Customer Company Size
Large Corporate
Region
- America
Country
- United States
Product
- 3G Pacejet Shipping
- Infor CloudSuite Industrial (CSI)
Tech Stack
- ERP Integration
- Shipping Platform
Implementation Scale
- Enterprise-wide Deployment
Impact Metrics
- Productivity Improvements
- Customer Satisfaction
Technology Category
- Functional Applications - Enterprise Resource Planning Systems (ERP)
- Functional Applications - Remote Monitoring & Control Systems
Applicable Industries
- Mining
Applicable Functions
- Logistics & Transportation
- Business Operation
Use Cases
- Supply Chain Visibility
- Process Control & Optimization
Services
- System Integration
- Software Design & Engineering Services
About The Customer
Tracing their roots back over 125 years, Syntron Material Handling is most well known for their impact on the mining industry. As the company has grown into a global enterprise, their machinery now assists with everything from handling coal and iron ore to power generation and food processing. With company values including safety and sustainability, collaboration, innovation, and being customer-centric, Syntron needed a shipping solution to help them put their customer’s first.
The Challenge
Working in their Infor CloudSuite Industrial (CSI) environment for shipping with CSI’s out-of-the-box solution wasn’t going to meet their needs based on shipping volume alone. Syntron needed a platform to help them manage their heavy shipping volume and also had compatibility with 3PLs. They landed on Pacejet for a few reasons. In addition to having relationships with Syntron’s 3PLs of choice, Pacejet also didn’t require extensive time from Syntron’s internal team on implementation.
The Solution
Syntron ships about 60% parcel and 40% LTL and having the ability to process both within the same solution is a huge time saver for Syntron’s team. With CSI and Pacejet, Syntron has one integrated ERP and shipping platform allowing the company to be more efficient and freeing up valuable resources for more important things than routine communication with carriers. With Pacejet on-board, Syntron was able to take advantage of easy implementation and focus their resources on other critical areas of their Infor CloudSuite Industrial (CSI) ERP upgrade. By streamlining Syntron’s shipping process and consolidating into one system, Syntron is able to get their shipments out the door faster and have tracking details available immediately following, enhancing their overall customer experience.
Operational Impact
Quantitative Benefit
Case Study missing?
Start adding your own!
Register with your work email and create a new case study profile for your business.
Related Case Studies.
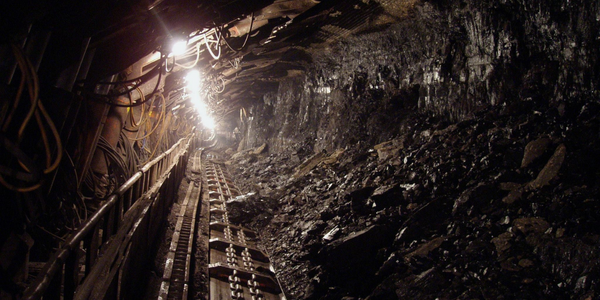
Case Study
Underground Mining Safety
The goal was to produce a safety system to monitor and support underground mining operations; existing systems were either too simple (i.e. phone line) or overly complex and expensive, inhibiting deployment, and providing little-to-no support in event of an accident. Given the dangerous nature of the mining work environment and the strict regulations placed on the industry, the solution would have to comply with Mine Safety and Health Administration (MSHA) regulations. Yet the product needed to allow for simple deployment to truly be a groundbreaking solution - increasing miner safety and changing daily operations for the better.
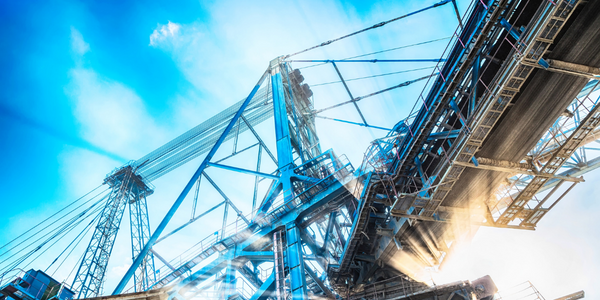
Case Study
Mining Firm Quadruples Production, with Internet of Everything
Dundee Precious Metal’s flagship mine, in Chelopech, Bulgaria, produces a gold, copper, and silver concentrate set a goal to increase production by 30%. Dundee wanted to increase production quality and output without increasing headcount and resources, improve miner safety, and minimize cost.
