Technology Category
- Platform as a Service (PaaS) - Application Development Platforms
Applicable Industries
- Agriculture
- Transportation
Applicable Functions
- Logistics & Transportation
Use Cases
- Farm Monitoring & Precision Farming
- Last Mile Delivery
About The Customer
Tara Firma Farms is a pasture-raised farm and CSA based in the Bay Area. Known for their home delivery service, the farm practices regenerative agriculture by rotating their cows, pigs, and turkeys to different pastures. All of the beef is grass-fed, leading to a leaner cut. The farm is also committed to education and transparency, offering free farm tours to their customers prior to the pandemic. After the pandemic struck, their membership doubled in just three weeks due to a higher demand for local, reliable, and sustainable food that could be delivered directly to people’s doorsteps.
The Challenge
Tara Firma Farms, a Bay Area farm and CSA known for their pasture-raised meats, experienced a sudden doubling of their home delivery membership due to the pandemic. This surge in demand presented a significant challenge for the farm, which was using outdated CSA management software with limited functionality. The software was better suited for smaller, produce-only CSAs and required manual intervention for tasks such as offering discounts or analyzing sales data. The farm was also in the process of replacing their CSA management software, adding to the stress of managing the increased demand. Additionally, the farm discovered that they were undercharging for delivery and some delivery routes were not profitable.
The Solution
To address these challenges, Tara Firma Farms replaced their old CSA management software with GetSwift’s SaaS eCommerce + Delivery software. This new platform provided valuable business insights, such as the realization that the farm was undercharging for delivery. As a result, the farm raised their delivery fee and required all new members to get at least one meat share, making the driver routes profitable. The new software also allowed for the creation of a beautifully designed eCommerce store, which became a one-stop-shop for high-end local products. The new routing functionality of the software enabled the farm to easily move a route from one night to another or add stops, optimizing routes automatically. The drivers could also update invoices or mark items returned from the road, all synced in real time.
Operational Impact
Quantitative Benefit
Case Study missing?
Start adding your own!
Register with your work email and create a new case study profile for your business.
Related Case Studies.
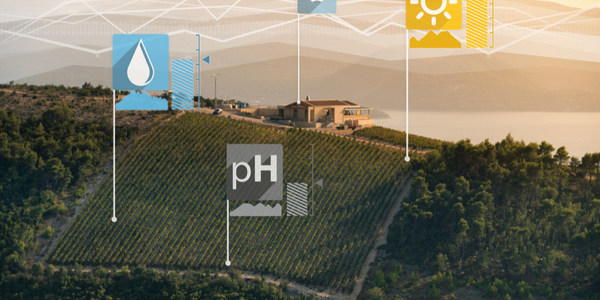
Case Study
Intelligent Farming with ThingWorx Analytics
Z Farms was facing three challenges: costly irrigation systems with water as a limited resource, narrow optimal ranges of soil moisture for growth with difficult maintenance and farm operators could not simply turn on irrigation systems like a faucet.
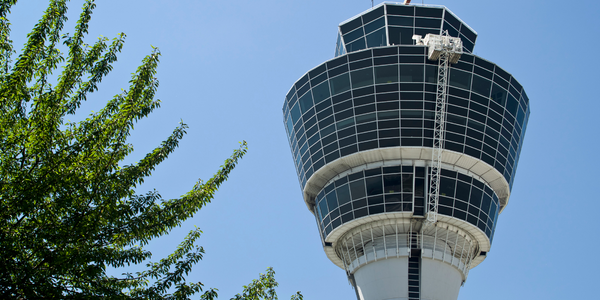
Case Study
Airport SCADA Systems Improve Service Levels
Modern airports are one of the busiest environments on Earth and rely on process automation equipment to ensure service operators achieve their KPIs. Increasingly airport SCADA systems are being used to control all aspects of the operation and associated facilities. This is because unplanned system downtime can cost dearly, both in terms of reduced revenues and the associated loss of customer satisfaction due to inevitable travel inconvenience and disruption.
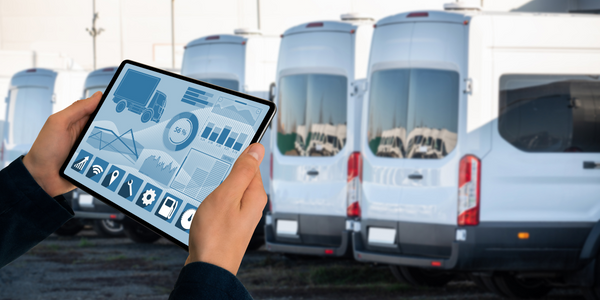
Case Study
IoT-based Fleet Intelligence Innovation
Speed to market is precious for DRVR, a rapidly growing start-up company. With a business model dependent on reliable mobile data, managers were spending their lives trying to negotiate data roaming deals with mobile network operators in different countries. And, even then, service quality was a constant concern.
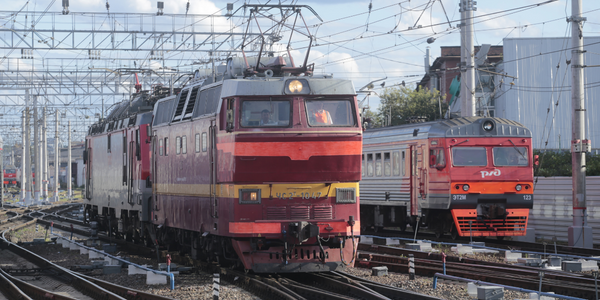
Case Study
Digitize Railway with Deutsche Bahn
To reduce maintenance costs and delay-causing failures for Deutsche Bahn. They need manual measurements by a position measurement system based on custom-made MEMS sensor clusters, which allow autonomous and continuous monitoring with wireless data transmission and long battery. They were looking for data pre-processing solution in the sensor and machine learning algorithms in the cloud so as to detect critical wear.