Technology Category
- Robots - Wheeled Robots
- Sensors - GPS
Applicable Industries
- Recycling & Waste Management
- Telecommunications
Applicable Functions
- Maintenance
- Product Research & Development
Use Cases
- Predictive Waste Reduction
- Time Sensitive Networking
About The Customer
Numac Fabrications Ltd is a family-owned business that manufactures waste skips, roll-on roll-off containers, and waste compactors. They also provide on-site servicing of waste compactors and balers. The company services clients across Ireland, the UK, and the USA, offering bespoke design and production services to waste management, construction, and food processing companies. Their facility includes CAD design, specialist plasma cutting equipment, and painting units. They manufacture products to meet all Chem standards and their product range includes waste compactors, both static and portable units, as well as a wide range of containers and skips.
The Challenge
Numac Fabrications Ltd, a manufacturer of waste skips, roll-on roll-off containers, and waste compactors, was facing challenges in managing their day-to-day operations. The company, which also provides on-site servicing of waste compactors and balers, was struggling with the efficient allocation of jobs based on real-time factors such as driver, equipment, and stock availability. The traditional method of passing on orders verbally often resulted in mistakes, as important specifications were sometimes forgotten. Furthermore, the company was unable to effectively track their products and engineers, which was crucial for their growing business. The lack of a digital system for forms and data collection was also hindering business growth and employee productivity.
The Solution
Numac Fabrications Ltd adopted FIELDMOTION, a waste and recycling software, to streamline their operations. The software allowed the company to send orders directly to the workshop supervisor, eliminating the need for verbal communication and reducing the chances of errors. The software also provided the ability to add photos to job sheets and service sheets, enhancing customer understanding of the work carried out. FIELDMOTION's job scheduling feature enabled Numac Fabrications to allocate jobs based on real-time factors, improving efficiency. The mobile app provided live job progress updates to the back office team and customers, and also included a GPS stamp for locating jobs and employees. The company also switched to mobile forms and data collection software, which led to greater business growth, employee productivity, and improved bottom line.
Operational Impact
Quantitative Benefit
Case Study missing?
Start adding your own!
Register with your work email and create a new case study profile for your business.
Related Case Studies.
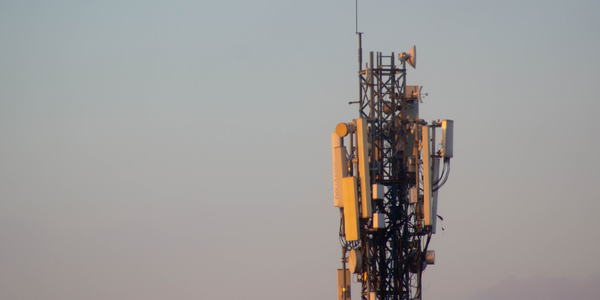
Case Study
Vodafone Hosted On AWS
Vodafone found that traffic for the applications peak during the four-month period when the international cricket season is at its height in Australia. During the 2011/2012 cricket season, 700,000 consumers downloaded the Cricket Live Australia application. Vodafone needed to be able to meet customer demand, but didn’t want to invest in additional resources that would be underutilized during cricket’s off-season.
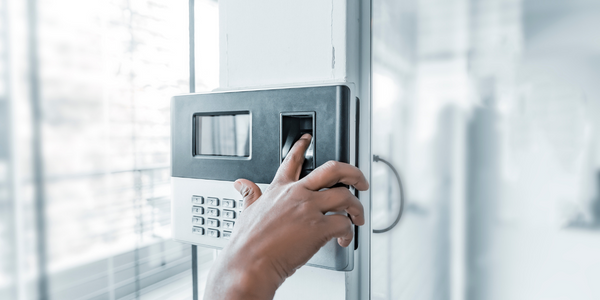
Case Study
SKT, Construction of Smart Office Environment
SK T-Tower is the headquarters of SK Telecom. Inside the building, different types of mobile devices, such as laptops, smartphones and tablets, are in use, and with the increase in WLAN traffic and the use of quality multimedia data, the volume of wireless data sees an explosive growth. Users want limitless Internet access in various places in addition to designated areas.
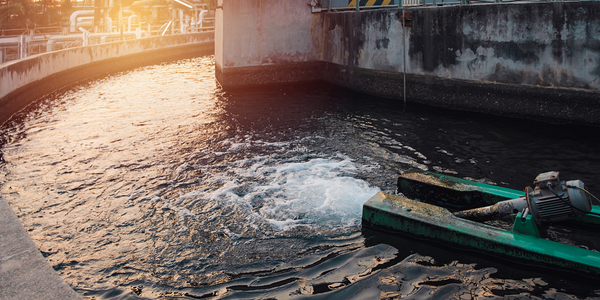
Case Study
Water Treatment Energy Management
Water pumping, treatment and conveyance are among the largest energy and cost outlays for many local and regional municipalities. Electricity time-of-use rates and peak pricing tariffs are driving those costs even higher. This case study describes how Monterey Regional Water Pollution Control Agency (MRWPCA) implemented a process data monitoring and control solution in order to analyze and optimize energy use, reduce deployment costs and save operational expenses.