Customer Company Size
Large Corporate
Region
- Europe
Country
- Switzerland
- Italy
Product
- HPE SimpliVity
- HPE InfoSight
- HPE iLO Advanced
Tech Stack
- SQL Server database engine
- VMware
Implementation Scale
- Enterprise-wide Deployment
Impact Metrics
- Productivity Improvements
- Cost Savings
Technology Category
- Infrastructure as a Service (IaaS) - Cloud Computing
- Infrastructure as a Service (IaaS) - Cloud Storage Services
Applicable Functions
- Discrete Manufacturing
- Quality Assurance
Use Cases
- Manufacturing System Automation
- Predictive Maintenance
Services
- Cloud Planning, Design & Implementation Services
- System Integration
About The Customer
Noyfil, which has been on the market for almost 50 years, now specializes in the production of continuous polyester yarn. Based in Stabio, in the Swiss canton of Ticino, the company is part of the Fibers Area of the RadiciGroup, an Italian multinational that aims to offer a diversified range of products with a reduced environmental impact in the yarn sector and contribute to the revival of the textile and fashion industry, one of the sectors hardest hit by the pandemic, in the name of the circular economy. Noyfil, a production company located in Switzerland, produces specialized yarns made with special additives using new technological developments in a well-established polyester fiber market. This all begins with an increasing volume of recycled polyester fibers made using post-consumer bottles or plastics/microplastics recovered from lakes and seas. The company uses the pellets formed from crushed bottles to produce the polymer in-house, and then spins it into thousands of different colors with special properties such as anti-bacterial, anti-UV, and flame-retardant, used in weaving and clothing to prevent fabrics from catching fire. In addition to promoting recycling, the company strives to reduce waste in production processes and use alternative sources of energy in accordance with the Group's strategy. RadiciGroup is involved in multiple areas of production, working with a variety of materials including chemicals, technopolymers, fibers, and nonwovens. It has 3,000 employees in 15 countries around the world, 100 of whom are employed at the Noyfil plant; the Group closed the 2020 financial year with consolidated sales of EUR 1,019 million.
The Challenge
Noyfil, a company specializing in the production of continuous polyester yarn, was looking to overhaul its application support infrastructure to enhance the management of its special yarn production process. The company was keen to break away from the typical approach in the manufacturing sector, where there is a tendency to adopt the “if it ain’t broke, don’t fix it” mentality. The rationale for this attitude is the level of investment—which can run into the millions—that is required when upgrading production facilities, which have a much longer service life than IT infrastructures, which need to be replaced before they become obsolete. However, with relatively moderate investments, it is possible to achieve a quantum leap in performance and ease of management.
The Solution
With the support of its partner 4IT Solutions, the company's IT department carried out an analysis of what the market was offering, with a particular focus on HPE products, which had performed well in various areas (from servers to switches). Noyfil ultimately went with HPE SimpliVity, a solution already adopted by another company in the Group (Radici Chimica), which instantly made it possible to go from the previous five machines to two hyperconverged servers with internal disks. The reduction in hardware alone has simplified the whole operation, reduced the possibility of disruption, and led to fewer aspects to be managed. Instead of using one server for the VMware component and another (with a different program) for the storage aspect, a single access point was created from which the storage servers, network, backups, etc., can be managed. The transition from virtual storage based on mechanical disks to the HPE SimpliVity all-flash approach also triggered an immediate improvement in performance. A potential future development would be to boost reliability by creating a second room where one of the two servers could be relocated or, alternatively, to procure a third server, which Ubertis hopes would be based remotely, to be used as a basis for replication and developing a disaster recovery plan.
Operational Impact
Quantitative Benefit
Case Study missing?
Start adding your own!
Register with your work email and create a new case study profile for your business.
Related Case Studies.

Case Study
Remote Monitoring & Predictive Maintenance App for a Solar Energy System
The maintenance & tracking of various modules was an overhead for the customer due to the huge labor costs involved. Being an advanced solar solutions provider, they wanted to ensure early detection of issues and provide the best-in-class customer experience. Hence they wanted to automate the whole process.
