Customer Company Size
SME
Region
- America
Country
- United States
Product
- Sage 100 Advanced ERP
- Sage ACT!
- Sage Fixed Assets
- Visual Integrator
- Business Alerts
Tech Stack
- Windows NT
- SAP Crystal Reports
Implementation Scale
- Enterprise-wide Deployment
Impact Metrics
- Productivity Improvements
- Cost Savings
Technology Category
- Application Infrastructure & Middleware - API Integration & Management
Applicable Functions
- Discrete Manufacturing
Use Cases
- Inventory Management
- Manufacturing System Automation
Services
- System Integration
- Software Design & Engineering Services
About The Customer
QesTec, Inc. is a company that provides computer options such as upgrades for servers, workstations, personal computers, laptops, notebooks, and printers. The company prides itself on offering innovative, practical, and top-quality products, designed to be easily accessible and competitively priced. In addition to its own compatible memory products, QesTec currently supports many of the industry’s most prominent product lines including Digital/Compaq enterprise and storage options, Kingston Technologies compatible memory products, and Sun Microsystems server and storage options. The company is located in Auburn, Massachusetts and has three locations. It employs 20 people.
The Challenge
QesTec, a provider of computer options such as upgrades for servers, workstations, personal computers, laptops, notebooks, and printers, was experiencing booming demand for its high-tech products. This led to a situation where the business was doubling every year, and the company’s computer system simply couldn’t keep up with it. Inventory was turning at least 25 times a year. The time had come to replace standalone PCs with a robust network, including software that would provide manufacturing and inventory management systems plus wider access to customer information. In other words, it was time to migrate up from Sage 50—U.S. Edition, the accounting package that had worked so well during QesTec’s earlier days.
The Solution
QesTec implemented a full-featured networked computer system on Windows® NT, and selected Sage 100 ERP as its accounting solution. Deciding factors included the ability of Sage 100 ERP to maximize benefits of client/server technology such as performance and reliability. Also, it offered real-time inventory analysis with multiple user stations. And as an added bonus, transitioning records from Sage 50 to Sage 100 ERP would be easy. Sage 100 ERP was configured to calculate the costs of building memory upgrade products, recalculate the cost of finished goods, and then enter figures back in for finished products. It transformed the company’s data input process, eliminating the need for massive amounts of paperwork and double entries.
Operational Impact
Quantitative Benefit
Case Study missing?
Start adding your own!
Register with your work email and create a new case study profile for your business.
Related Case Studies.
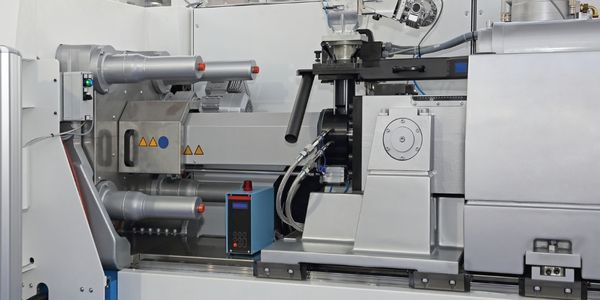
Case Study
Plastic Spoons Case study: Injection Moulding
In order to meet customer expectations by supplying a wide variety of packaging units, from 36 to 1000 spoons per package, a new production and packaging line needed to be built. DeSter wanted to achieve higher production capacity, lower cycle time and a high degree of operator friendliness with this new production line.
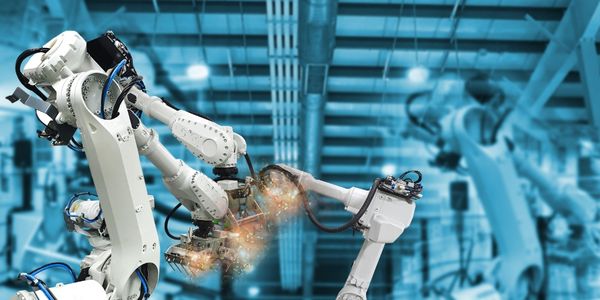
Case Study
Robot Saves Money and Time for US Custom Molding Company
Injection Technology (Itech) is a custom molder for a variety of clients that require precision plastic parts for such products as electric meter covers, dental appliance cases and spools. With 95 employees operating 23 molding machines in a 30,000 square foot plant, Itech wanted to reduce man hours and increase efficiency.
