技术
- 传感器 - 全球定位系统
用例
- 人员跟踪与监控
- 时间敏感网络
关于客户
Follow Leisure Group 是北爱尔兰领先的酒店运营商,拥有多家受欢迎的餐馆,包括 Slim's Healthy Kitchen、Canteen、Output Espresso 和 Morning Martha。该公司以新鲜、创意和创新的方式创建品牌、社区和社交空间。他们供应、管理和特许经营酒店和休闲行业的市场领先品牌。该公司自 2018 年开始运营,分布在 9 个地点,拥有 100 多名员工。
挑战
Follow Leisure Group 是北爱尔兰的一家多场所酒店运营商,该集团一直在应对管理各个品牌日常运营的挑战。创始人加里·麦克唐尼 (Gary McIldowney) 非常清楚运营业务所涉及的耗时任务,例如创建时间表、审查员工考勤卡和运行工资单。这些任务是使用过时的方法来管理的,例如笔和纸、笨重的机器和多个电子表格。此外,员工只能在工作时查看打印输出的排班安排,由于 Whatsapp、电子邮件和电话等多种沟通形式,导致混乱和冲突。该公司迫切需要一种软件解决方案来简化这些流程、节省时间并降低成本。
解决方案
Follow Leisure Group 选择 Bizimply 是因为它易于使用,并且能够将三个不同的流程整合到一个简单的仪表板中。目标是降低劳动力成本并简化过时的流程。实施 Bizimply 后,该公司立即开始看到好处。 Bizimply 的准确性和一致性是主要优势。它帮助餐厅和咖啡馆实现了整个集团的基准劳动力成本。通过对数据的精细洞察,他们能够更好地预测多个地点的需求并降低成本。该软件还改善了每个地点的劳动力管理,从而提高了生产力并改善了团队之间的沟通。
运营影响
数量效益
Case Study missing?
Start adding your own!
Register with your work email and create a new case study profile for your business.
相关案例.
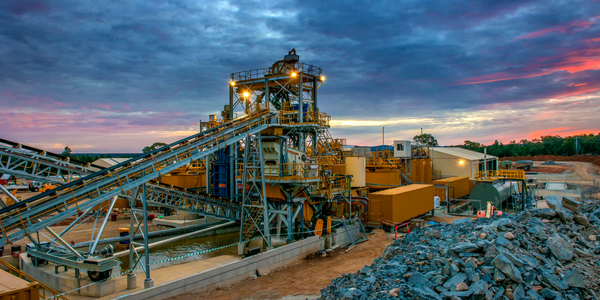
Case Study
Goldcorp: Internet of Things Enables the Mine of the Future
Goldcorp is committed to responsible mining practices and maintaining maximum safety for its workers. At the same time, the firm is constantly exploring ways to improve the efficiency of its operations, extend the life of its assets, and control costs. Goldcorp needed technology that can maximize production efficiency by tracking all mining operations, keep employees safe with remote operations and monitoring of hazardous work areas and control production costs through better asset and site management.
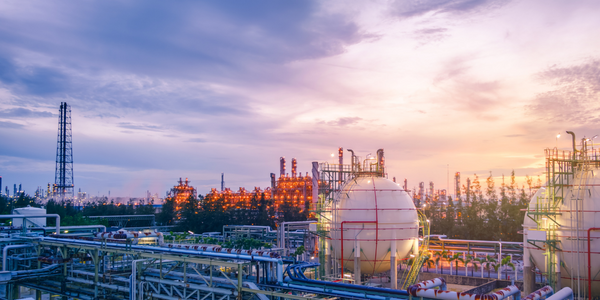
Case Study
Cisco Kinetic for Oil and Gas: Refineries and Plants
The plant manager and safety teams needed a solution that provided near real-time visibility of gas detection and personnel location, with easy to understand visualization and alerting dashboards. This would enable them to improve productivity through decreasing the time taken to start work, optimize evacuation route planning, and to meet critical staff safety and compliance goals.
