Customer Company Size
Large Corporate
Region
- Asia
Country
- Malaysia
Product
- nGeniusONE® Service Assurance platform
- InfiniStreamNG™ appliances
- nGenius® packet flow switch appliances
Tech Stack
- Adaptive Service Intelligence™ (ASI) technology
Implementation Scale
- Enterprise-wide Deployment
Impact Metrics
- Customer Satisfaction
- Productivity Improvements
Technology Category
- Application Infrastructure & Middleware - API Integration & Management
Applicable Industries
- Oil & Gas
- Retail
Applicable Functions
- Sales & Marketing
- Business Operation
Use Cases
- Real-Time Location System (RTLS)
Services
- System Integration
- Testing & Certification
About The Customer
Petroliam Nasional Berhad (PETRONAS) is Malaysia’s fully integrated oil and gas multinational and is ranked among the largest corporations in the Fortune Global 500. Their partly owned PETRONAS Dagangan Berhad business subsidiary is involved in the distribution and sale of finished petroleum products and operations of service stations for the Malaysian market. PETRONAS provides onshore and offshore gas and petroleum exploration primarily in Malaysia. It has grown to be Malaysia’s largest petroleum retail network, marketing products to consumers in more than 1,000 PETRONAS stations and 725 Kedai Mesra convenience stores. In addition to petroleum products, their one-stop convenience centres offer dining, shopping, banking, car spa, and other services.
The Challenge
PETRONAS Dagangan Berhad, a subsidiary of Petroliam Nasional Berhad (PETRONAS), is a leading oil and gas multinational in Malaysia. The company operates over 1,000 petrol stations and 725 convenience stores, offering a range of services from fuel to dining and banking. To maintain its market leadership, PETRONAS recognized the need for a proactive solution to detect and troubleshoot issues with its point-of-sale (POS), Customer Relationship Management (CRM), and logistics applications before they impacted customers. Prior to implementing a proactive monitoring solution, PETRONAS was unable to detect and correct IT service degradations, which could negatively impact customer experience. With over 1,000 remote locations and multiple applications interfacing with central data centers over the telco network, pinpointing disruptions became a significant challenge. PETRONAS needed a solution that could provide visibility across the entire environment to reduce mean-time-to-resolution (MTTR) when problems were detected.
The Solution
PETRONAS chose NETSCOUT’s nGeniusONE Service Assurance platform for its ability to leverage smart data generated by its patented Adaptive Service Intelligence™ (ASI) technology. This technology quickly identifies and pinpoints the root cause of service problems. The solution is deployed in the central data centers, monitoring all packets into and out of the data centers, including POS, CRM, logistics, and other application traffic. Alarms are triggered to provide early warning when services first start to degrade. The IT staff uses the Service Dashboard for details, including latency, errors, success/failure, etc. for the affected location. With contextual drill-downs from the dashboard to views of session details and/or specialized service monitors with key performance indicators, the team can quickly determine the root cause of problems, allowing them to be addressed before negatively impacting customers. PETRONAS also deployed nGenius packet flow switch appliances at each data center to optimize traffic, delivering it to required backend systems as well as to the InfiniStreamNG (ISNG) appliance, where bi-directional traffic is analyzed with ASI, creating smart data utilized by the nGeniusONE platform.
Operational Impact
Quantitative Benefit
Case Study missing?
Start adding your own!
Register with your work email and create a new case study profile for your business.
Related Case Studies.
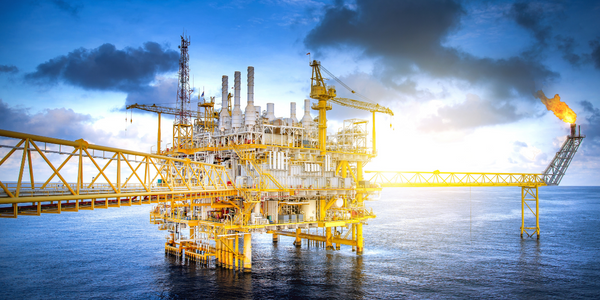
Case Study
Taking Oil and Gas Exploration to the Next Level
DownUnder GeoSolutions (DUG) wanted to increase computing performance by 5 to 10 times to improve seismic processing. The solution must build on current architecture software investments without sacrificing existing software and scale computing without scaling IT infrastructure costs.
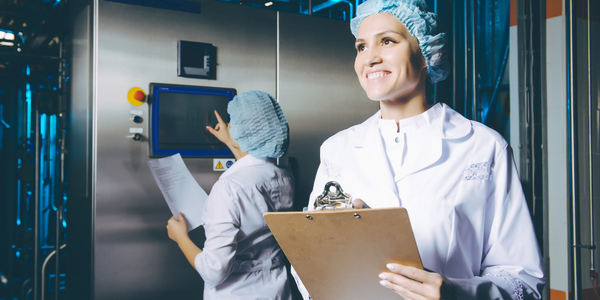
Case Study
Remote Wellhead Monitoring
Each wellhead was equipped with various sensors and meters that needed to be monitored and controlled from a central HMI, often miles away from the assets in the field. Redundant solar and wind generators were installed at each wellhead to support the electrical needs of the pumpstations, temperature meters, cameras, and cellular modules. In addition to asset management and remote control capabilities, data logging for remote surveillance and alarm notifications was a key demand from the customer. Terra Ferma’s solution needed to be power efficient, reliable, and capable of supporting high-bandwidth data-feeds. They needed a multi-link cellular connection to a central server that sustained reliable and redundant monitoring and control of flow meters, temperature sensors, power supply, and event-logging; including video and image files. This open-standard network needed to interface with the existing SCADA and proprietary network management software.
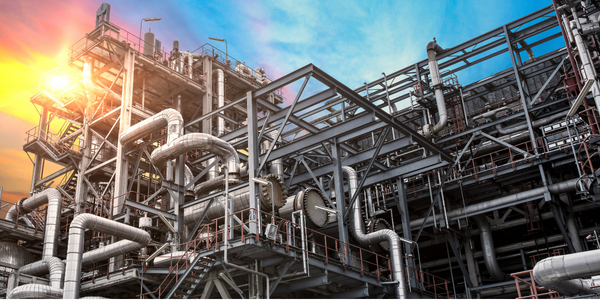
Case Study
Refinery Saves Over $700,000 with Smart Wireless
One of the largest petroleum refineries in the world is equipped to refine various types of crude oil and manufacture various grades of fuel from motor gasoline to Aviation Turbine Fuel. Due to wear and tear, eight hydrogen valves in each refinery were leaking, and each cost $1800 per ton of hydrogen vented. The plant also had leakage on nearly 30 flare control hydrocarbon valves. The refinery wanted a continuous, online monitoring system that could catch leaks early, minimize hydrogen and hydrocarbon production losses, and improve safety for maintenance.