Customer Company Size
Mid-size Company
Region
- America
Country
- United States
Product
- Planning Maestro
Tech Stack
- QuickBooks
- Excel
Implementation Scale
- Enterprise-wide Deployment
Impact Metrics
- Productivity Improvements
- Cost Savings
Technology Category
- Functional Applications - Enterprise Resource Planning Systems (ERP)
Applicable Functions
- Business Operation
Use Cases
- Demand Planning & Forecasting
- Asset Lifecycle Management
Services
- Cloud Planning, Design & Implementation Services
About The Customer
Amwaste, LLC is a full-service waste and recycling company with operations in Alabama, Georgia, and Louisiana. The company was founded in April of 2010 and began serving in the Birmingham market with its roll off (demolition removal services) and landfill operations. Since then, it has expanded its service offerings to include everything from residential garbage collection to recycling to portable toilets and holding tanks. Amwaste is a collection of multiple entities, organized by state and landfill, each requiring its own budget and forecast. Additionally, an overall budget and forecast is needed for the parent company, Matter Management Enterprises. The company has over 400 employees and uses NetSuite for its General Ledger.
The Challenge
Amwaste, LLC, a full-service waste and recycling company, was facing challenges in managing its budgeting process due to its complex organizational structure. The company is a collection of multiple entities, each requiring its own budget and forecast. Additionally, an overall budget and forecast is needed for the parent company, Matter Management Enterprises. Each service offered by Amwaste has unique business drivers that shape the companies. For instance, in the residential pickup business, revenue is driven by the number of homes under contract or serviced, while expenses are driven by days in the month. Roll-off customers are charged based on the number of services provided, while commercial front load customers are charged a fixed monthly fee, but the longer the month, the higher the labor costs. Initially, Amwaste had just three entities, each of which had its own QuickBooks database and budget. To create an annual budget, Amwaste’s CFO, David Carlisle, pulled data from the three QuickBooks databases and manually re-entered it into three separate Excel spreadsheets. Once the spreadsheets were completed he rolled them up to a single budget for the company.
The Solution
As the company began to grow, Mr. Carlisle wanted a more streamlined and accurate way to manage the overall budgeting process. He was familiar with Planning Maestro, a robust FP&A platform, as he purchased it for a former employer. He was eager to bring the same benefits to Amwaste. Mr. Carlisle particularly likes the advanced reporting features part of the platform, which provide accurate and reliable graphical representations of Amwaste’s financial data, and integrates with its GL. Using Planning Maestro, Mr. Carlisle was able to create a five-year rolling forecast, with a particular focus on the 18-month horizon. Once monthly actuals come in, he easily updates the forecasts for each entity, enabling him to monitor each company’s health, as well as the overall financial picture for Matter Management Enterprises. For complex sales proposals, such as responding to an RFP from a municipality, Mr. Carlisle will first build a budget in Planning Maestro using all of the correct drivers and actual costs. The result is a more accurate proposal, a critical criteria for long-term contracts.
Operational Impact
Quantitative Benefit
Case Study missing?
Start adding your own!
Register with your work email and create a new case study profile for your business.
Related Case Studies.
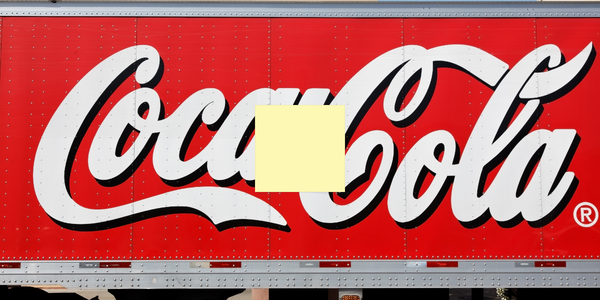
Case Study
Coca-Cola Refreshments, U.S.
Coca-Cola Refreshments owns and manages Coca-Cola branded refrigerators in retail establishments. Legacy systems were used to locate equipment information by logging onto multiple servers which took up to 8 hours to update information on 30-40 units. The company had no overall visibility into equipment status or maintenance history.
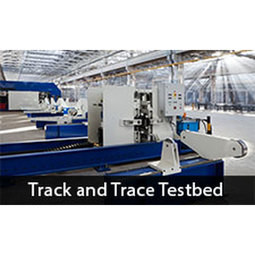
Case Study
IIC - Track and Trace Testbed
Factory systems can detect - within a meter - the location of a tool; Misuse of tools can result in serious accident or injury; The production of many industrial and consumer goods requires exacting work - down to the precise force used to tighten a screw. GOAL Manage smart, hand-held tools in manufacturing, maintenance, and industrial environments
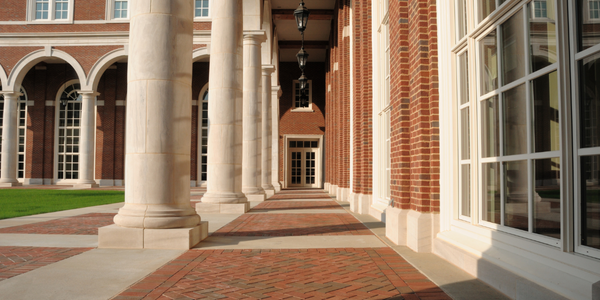
Case Study
IIC Asset Efficiency Testbed
A recent study on maturity of Asset Efficiency from Infosys and the Institute for Industrial Management (FIR) at Aachen University revealed that 85 percent of manufacturing companies globally are aware of asset efficiency, but only 15 percent have implemented it at a systematic level. Current challenges include lack of instrumentation of the assets, missing real-time data analytics, lack of context due to missing information from other systems, and lack of a holistic focus with other aspects of efficiency like energy, utilization, operations, and serviceability.GOALTo collect asset information efficiently and accurately in real-time and run analytics to make the right decisions