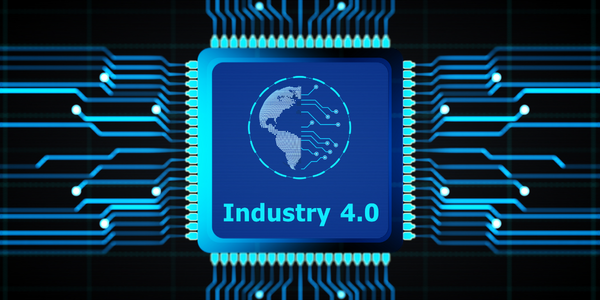
Case Study
Industry 4.0 at ALPLA: Enhancing Factory Efficiency with IoT
ALPLA, a global leader in packaging solutions, faced several challenges as the complexity of their production machinery increased. The need for highly trained specialists in each factory led to higher personnel costs, difficulties in recruiting experienced talent at each location, and costly personnel turnover. Furthermore, less experienced operators running the machines sub-optimally impacted resource consumption and overall equipment effectiveness (OEE). ALPLA also faced the challenge of monitoring visual inspection systems in every line of their plants, which was almost impossible to do manually. In 2016, ALPLA decided to use data from the 900 different types of embedded sensors in each factory to address these issues. However, their initial choice of SQL Server as the data store for the sensor data proved inadequate, as it was unable to cope with their data requirements.
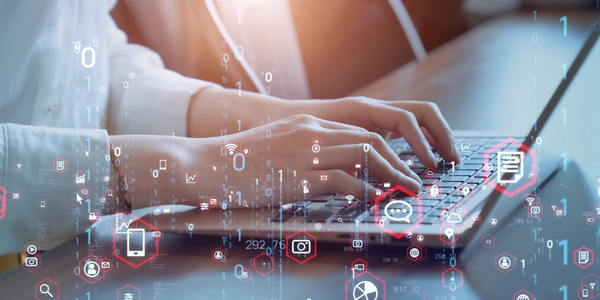
Case Study
Digital Transformation of Atlanta Grout & Tile: An IoT Case Study
Atlanta Grout & Tile, a Tile, Stone & Grout restoration company based in Woodstock, Georgia, was facing challenges with its traditional business model. Despite steady growth over the years, the company was falling behind the web revolution and missing out on the opportunity to tap into a new consumer base. They were using independent software from different vendors for each of their department information and workforce management. This resulted in a lot of manual work on excel and the need to export/import data between different systems. This not only increased overhead costs but also slowed down their response to clients. The company also had to prepare numerous reports manually and lacked access to customer trends for effective business decision-making.
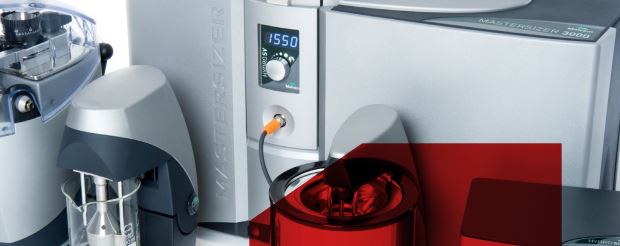
Case Study
Centralizing Data for Improved Efficiency: A Case Study on Malvern Panalytical
Malvern Panalytical, a UK-based hi-tech electronics company, was grappling with the challenge of decentralized data storage. The company had a vast amount of unstructured data scattered across various platforms, from hard drives to emails and floppy disks. This made the data searching process extremely cumbersome and inefficient. The company's rapid growth, from 200 to over 1,000 employees in a decade, and expansion across three continents further exacerbated the need for a more structured and centralized data system. As a company involved in electronics manufacturing and software development, it was crucial for Malvern Panalytical to find a platform that could structure all their data, track all modifications of documents in real time, and provide clear visibility of the internal information flow across all its facilities.