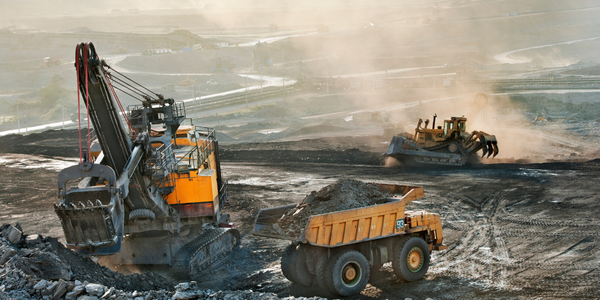
Case Study
Fastenal Builds the Future of Manufacturing with MachineMetrics
Fastenal's objective was to better understand their machine downtime, utilization, quality issues, and to embrace cutting-edge manufacturing technology/process improvement capabilities to bring their team to the next level. However, there was a lack of real-time data, visualization, and actionable insights made this transition impossible.
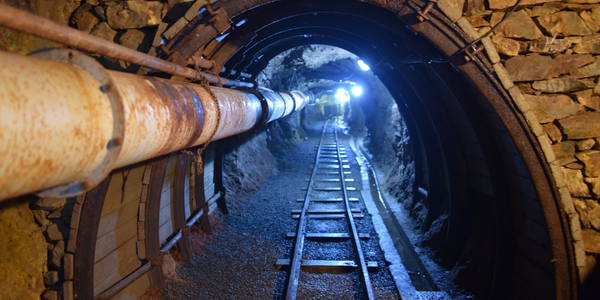
Case Study
Joy Mining Systems
Joy equipment faces many challenges. The first is machine integration and control. The business end of the machine has a rapidly-spinning cylinder with 6-inch diamond-studded cutting teeth. It chews through rock at rates measured in tens of tons per minute. The system grinds through the rock in front, creating a rectangular mine tunnel. Hydraulic lifters support the ceiling as the machine moves forward. Automated drills and screws drive 3-ft long screws into the ceiling to stabilize it. The rock and coal fall into a set of gathering "fingers" below the cutting cylinder. These fingers scoop up the rock and coal and deposit it onto a conveyor belt. The conveyor passes under the machine and out the back. A train of conveyor belt cars, up to a mile long, follows the cutter into the mine. The rock shoots along this train at over 400 feet per minute until it empties into rail cars at the end. Current systems place an operator cage next to the cutter. Choking dust (potentially explosive), the risk of collapse and the proximity of metal and rock mayhem make the operator cage a hazardous location.
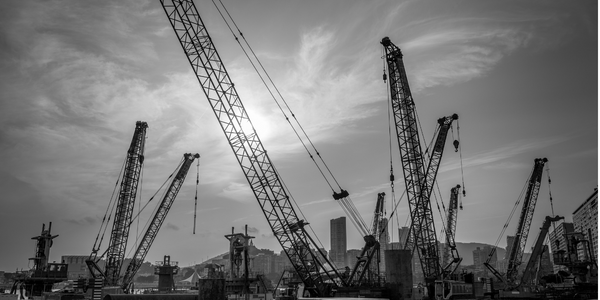
Case Study
Improved Monitoring in Industrial Manufacturing Facility
When your crane is moving tons of magma-hot iron, you can’t afford an unexpected failure. McWane Ductile knew monitoring the crane motor metrics within their facility could help prevent a mechanical failure that would strand an enormous bucket of molten metal overhead. Unfortunately, their legacy wired monitoring system couldn’t work with moving objects in this extreme environment. If they could integrate wireless capabilities into their existing equipment they could extend their monitoring capabilities without starting over from scratch.