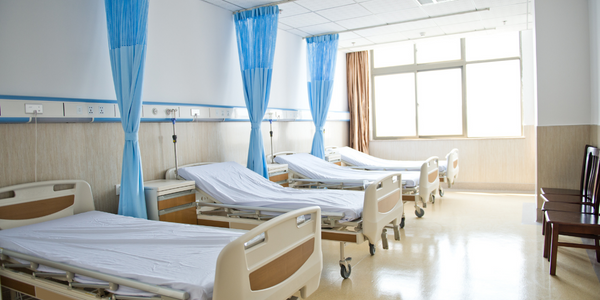
Case Study
Hospital Inventory Management
The hospital supply chain team is responsible for ensuring that the right medical supplies are readily available to clinicians when and where needed, and to do so in the most efficient manner possible. However, many of the systems and processes in use at the cancer center for supply chain management were not best suited to support these goals. Barcoding technology, a commonly used method for inventory management of medical supplies, is labor intensive, time consuming, does not provide real-time visibility into inventory levels and can be prone to error. Consequently, the lack of accurate and real-time visibility into inventory levels across multiple supply rooms in multiple hospital facilities creates additional inefficiency in the system causing over-ordering, hoarding, and wasted supplies. Other sources of waste and cost were also identified as candidates for improvement. Existing systems and processes did not provide adequate security for high-cost inventory within the hospital, which was another driver of cost. A lack of visibility into expiration dates for supplies resulted in supplies being wasted due to past expiry dates. Storage of supplies was also a key consideration given the location of the cancer center’s facilities in a dense urban setting, where space is always at a premium. In order to address the challenges outlined above, the hospital sought a solution that would provide real-time inventory information with high levels of accuracy, reduce the level of manual effort required and enable data driven decision making to ensure that the right supplies were readily available to clinicians in the right location at the right time.
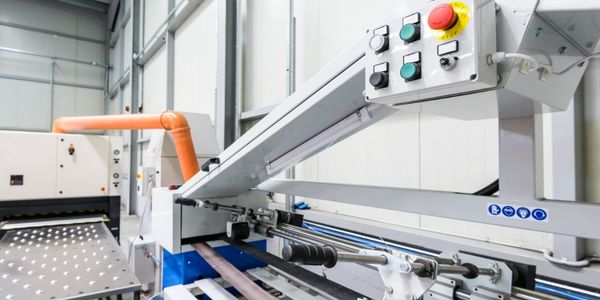
Case Study
Fully Automated Visual Inspection System
Tofflon has developed a fully automatic machine that uses light to inspect vials, medicine bottles, or infusion containers for glass fragments, aluminum particles, rubber grains, hairs, fibers, or other contaminants. It also detects damaged containers with cracks or inclusions (microscopic imperfections), automatically removing faulty or contaminated products. In order to cover all production processes for freeze-dried pharmaceuticals, Tofflon needed to create an open, consistent, and module-based automation concept.
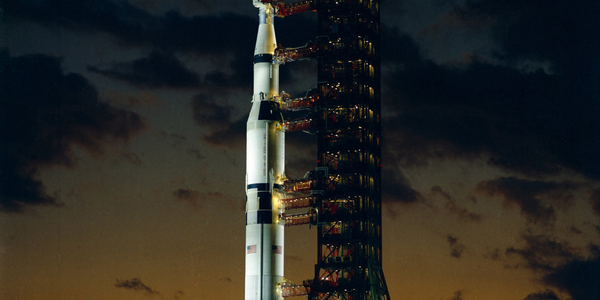
Case Study
SAP Leonardo Enabling Rocket Science
At times, ULA has as many as 15 different operating systems dedicated to overlapping processes, such as rocket design, testing, and launch. Multiple systems created unnecessary costs and unwanted confusion among workers at offices, factories, and launch sites in different location. In order to improve collaboration and transparency during vital activities that directly influence mission success, ULA wanted to improve data sharing and streamline manufacturing processes.