Customer Company Size
SME
Region
- America
Country
- United States
Product
- Pacejet Shipping Software
Tech Stack
- NetSuite
Implementation Scale
- Enterprise-wide Deployment
Impact Metrics
- Cost Savings
- Productivity Improvements
Technology Category
- Functional Applications - Fleet Management Systems (FMS)
Applicable Industries
- Automotive
Applicable Functions
- Logistics & Transportation
Use Cases
- Fleet Management
Services
- System Integration
About The Customer
Established in 2006, TrakMotive specializes in 100% brand new Automotive Light Duty Truck CV Axles, ATV-UTV CV Axles, Drive Shaft Assemblies and Window Regulators. With two distribution centers, Springfield, MO, and Redlands, CA, TrakMotive serves customers in the United States the highest quality transfer of power from their transmission to their wheels. As they began to grow they were in search of a better shipping solution to help them with their manual entry errors and limited carrier options.
The Challenge
TrakMotive was using a few different workflows in order to process shipments and were unable to find an efficient way to ensure data was getting written back correctly. Team members were having to manually key in various repeated pieces of information into multiple systems leaving their business vulnerable to errors. With multiple systems and tabs open to process a shipment, their management team required they limit the number of carrier offerings so that they could try to reduce manual errors and time spent at the shipping workstation.
The Solution
Pacejet’s built-in rate shopping capabilities helped enable their staff to grow the number of carrier options to reduce spend and provide variety. Simply having more connected carrier options within their system, has greatly improved TrakMotive’s ability to grow and scale. Now, the TrakMotive team is able to quickly view real-time rates and carrier options directly within their NetSuite portal without having to open multiple windows and tabs in order to compare shipments. Manual keystroke errors were one of the biggest challenges that TrakMotive was facing. With Pacejet in place, they are now able to process shipments with scanning and a few single entry keystrokes and the information flows seamlessly into all of their database and supply chain systems.
Operational Impact
Quantitative Benefit
Case Study missing?
Start adding your own!
Register with your work email and create a new case study profile for your business.
Related Case Studies.
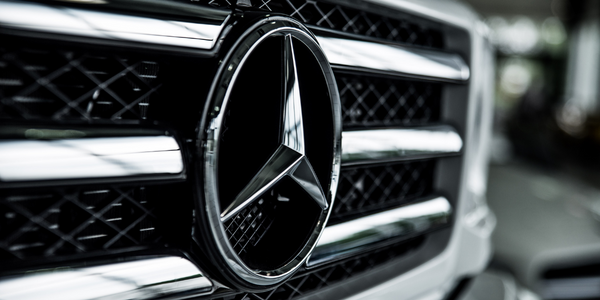
Case Study
Integral Plant Maintenance
Mercedes-Benz and his partner GAZ chose Siemens to be its maintenance partner at a new engine plant in Yaroslavl, Russia. The new plant offers a capacity to manufacture diesel engines for the Russian market, for locally produced Sprinter Classic. In addition to engines for the local market, the Yaroslavl plant will also produce spare parts. Mercedes-Benz Russia and his partner needed a service partner in order to ensure the operation of these lines in a maintenance partnership arrangement. The challenges included coordinating the entire maintenance management operation, in particular inspections, corrective and predictive maintenance activities, and the optimizing spare parts management. Siemens developed a customized maintenance solution that includes all electronic and mechanical maintenance activities (Integral Plant Maintenance).
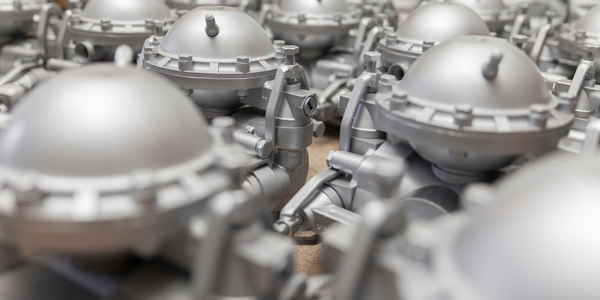
Case Study
Monitoring of Pressure Pumps in Automotive Industry
A large German/American producer of auto parts uses high-pressure pumps to deburr machined parts as a part of its production and quality check process. They decided to monitor these pumps to make sure they work properly and that they can see any indications leading to a potential failure before it affects their process.