Technology Category
- Sensors - GPS
Use Cases
- Personnel Tracking & Monitoring
- Time Sensitive Networking
About The Customer
Follow Leisure Group is a leading hospitality operator in Northern Ireland, owning several popular eateries including Slim's Healthy Kitchen, Canteen, Output Espresso, and Morning Martha. The company creates brands, communities, and social spaces with a fresh, creative, and innovative approach. They supply, manage, and franchise market-leading brands within the Hospitality and Leisure industry. The company has over 100 employees across nine locations and has been in operation since 2018.
The Challenge
Follow Leisure Group, a multi-venue hospitality operator in Northern Ireland, was grappling with the challenges of managing daily operations across its various brands. The founder, Gary McIldowney, was well aware of the time-consuming tasks involved in running the business, such as creating schedules, reviewing employee time cards, and running payroll. These tasks were being managed using outdated methods like pen and paper, clunky machines, and multiple spreadsheets. Additionally, staff could only check their rota schedules on a printout at work, leading to confusion and clashes due to multiple forms of communication like Whatsapp, email, and phone calls. The company was in dire need of a software solution that could streamline these processes, save time, and reduce costs.
The Solution
Follow Leisure Group chose Bizimply for its ease of use and its ability to consolidate three different processes into one simple dashboard. The goal was to lower labour costs and streamline their outdated processes. After implementing Bizimply, the company immediately started to see the benefits. Bizimply's accuracy and consistency were key advantages. It helped the restaurants and cafes achieve a baseline labour cost across the Group. With granular insight into their data, they were able to better forecast demand and lower costs across multiple locations. The software also improved workforce management across each location, leading to increased productivity and better communication among teams.
Operational Impact
Quantitative Benefit
Case Study missing?
Start adding your own!
Register with your work email and create a new case study profile for your business.
Related Case Studies.
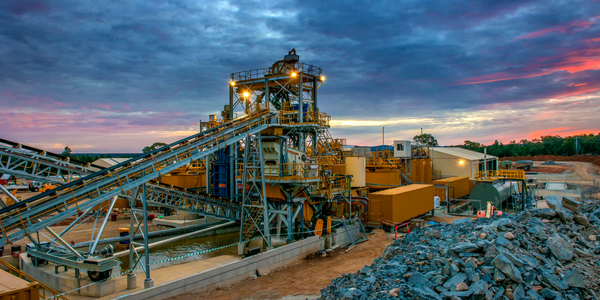
Case Study
Goldcorp: Internet of Things Enables the Mine of the Future
Goldcorp is committed to responsible mining practices and maintaining maximum safety for its workers. At the same time, the firm is constantly exploring ways to improve the efficiency of its operations, extend the life of its assets, and control costs. Goldcorp needed technology that can maximize production efficiency by tracking all mining operations, keep employees safe with remote operations and monitoring of hazardous work areas and control production costs through better asset and site management.
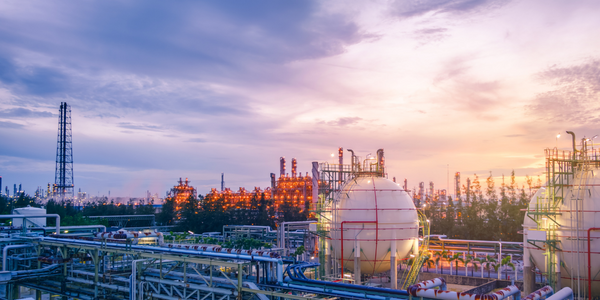
Case Study
Cisco Kinetic for Oil and Gas: Refineries and Plants
The plant manager and safety teams needed a solution that provided near real-time visibility of gas detection and personnel location, with easy to understand visualization and alerting dashboards. This would enable them to improve productivity through decreasing the time taken to start work, optimize evacuation route planning, and to meet critical staff safety and compliance goals.
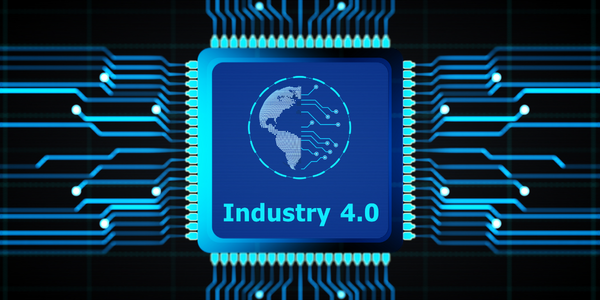
Case Study
Industry 4.0 at ALPLA: Enhancing Factory Efficiency with IoT
ALPLA, a global leader in packaging solutions, faced several challenges as the complexity of their production machinery increased. The need for highly trained specialists in each factory led to higher personnel costs, difficulties in recruiting experienced talent at each location, and costly personnel turnover. Furthermore, less experienced operators running the machines sub-optimally impacted resource consumption and overall equipment effectiveness (OEE). ALPLA also faced the challenge of monitoring visual inspection systems in every line of their plants, which was almost impossible to do manually. In 2016, ALPLA decided to use data from the 900 different types of embedded sensors in each factory to address these issues. However, their initial choice of SQL Server as the data store for the sensor data proved inadequate, as it was unable to cope with their data requirements.
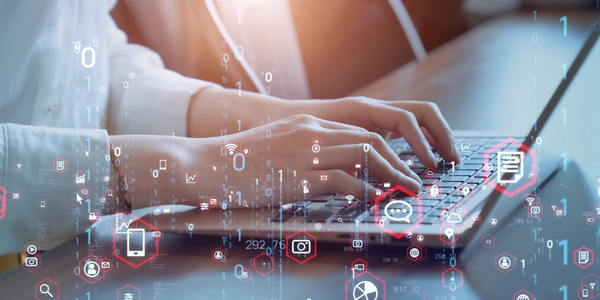
Case Study
Digital Transformation of Atlanta Grout & Tile: An IoT Case Study
Atlanta Grout & Tile, a Tile, Stone & Grout restoration company based in Woodstock, Georgia, was facing challenges with its traditional business model. Despite steady growth over the years, the company was falling behind the web revolution and missing out on the opportunity to tap into a new consumer base. They were using independent software from different vendors for each of their department information and workforce management. This resulted in a lot of manual work on excel and the need to export/import data between different systems. This not only increased overhead costs but also slowed down their response to clients. The company also had to prepare numerous reports manually and lacked access to customer trends for effective business decision-making.
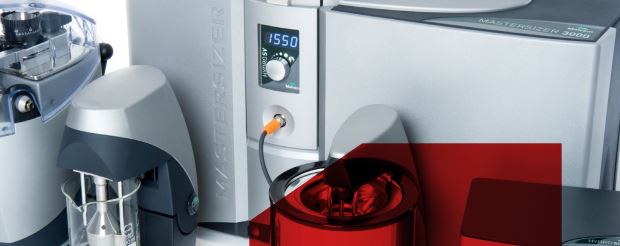
Case Study
Centralizing Data for Improved Efficiency: A Case Study on Malvern Panalytical
Malvern Panalytical, a UK-based hi-tech electronics company, was grappling with the challenge of decentralized data storage. The company had a vast amount of unstructured data scattered across various platforms, from hard drives to emails and floppy disks. This made the data searching process extremely cumbersome and inefficient. The company's rapid growth, from 200 to over 1,000 employees in a decade, and expansion across three continents further exacerbated the need for a more structured and centralized data system. As a company involved in electronics manufacturing and software development, it was crucial for Malvern Panalytical to find a platform that could structure all their data, track all modifications of documents in real time, and provide clear visibility of the internal information flow across all its facilities.