Region
- America
Country
- United States
Product
- E2 Shop System
Implementation Scale
- Enterprise-wide Deployment
Impact Metrics
- Productivity Improvements
- Digital Expertise
Technology Category
- Functional Applications - Enterprise Resource Planning Systems (ERP)
Applicable Industries
- Automotive
- Healthcare & Hospitals
Applicable Functions
- Quality Assurance
Services
- System Integration
- Training
About The Customer
PF Technologies is a leader in robotic coatings and decorating for the medical and automotive industries. Unlike traditional job shops that focus on parts creation or tool making, PF Technologies' focus is on producing quality products while adhering to strict federal and agency regulations. The company's processes are unique and more restricted due to these regulations. The General Manager of PF Technologies, Bill Rice, has been with the company since 1993 and was instrumental in designing and managing the company's first access system.
The Challenge
PF Technologies, a company specializing in robotic coatings and decorating for the medical and automotive industries, was facing challenges with their outdated management software. The software, which was designed and managed by the company's General Manager, Bill Rice, in 1993, was no longer able to keep up with the growing sophistication of the business. The system began to crash daily, and the original programmer was no longer available to make necessary updates. The company's unique processes, which are heavily regulated by federal and agency regulations, required a robust and sophisticated system that could handle their unique needs.
The Solution
PF Technologies chose the E2 Shop System as their new management software. The E2 system was chosen for its balance of user-friendliness and sophistication, capable of handling the unique aspects of PF Technologies' business. To transition to the new system, the company ran E2 parallel with their old system for two months. This allowed them to learn how to enter parts and familiarize themselves with the software without disrupting their daily operations. After two months, they were able to shut down the old system and run completely on E2. The E2 system is logically designed, with everything tied together and easily accessible. It allows PF Technologies to customize forms based on the industries and clients they serve, and it is robust enough to handle the regulations and quality controls required by their clients' industries.
Operational Impact
Case Study missing?
Start adding your own!
Register with your work email and create a new case study profile for your business.
Related Case Studies.
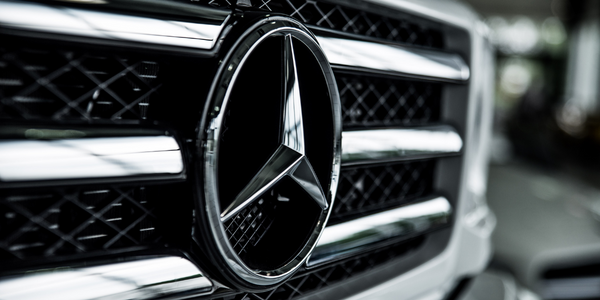
Case Study
Integral Plant Maintenance
Mercedes-Benz and his partner GAZ chose Siemens to be its maintenance partner at a new engine plant in Yaroslavl, Russia. The new plant offers a capacity to manufacture diesel engines for the Russian market, for locally produced Sprinter Classic. In addition to engines for the local market, the Yaroslavl plant will also produce spare parts. Mercedes-Benz Russia and his partner needed a service partner in order to ensure the operation of these lines in a maintenance partnership arrangement. The challenges included coordinating the entire maintenance management operation, in particular inspections, corrective and predictive maintenance activities, and the optimizing spare parts management. Siemens developed a customized maintenance solution that includes all electronic and mechanical maintenance activities (Integral Plant Maintenance).
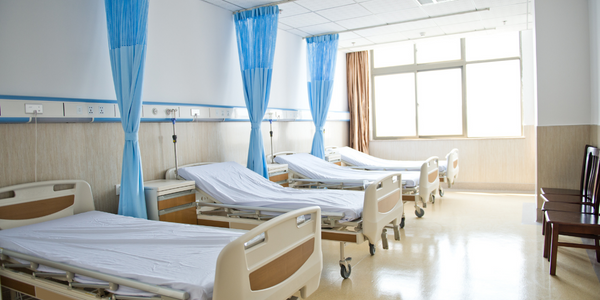
Case Study
Hospital Inventory Management
The hospital supply chain team is responsible for ensuring that the right medical supplies are readily available to clinicians when and where needed, and to do so in the most efficient manner possible. However, many of the systems and processes in use at the cancer center for supply chain management were not best suited to support these goals. Barcoding technology, a commonly used method for inventory management of medical supplies, is labor intensive, time consuming, does not provide real-time visibility into inventory levels and can be prone to error. Consequently, the lack of accurate and real-time visibility into inventory levels across multiple supply rooms in multiple hospital facilities creates additional inefficiency in the system causing over-ordering, hoarding, and wasted supplies. Other sources of waste and cost were also identified as candidates for improvement. Existing systems and processes did not provide adequate security for high-cost inventory within the hospital, which was another driver of cost. A lack of visibility into expiration dates for supplies resulted in supplies being wasted due to past expiry dates. Storage of supplies was also a key consideration given the location of the cancer center’s facilities in a dense urban setting, where space is always at a premium. In order to address the challenges outlined above, the hospital sought a solution that would provide real-time inventory information with high levels of accuracy, reduce the level of manual effort required and enable data driven decision making to ensure that the right supplies were readily available to clinicians in the right location at the right time.