技术
- 功能应用 - 计算机化维护管理系统 (CMMS)
适用功能
- 维护
- 质量保证
用例
- 时间敏感网络
- 视觉质量检测
服务
- 测试与认证
关于客户
本案例研究中的客户是一家以其高质量标准而闻名的大型制造公司。该公司拥有独特的维护计划,其中某些程序仅每 5 至 10 年需要执行一次。该公司有着依赖部落知识的悠久传统,长期员工将这些维护程序的知识传承下来。公司拥有一支高保留率的员工队伍,许多员工在公司工作超过30年。然而,该公司正面临着劳动力动态变化的潜在挑战,千禧一代的任期往往较短,成为劳动力的主导力量。
挑战
该案例研究围绕一家大型制造公司展开,该公司的维护程序严重依赖部落知识。该公司有一个独特的情况,即每 5 到 10 年才需要执行某些维护程序。这些知识是从在公司工作了数十年的长期员工那里传承下来的。然而,该公司正面临着劳动力动态变化的潜在挑战。目前的趋势表明,现在作为劳动力主体的千禧一代往往只在公司工作2-3年,大大低于5-10年的维护周期。工人的平均任期为 4.6 年,千禧一代的平均任期更低,为 3.2 年。这给公司的维护程序带来了重大风险,因为由于员工任期较短,知识可能无法有效传承。
解决方案
应对这一挑战的解决方案是不再仅仅依赖部落知识,而是开始记录和重新分发这些知识。这将涉及创建一个系统或流程,其中记录了这些维护程序的知识,并且可以轻松访问以供将来参考。这可以是数字数据库或手册的形式,具体取决于公司的偏好和资源。公司需要确保定期更新这些知识,并确保新员工接受如何访问和使用这些信息的培训。这不仅可以保存知识,而且可以确保知识有效地传承下去,无论员工的任期如何。这一转变需要付出巨大的努力,但也是确保公司高质量标准连续性的必要努力。
运营影响
Case Study missing?
Start adding your own!
Register with your work email and create a new case study profile for your business.
相关案例.
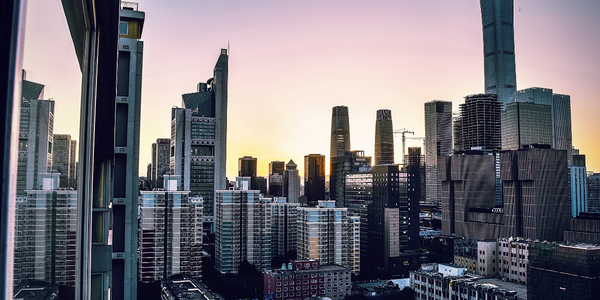
Case Study
Rapid and Simple Installation Provides Access to Critical Data
The customer needed to monitor non-contact alignment and non-contact process temperature in different positions along a 100-meter production line. Space around the line is tight and operators and forklift trucks are passing by constantly. Installation of correctly routed cables from sensors back to the control station would have been expensive and would have taken too long and caused too much disruption to ongoing operations.
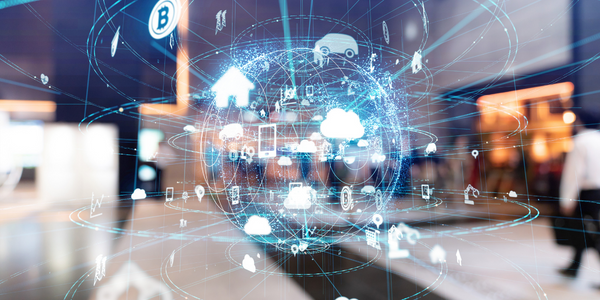
Case Study
Real-Time IoT Tracking and Visualization Improve Manufacturing
Shimane Fujitsu, a wholly-owned subsidiary of Fujitsu and a leading manufacturer of business notebooks and tablets, set out to improve processes where factory inspections found product errors. Prioritizing product rework based on shipping date was challenging, and it caused Shimane Fujitsu to incur additional shipping fees. The company needed a way to collect data to better track the location of products in the rework cycle as well as monitor progress in real time. The collected data would also help process analysis for future improvements.
