Customer Company Size
SME
Region
- America
Country
- United States
Product
- DocuWare
- IniTrack
Tech Stack
- Document Management System
- Claims Processing Software
Implementation Scale
- Enterprise-wide Deployment
Impact Metrics
- Cost Savings
- Productivity Improvements
- Customer Satisfaction
Technology Category
- Functional Applications - Enterprise Resource Planning Systems (ERP)
Applicable Industries
- Automotive
Applicable Functions
- Business Operation
- Sales & Marketing
Use Cases
- Asset Lifecycle Management
- Leasing Finance Automation
Services
- System Integration
- Software Design & Engineering Services
About The Customer
Randy Shepard & Associates, Inc., (RS&A) is a company that specializes in warranty claims processing for new car dealerships nationwide. They are dedicated to helping dealerships navigate the complexity of warranty administration. RS&A performs warranty claims processing by reviewing every claim for manufacturer compliance, applying proper codes, entering the data and ensuring the appropriate documentation is submitted to the manufacturer with each claim. They also handle correcting rejected claims and resubmitting them and provide their customers with claim payment confirmations. The company is based in New York, USA and has more than 165 clients submitting between 800 1,300 claims a day that range from 3 - 12 pages each.
The Challenge
Randy Shepard & Associates, Inc., (RS&A) specializes in warranty claims processing for new car dealerships nationwide. They handle warranty claims processing by reviewing every claim for manufacturer compliance, applying proper codes, entering the data and ensuring the appropriate documentation is submitted to the manufacturer with each claim. They also handle correcting rejected claims and resubmitting them and provide their customers with claim payment confirmations. However, managing these claims was time consuming especially if a document needed to be verified from a previous day or week. As their business grew, RS&A wanted to expedite their business process associated with processing paper documents, and make it faster and easier to locate any claim electronically.
The Solution
RS&A evaluated several systems, but chose to implement DocuWare because their Authorized DocuWare Partner was able to create a working prototype, provide superior technical support, and connected RS&A with another DocuWare customer who had successfully customized and deployed DocuWare. Today, most claims are received electronically. Each document is brought into IniTrack, indexed with dealer name, manufacturer name and claim number. Annotations are entered on an electronic layer over the document. The annotated information is then entered into the dealer’s computer system and sent to the manufacture for payment. DocuWare acts as the backend document storage archive for IniTrack. As supporting claim documentation arrives, it can be easily added to a claim in process. Staff members do not even need to open DocuWare as a separate program because of its tight integration, allowing them to work in their familiar IniTrack program.
Operational Impact
Quantitative Benefit
Case Study missing?
Start adding your own!
Register with your work email and create a new case study profile for your business.
Related Case Studies.
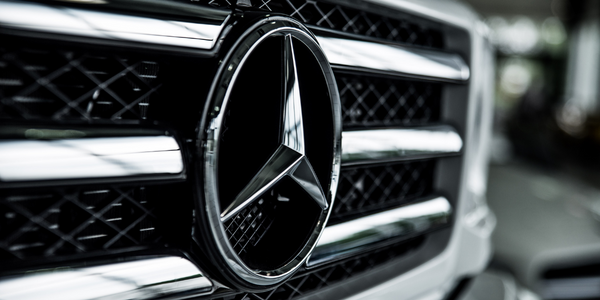
Case Study
Integral Plant Maintenance
Mercedes-Benz and his partner GAZ chose Siemens to be its maintenance partner at a new engine plant in Yaroslavl, Russia. The new plant offers a capacity to manufacture diesel engines for the Russian market, for locally produced Sprinter Classic. In addition to engines for the local market, the Yaroslavl plant will also produce spare parts. Mercedes-Benz Russia and his partner needed a service partner in order to ensure the operation of these lines in a maintenance partnership arrangement. The challenges included coordinating the entire maintenance management operation, in particular inspections, corrective and predictive maintenance activities, and the optimizing spare parts management. Siemens developed a customized maintenance solution that includes all electronic and mechanical maintenance activities (Integral Plant Maintenance).
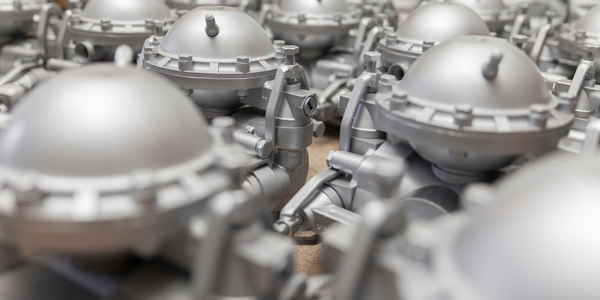
Case Study
Monitoring of Pressure Pumps in Automotive Industry
A large German/American producer of auto parts uses high-pressure pumps to deburr machined parts as a part of its production and quality check process. They decided to monitor these pumps to make sure they work properly and that they can see any indications leading to a potential failure before it affects their process.