Technology Category
- Functional Applications - Inventory Management Systems
- Platform as a Service (PaaS) - Application Development Platforms
Applicable Industries
- Automotive
Applicable Functions
- Procurement
- Warehouse & Inventory Management
Use Cases
- Inventory Management
- Picking, Sorting & Positioning
About The Customer
The customer is one of India's largest paint manufacturers with a presence in multiple countries. The company serves both B2C and B2B business segments, including Decorative, Automotive, General Industrial, and Coatings. The company was growing rapidly and was facing challenges in managing its demand and supply planning processes due to high dependency on manual activities and Excel spreadsheets. The company primarily relied on the Annual Operating Plan (AOP) to determine future demand, which meant they were unable to keep up with the latest market trends. There was limited collaboration between sales, marketing, and supply chain teams, leading to inaccuracies in a heavily regional, promo-driven market.
The Challenge
One of India's largest paint manufacturers, with a presence in multiple countries and serving both B2C and B2B business segments, was facing significant challenges in managing its demand and supply planning processes. The company was growing rapidly, and its existing processes, heavily reliant on manual activities and Excel spreadsheets, were unable to support this growth. The company primarily relied on the Annual Operating Plan (AOP) to determine future demand, which meant they were unable to keep up with the latest market trends. There was limited collaboration between sales, marketing, and supply chain teams, leading to inaccuracies in a heavily regional, promo-driven market. The stocking of depots was controlled by basic automation and overridden by sales team-based manual replenishment requests, leading to slow-moving inventory and stockouts. With a limited planning horizon (one month) and a weekly production plan, the procurement teams struggled to estimate the inventory requirements for raw materials, leading to stockouts or excess inventory with teams operating in silos.
The Solution
The company partnered with o9 to leverage its advanced machine learning analytics and consensus forecasting capabilities to drive improvements in forecast accuracy. The manual work was removed, and a complete overview was generated using o9’s integrated platform for inventory planning, procurement planning, and master planning. The company was able to leverage o9’s optimization engine, providing an efficient way to arrive at inventory requirements based on matching demand, supply, and inventory levels across time horizons. The Enterprise Knowledge Graph was used to implement a complete end-to-end Integrated Business Planning (IBP) process. This includes demand planning in collaboration with sales and marketing, distribution planning, master planning, procurement planning, and S&OP. The manual Excel-based planning and homegrown solutions were replaced with o9's platform.
Operational Impact
Quantitative Benefit
Case Study missing?
Start adding your own!
Register with your work email and create a new case study profile for your business.
Related Case Studies.
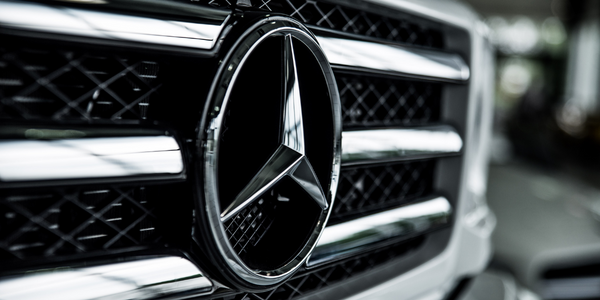
Case Study
Integral Plant Maintenance
Mercedes-Benz and his partner GAZ chose Siemens to be its maintenance partner at a new engine plant in Yaroslavl, Russia. The new plant offers a capacity to manufacture diesel engines for the Russian market, for locally produced Sprinter Classic. In addition to engines for the local market, the Yaroslavl plant will also produce spare parts. Mercedes-Benz Russia and his partner needed a service partner in order to ensure the operation of these lines in a maintenance partnership arrangement. The challenges included coordinating the entire maintenance management operation, in particular inspections, corrective and predictive maintenance activities, and the optimizing spare parts management. Siemens developed a customized maintenance solution that includes all electronic and mechanical maintenance activities (Integral Plant Maintenance).
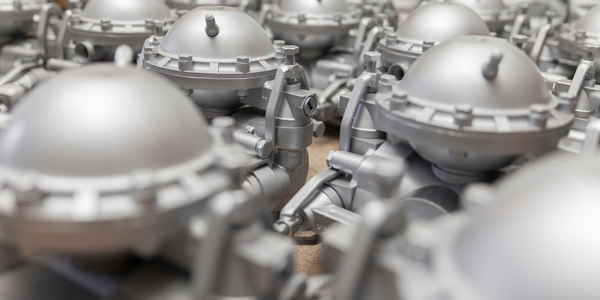
Case Study
Monitoring of Pressure Pumps in Automotive Industry
A large German/American producer of auto parts uses high-pressure pumps to deburr machined parts as a part of its production and quality check process. They decided to monitor these pumps to make sure they work properly and that they can see any indications leading to a potential failure before it affects their process.