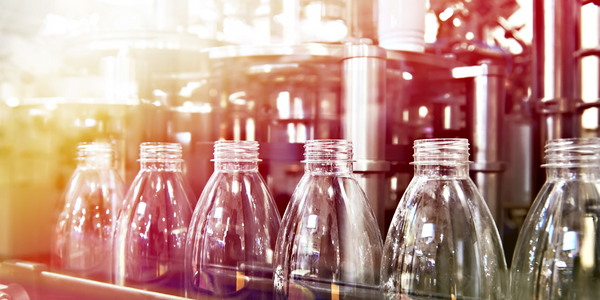
Case Study
Automatic Vision Inspection Solution for Product Traceability
With greater market demand for food safety, traceability is receiving increasingly more attention in the food and beverage industry as well as the packaging industry. One of the world's leading providers of beverage containers required a system to identify bar codes and alphanumeric characters on ink-jet-printed labels at a run rate of 7 units and minimum 99.9% accuracy. Since there were few engineers in the factory, the customer sought to implement a reliable system with an easy-to-use GUI for workers with a less technical background.
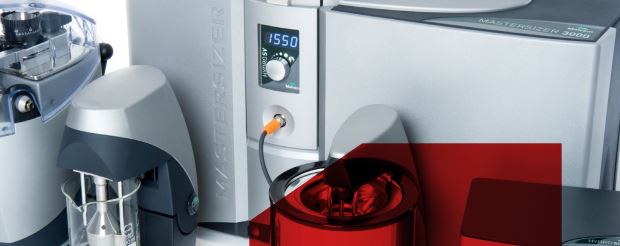
Case Study
Centralizing Data for Improved Efficiency: A Case Study on Malvern Panalytical
Malvern Panalytical, a UK-based hi-tech electronics company, was grappling with the challenge of decentralized data storage. The company had a vast amount of unstructured data scattered across various platforms, from hard drives to emails and floppy disks. This made the data searching process extremely cumbersome and inefficient. The company's rapid growth, from 200 to over 1,000 employees in a decade, and expansion across three continents further exacerbated the need for a more structured and centralized data system. As a company involved in electronics manufacturing and software development, it was crucial for Malvern Panalytical to find a platform that could structure all their data, track all modifications of documents in real time, and provide clear visibility of the internal information flow across all its facilities.
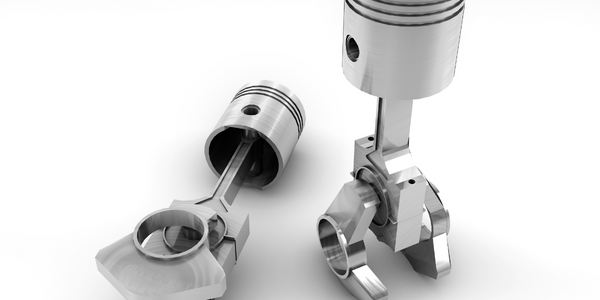
Case Study
Automated Inspection of Axial Piston Motors
Earth moving machines require an immense energy source to provide the power they need for use within civil engineering works. ‘Hydraulic Motors’ allow this power to be applied to enable the machines movement and in addition ‘Control Valves’ also provide the operator with the precise feel and control required to undertake the necessary tasks needed for such machines, including trenching, rock breaking and demolition. These same motors are also used in cranes, wheel loaders and general construction equipment. Though not a new product, the designs of such motors and control valves have been around a few decades, the overall method for manufacture has changed rapidly over the last few years to take account of the need for more modular designs, manufacture and just-in-time manufacturing. Kawasaki Precision Machinery (UK) Ltd based in Plymouth, UK is one of the leading manufacturers of such motors and pumps. They approached Industrial Vision Systems Ltd to come up with a solution to provide automated inspection of such pumps for their semi-automated assembly process. The pumps requiring inspection are at a sub-assembly stage when they are due for the inspection process to take place. Due to the highly modular nature of the construction each part of the pump can have many different derivatives which overall have a different effect on the pump in industrial use. It is therefore critical for the manufacturing process to check all components are the correct type and number for the construction of the pump to begin. Once built it is difficult and costly to rework such units if a fault is detected later in the manufacturing process, therefore automated visual inspection is critical for the success in building quality motors and pumps.