Technology Category
- Functional Applications - Computerized Maintenance Management Systems (CMMS)
Applicable Functions
- Maintenance
- Quality Assurance
Use Cases
- Time Sensitive Networking
- Visual Quality Detection
Services
- Testing & Certification
About The Customer
The customer in this case study is a large manufacturing company known for its high-quality standards. The company has a unique maintenance program where certain procedures are only required every 5 to 10 years. The company has a long-standing tradition of relying on tribal knowledge, with long-term employees passing down the knowledge of these maintenance procedures. The company boasts a workforce with a high retention rate, with many employees staying with the company for over 30 years. However, the company is facing a potential challenge with the changing dynamics of the workforce, with millennials, who tend to have a shorter tenure, becoming the dominant workforce.
The Challenge
The case study revolves around a large manufacturing company that relies heavily on tribal knowledge for its maintenance procedures. The company has a unique situation where certain maintenance procedures are only required every 5 to 10 years. This knowledge is passed down from long-term employees who have been with the company for decades. However, the company is facing a potential challenge with the changing dynamics of the workforce. The current trend shows that millennials, who are now the dominant workforce, tend to stay with a company for only 2-3 years, significantly less than the 5-10 year maintenance cycle. The average tenure of workers is 4.6 years, and even lower for millennials at 3.2 years. This poses a significant risk to the company's maintenance procedures as the knowledge may not be passed down effectively due to the shorter tenure of employees.
The Solution
The solution to this challenge is to shift away from relying solely on tribal knowledge and start recording and redistributing this knowledge. This would involve creating a system or process where the knowledge of these maintenance procedures is documented and easily accessible for future reference. This could be in the form of a digital database or a manual, depending on the company's preference and resources. The company would need to ensure that this knowledge is updated regularly and that new employees are trained on how to access and use this information. This would not only preserve the knowledge but also ensure that it is passed down effectively, regardless of the tenure of the employees. This shift would require a significant effort but is a necessary endeavor to ensure the continuity of the company's high-quality standards.
Operational Impact
Case Study missing?
Start adding your own!
Register with your work email and create a new case study profile for your business.
Related Case Studies.
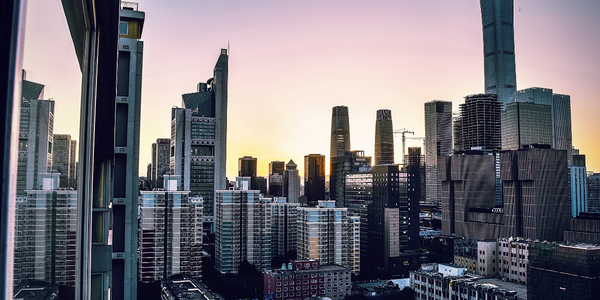
Case Study
Rapid and Simple Installation Provides Access to Critical Data
The customer needed to monitor non-contact alignment and non-contact process temperature in different positions along a 100-meter production line. Space around the line is tight and operators and forklift trucks are passing by constantly. Installation of correctly routed cables from sensors back to the control station would have been expensive and would have taken too long and caused too much disruption to ongoing operations.
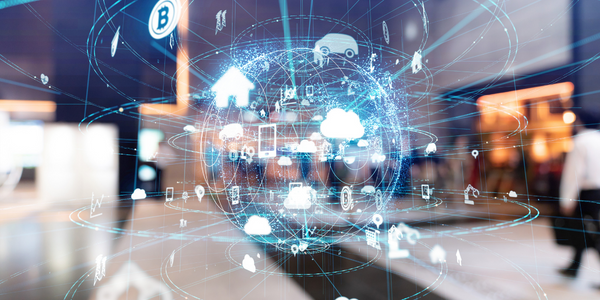
Case Study
Real-Time IoT Tracking and Visualization Improve Manufacturing
Shimane Fujitsu, a wholly-owned subsidiary of Fujitsu and a leading manufacturer of business notebooks and tablets, set out to improve processes where factory inspections found product errors. Prioritizing product rework based on shipping date was challenging, and it caused Shimane Fujitsu to incur additional shipping fees. The company needed a way to collect data to better track the location of products in the rework cycle as well as monitor progress in real time. The collected data would also help process analysis for future improvements.
