Customer Company Size
Large Corporate
Region
- Europe
Country
- Finland
Product
- Klipfolio Dashboard
Tech Stack
- Google Spreadsheets
- Adobe Insights
- MailChimp
- Google Analytics
- comScore
- Meltwater media monitoring
Implementation Scale
- Enterprise-wide Deployment
Impact Metrics
- Productivity Improvements
- Digital Expertise
Technology Category
- Analytics & Modeling - Real Time Analytics
- Platform as a Service (PaaS) - Data Management Platforms
Applicable Functions
- Business Operation
Use Cases
- Real-Time Location System (RTLS)
- Process Control & Optimization
Services
- Data Science Services
About The Customer
Sanoma is a leading consumer media and learning company in Europe. The company has a dominant market share position in Finland and the Netherlands with multiple broadcast and online content delivery channels. Sanoma is listed on the NASDAQ OMX Helsinki Stock Exchange and its net sales in 2013 totaled 2.2 billion euros. Like many media companies, Sanoma understood that it needed to provide the sports, entertainment and information programming its viewers demanded, whenever and wherever they wanted it. This led to the launch of new online streaming and web-based content in addition to the organization’s already leading traditional broadcast services.
The Challenge
Sanoma, a leading consumer media and learning company in Europe, was facing the challenge of tracking and managing metrics for its new online streaming and web-based content. The new content distribution channels created complexities for tracking and metrics management. The online streaming generated a large amount of data about viewership behaviour and content consumption patterns that needed to be effectively tracked and analyzed. In addition, Sanoma had recently signed a lucrative content deal to live stream Finnish Elite League - Liiga hockey games. This deal created a significant need within the management team to track viewer behaviour and feedback up-to-the-minute, to ensure they were generating a solid return on investment. Previous viewership statistics were tracked using Excel spreadsheets, which were difficult to compile and provided a disjointed view of what was really happening online.
The Solution
Sanoma adopted Klipfolio Dashboard as a solution to their challenge. Klipfolio Dashboard allowed Sanoma to integrate disparate data sources into a single dashboard and create dashboards quickly for web and mobile delivery. Petri Mertanen, a member of Sanoma's team, started a Klipfolio trial and by the end of the first weekend, he had a sample dashboard to show to the VP of Online at Nelonen Media. The VP was impressed with the interactivity of the visuals and the ability to view the dashboard on a mobile device. Within a month, Petri was able to push out complete dashboard reports with Klipfolio, targeted at development, directors and executives, as well as the online analyst team. Starting with a few key data sources, like Adobe Insights and Google Spreadsheets, Mertanen was able to quickly create dynamic, user-friendly dashboards.
Operational Impact
Quantitative Benefit
Case Study missing?
Start adding your own!
Register with your work email and create a new case study profile for your business.
Related Case Studies.
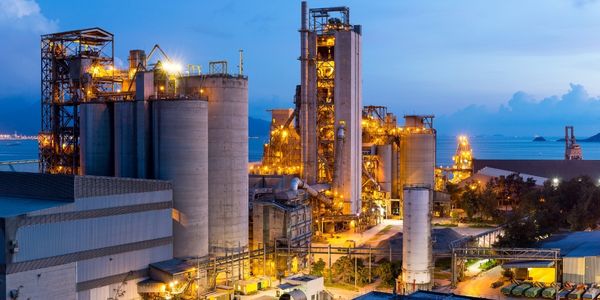
Case Study
System 800xA at Indian Cement Plants
Chettinad Cement recognized that further efficiencies could be achieved in its cement manufacturing process. It looked to investing in comprehensive operational and control technologies to manage and derive productivity and energy efficiency gains from the assets on Line 2, their second plant in India.
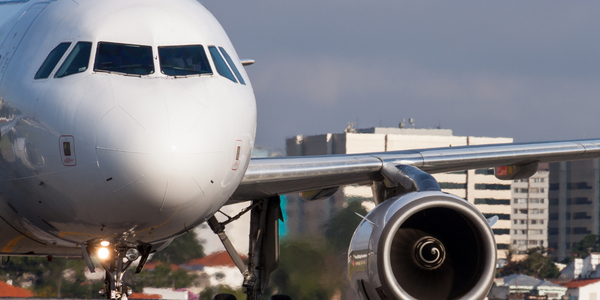
Case Study
Airbus Soars with Wearable Technology
Building an Airbus aircraft involves complex manufacturing processes consisting of thousands of moving parts. Speed and accuracy are critical to business and competitive advantage. Improvements in both would have high impact on Airbus’ bottom line. Airbus wanted to help operators reduce the complexity of assembling cabin seats and decrease the time required to complete this task.
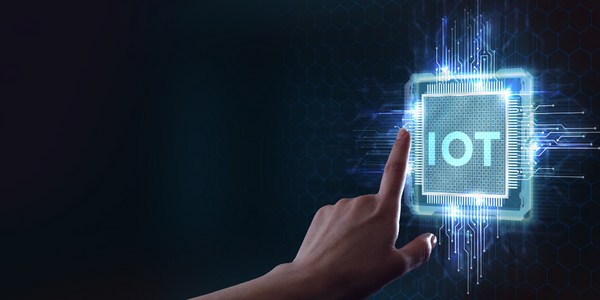
Case Study
Leading Tools Manufacturer Transforms Operations with IoT
Stanley Black & Decker required transparency of real-time overall equipment effectiveness and line productivity to reduce production line change over time.The goal was to to improve production to schedule, reduce actual labor costs and understanding the effects of shift changes and resource shifts from line to line.
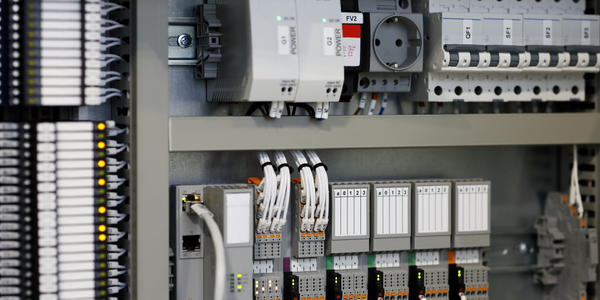
Case Study
Improving Production Line Efficiency with Ethernet Micro RTU Controller
Moxa was asked to provide a connectivity solution for one of the world's leading cosmetics companies. This multinational corporation, with retail presence in 130 countries, 23 global braches, and over 66,000 employees, sought to improve the efficiency of their production process by migrating from manual monitoring to an automatic productivity monitoring system. The production line was being monitored by ABB Real-TPI, a factory information system that offers data collection and analysis to improve plant efficiency. Due to software limitations, the customer needed an OPC server and a corresponding I/O solution to collect data from additional sensor devices for the Real-TPI system. The goal is to enable the factory information system to more thoroughly collect data from every corner of the production line. This will improve its ability to measure Overall Equipment Effectiveness (OEE) and translate into increased production efficiencies. System Requirements • Instant status updates while still consuming minimal bandwidth to relieve strain on limited factory networks • Interoperable with ABB Real-TPI • Small form factor appropriate for deployment where space is scarce • Remote software management and configuration to simplify operations