure early detection of issues and provide the best-in-class customer experience. Hence they wanted to automate the whole process.
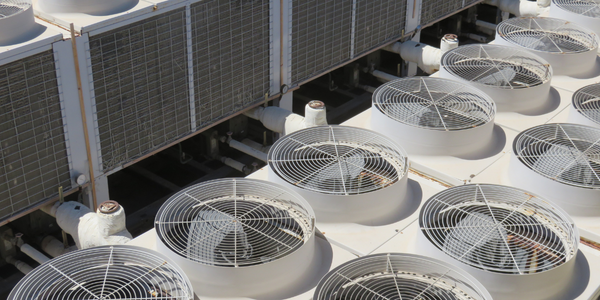
Case Study
Predictive Maintenance for Industrial Chillers
For global leaders in the industrial chiller manufacturing, reliability of the entire production process is of the utmost importance. Chillers are refrigeration systems that produce ice water to provide cooling for a process or industrial application. One of those leaders sought a way to respond to asset performance issues, even before they occur. The intelligence to guarantee maximum reliability of cooling devices is embedded (pre-alarming). A pre-alarming phase means that the cooling device still works, but symptoms may appear, telling manufacturers that a failure is likely to occur in the near future. Chillers who are not internet connected at that moment, provide little insight in this pre-alarming phase.
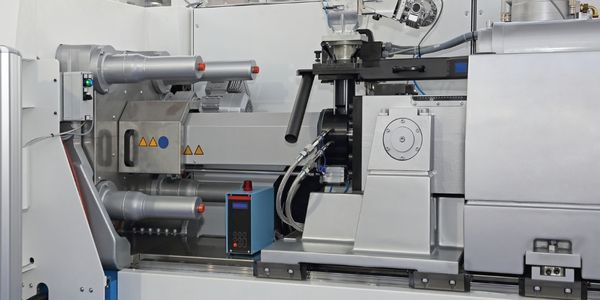
Case Study
Plastic Spoons Case study: Injection Moulding
In order to meet customer expectations by supplying a wide variety of packaging units, from 36 to 1000 spoons per package, a new production and packaging line needed to be built. DeSter wanted to achieve higher production capacity, lower cycle time and a high degree of operator friendliness with this new production line.
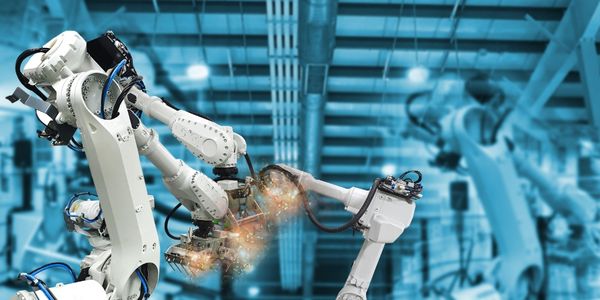
Case Study
Robot Saves Money and Time for US Custom Molding Company
Injection Technology (Itech) is a custom molder for a variety of clients that require precision plastic parts for such products as electric meter covers, dental appliance cases and spools. With 95 employees operating 23 molding machines in a 30,000 square foot plant, Itech wanted to reduce man hours and increase efficiency.
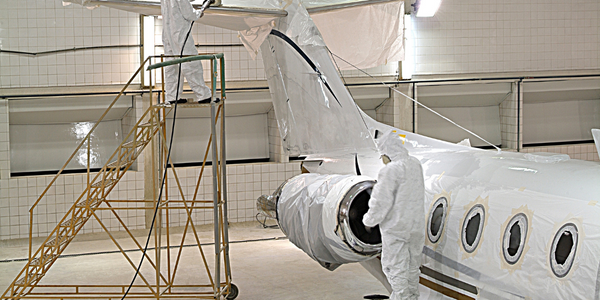
Case Study
Aircraft Predictive Maintenance and Workflow Optimization
First, aircraft manufacturer have trouble monitoring the health of aircraft systems with health prognostics and deliver predictive maintenance insights. Second, aircraft manufacturer wants a solution that can provide an in-context advisory and align job assignments to match technician experience and expertise.
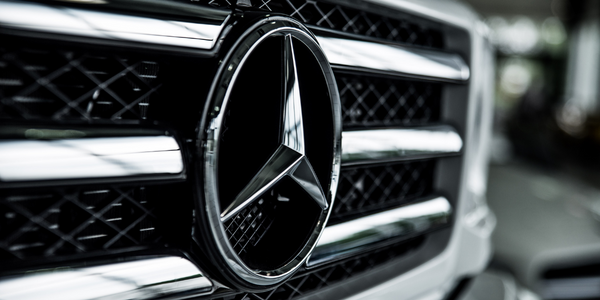
Case Study
Integral Plant Maintenance
Mercedes-Benz and his partner GAZ chose Siemens to be its maintenance partner at a new engine plant in Yaroslavl, Russia. The new plant offers a capacity to manufacture diesel engines for the Russian market, for locally produced Sprinter Classic. In addition to engines for the local market, the Yaroslavl plant will also produce spare parts. Mercedes-Benz Russia and his partner needed a service partner in order to ensure the operation of these lines in a maintenance partnership arrangement. The challenges included coordinating the entire maintenance management operation, in particular inspections, corrective and predictive maintenance activities, and the optimizing spare parts management. Siemens developed a customized maintenance solution that includes all electronic and mechanical maintenance activities (Integral Plant Maintenance).