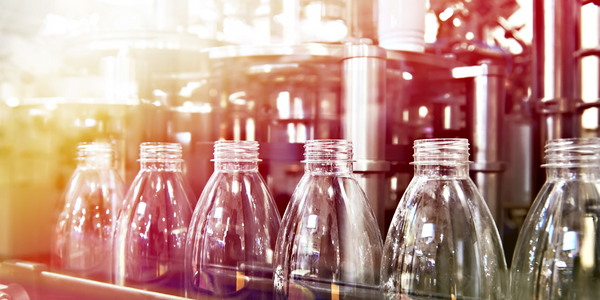
Case Study
Automatic Vision Inspection Solution for Product Traceability
With greater market demand for food safety, traceability is receiving increasingly more attention in the food and beverage industry as well as the packaging industry. One of the world's leading providers of beverage containers required a system to identify bar codes and alphanumeric characters on ink-jet-printed labels at a run rate of 7 units and minimum 99.9% accuracy. Since there were few engineers in the factory, the customer sought to implement a reliable system with an easy-to-use GUI for workers with a less technical background.
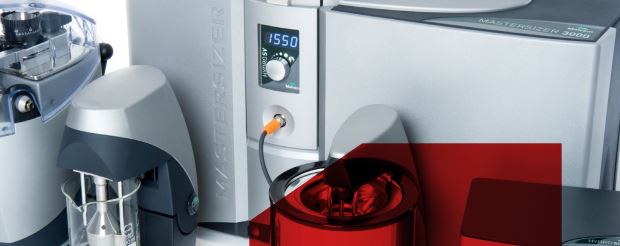
Case Study
Centralizing Data for Improved Efficiency: A Case Study on Malvern Panalytical
Malvern Panalytical, a UK-based hi-tech electronics company, was grappling with the challenge of decentralized data storage. The company had a vast amount of unstructured data scattered across various platforms, from hard drives to emails and floppy disks. This made the data searching process extremely cumbersome and inefficient. The company's rapid growth, from 200 to over 1,000 employees in a decade, and expansion across three continents further exacerbated the need for a more structured and centralized data system. As a company involved in electronics manufacturing and software development, it was crucial for Malvern Panalytical to find a platform that could structure all their data, track all modifications of documents in real time, and provide clear visibility of the internal information flow across all its facilities.
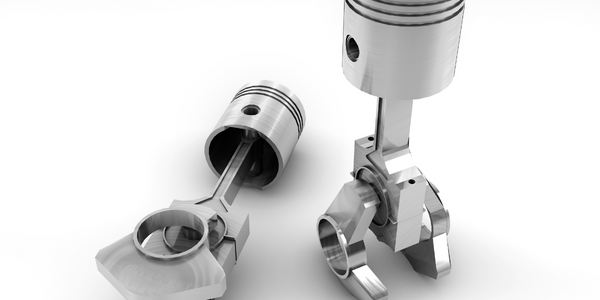
Case Study
Automated Inspection of Axial Piston Motors
Earth moving machines require an immense energy source to provide the power they need for use within civil engineering works. ‘Hydraulic Motors’ allow this power to be applied to enable the machines movement and in addition ‘Control Valves’ also provide the operator with the precise feel and control required to undertake the necessary tasks needed for such machines, including trenching, rock breaking and demolition. These same motors are also used in cranes, wheel loaders and general construction equipment. Though not a new product, the designs of such motors and control valves have been around a few decades, the overall method for manufacture has changed rapidly over the last few years to take account of the need for more modular designs, manufacture and just-in-time manufacturing. Kawasaki Precision Machinery (UK) Ltd based in Plymouth, UK is one of the leading manufacturers of such motors and pumps. They approached Industrial Vision Systems Ltd to come up with a solution to provide automated inspection of such pumps for their semi-automated assembly process. The pumps requiring inspection are at a sub-assembly stage when they are due for the inspection process to take place. Due to the highly modular nature of the construction each part of the pump can have many different derivatives which overall have a different effect on the pump in industrial use. It is therefore critical for the manufacturing process to check all components are the correct type and number for the construction of the pump to begin. Once built it is difficult and costly to rework such units if a fault is detected later in the manufacturing process, therefore automated visual inspection is critical for the success in building quality motors and pumps.