Technology Category
- Networks & Connectivity - Ethernet
- Wearables - Backpack
Applicable Industries
- Aerospace
- Buildings
Applicable Functions
- Procurement
- Product Research & Development
Use Cases
- Building Automation & Control
- Virtual Prototyping & Product Testing
Services
- System Integration
About The Customer
ThyssenKrupp Elevator, part of the Germany-based ThyssenKrupp Corporation, is one of the world's leading elevator companies. With sales of €6.4 billion and more than 50,000 employees at 900 locations, the company’s products are installed in buildings throughout the world. ThyssenKrupp Elevator’s design and engineering teams are known for their innovative solutions to the challenges posed by modern architecture. They developed an elevator system that uses electro-magnetic drives attached to the cabin frame, eliminating the need for roof-mounted cables and allowing the elevator to travel the full 800-meter distance of the world's tallest buildings.
The Challenge
The architecture industry is witnessing a trend of taller and more elaborate buildings, with the world’s tallest skyscraper, the Burj Khalifa, standing at 828 meters. This height brings unique challenges, particularly in transporting people from the ground floor to the top efficiently. Traditional elevator systems, which operate via cable systems located at the top floor of the building, offer a maximum ride height of up to 400 meters, just half the distance of the world’s tallest building. This necessitates passengers to ride two or more elevators to reach the top level. ThyssenKrupp Elevator, a leading elevator company, developed an elevator that uses electro-magnetic drives attached to the cabin frame, eliminating the need for roof-mounted cables and allowing the elevator to travel the full 800-meter distance. However, this new system could not carry as much weight as a traditional elevator. The challenge was to ensure the new design was as lightweight as possible to maximize the loading capacity of the cabins.
The Solution
Altair ProductDesign was selected to explore methods and materials that could help minimize the weight of the design. They developed a three-stage approach. In the first stage, a topology optimization study was performed on the BackPack concept using OptiStruct, a design optimization solution within Altair’s HyperWorks suite of simulation tools. The software suggested the most efficient layout of material for the cabin's structure while meeting design requirements. In the second stage, the thicknesses of the materials were investigated. The team explored the lightweight potential of sandwich panel structures where aluminium or plastic facing sheets are used with a foam core. Using OptiStruct, the team performed a sizing optimization process to explore the thicknesses of the wall facing sheets and the foam core. In the third stage, the team explored new materials, particularly carbon fiber, for the walls of the new cabin. An optimization study was developed to find the ideal thickness of material, fiber ply shapes, and lay-up orientation of each layer.
Operational Impact
Quantitative Benefit
Case Study missing?
Start adding your own!
Register with your work email and create a new case study profile for your business.
Related Case Studies.
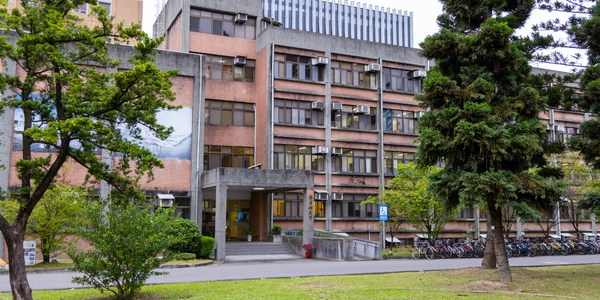
Case Study
Energy Saving & Power Monitoring System
Recently a university in Taiwan was experiencing dramatic power usage increases due to its growing number of campus buildings and students. Aiming to analyze their power consumption and increase their power efficiency across 52 buildings, the university wanted to build a power management system utilizing web-based hardware and software. With these goals in mind, they contacted Advantech to help them develop their system and provide them with the means to save energy in the years to come.
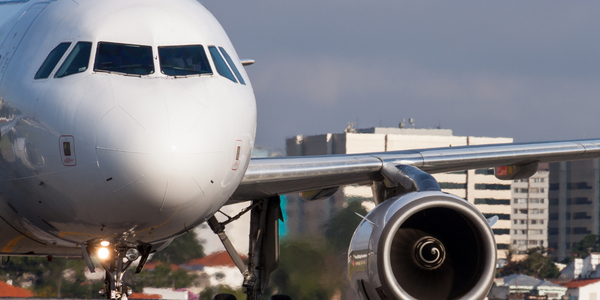
Case Study
Airbus Soars with Wearable Technology
Building an Airbus aircraft involves complex manufacturing processes consisting of thousands of moving parts. Speed and accuracy are critical to business and competitive advantage. Improvements in both would have high impact on Airbus’ bottom line. Airbus wanted to help operators reduce the complexity of assembling cabin seats and decrease the time required to complete this task.
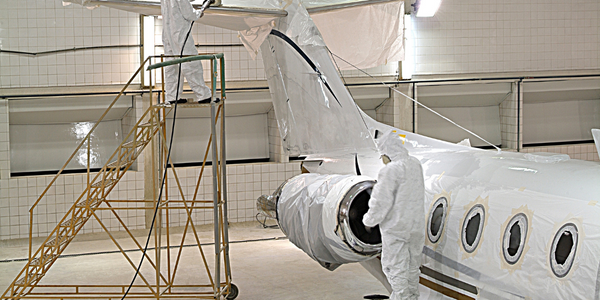
Case Study
Aircraft Predictive Maintenance and Workflow Optimization
First, aircraft manufacturer have trouble monitoring the health of aircraft systems with health prognostics and deliver predictive maintenance insights. Second, aircraft manufacturer wants a solution that can provide an in-context advisory and align job assignments to match technician experience and expertise.
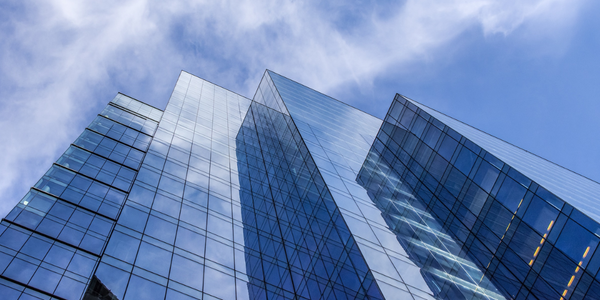
Case Study
Intelligent Building Automation System and Energy Saving Solution
One of the most difficult problems facing the world is conserving energy in buildings. However, it is not easy to have a cost-effective solution to reduce energy usage in a building. One solution for saving energy is to implement an intelligent building automation system (BAS) which can be controlled according to its schedule. In Indonesia a large university with a five floor building and 22 classrooms wanted to save the amount of energy being used.
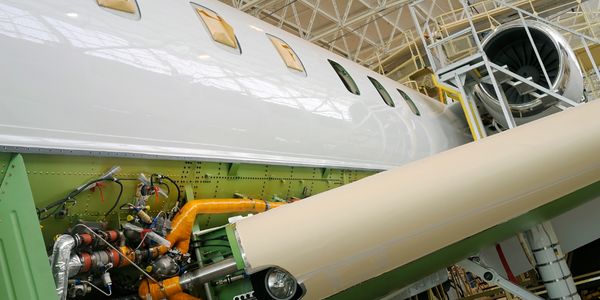
Case Study
Aerospace & Defense Case Study Airbus
For the development of its new wide-body aircraft, Airbus needed to ensure quality and consistency across all internal and external stakeholders. Airbus had many challenges including a very aggressive development schedule and the need to ramp up production quickly to satisfy their delivery commitments. The lack of communication extended design time and introduced errors that drove up costs.
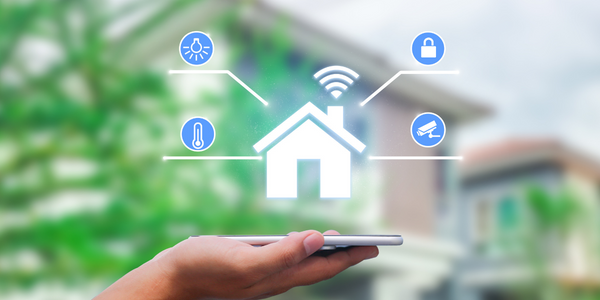
Case Study
Powering Smart Home Automation solutions with IoT for Energy conservation
Many industry leaders that offer Smart Energy Management products & solutions face challenges including:How to build a scalable platform that can automatically scale-up to on-board ‘n’ number of Smart home devicesData security, solution availability, and reliability are the other critical factors to deal withHow to create a robust common IoT platform that handles any kind of smart devicesHow to enable data management capabilities that would help in intelligent decision-making