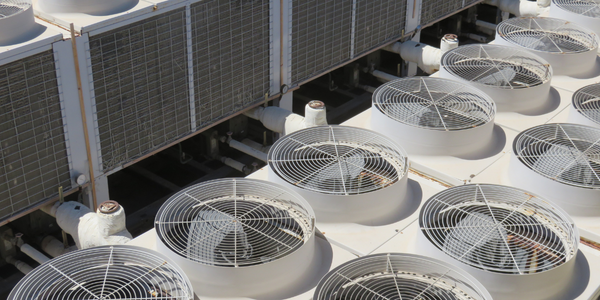
Case Study
Predictive Maintenance for Industrial Chillers
For global leaders in the industrial chiller manufacturing, reliability of the entire production process is of the utmost importance. Chillers are refrigeration systems that produce ice water to provide cooling for a process or industrial application. One of those leaders sought a way to respond to asset performance issues, even before they occur. The intelligence to guarantee maximum reliability of cooling devices is embedded (pre-alarming). A pre-alarming phase means that the cooling device still works, but symptoms may appear, telling manufacturers that a failure is likely to occur in the near future. Chillers who are not internet connected at that moment, provide little insight in this pre-alarming phase.
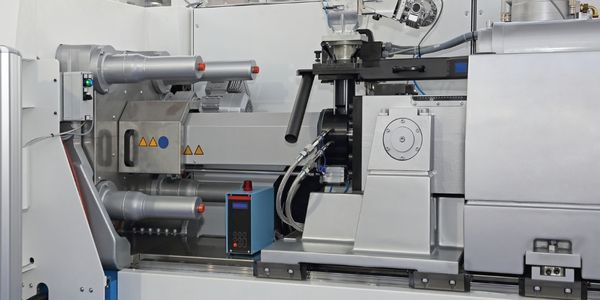
Case Study
Plastic Spoons Case study: Injection Moulding
In order to meet customer expectations by supplying a wide variety of packaging units, from 36 to 1000 spoons per package, a new production and packaging line needed to be built. DeSter wanted to achieve higher production capacity, lower cycle time and a high degree of operator friendliness with this new production line.
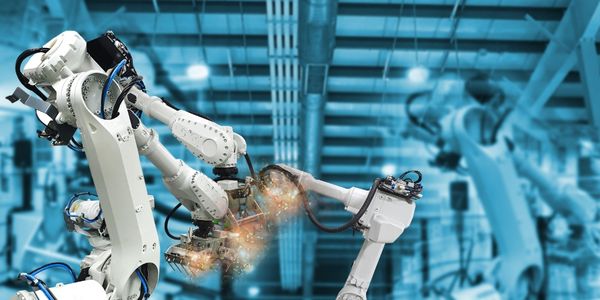
Case Study
Robot Saves Money and Time for US Custom Molding Company
Injection Technology (Itech) is a custom molder for a variety of clients that require precision plastic parts for such products as electric meter covers, dental appliance cases and spools. With 95 employees operating 23 molding machines in a 30,000 square foot plant, Itech wanted to reduce man hours and increase efficiency.
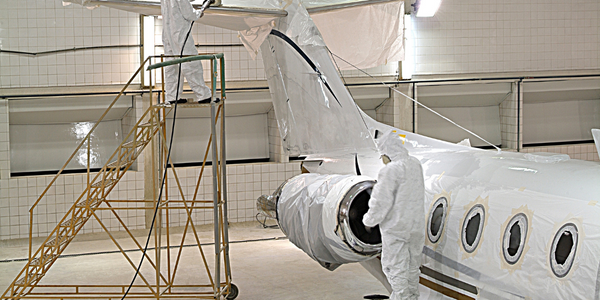
Case Study
Aircraft Predictive Maintenance and Workflow Optimization
First, aircraft manufacturer have trouble monitoring the health of aircraft systems with health prognostics and deliver predictive maintenance insights. Second, aircraft manufacturer wants a solution that can provide an in-context advisory and align job assignments to match technician experience and expertise.
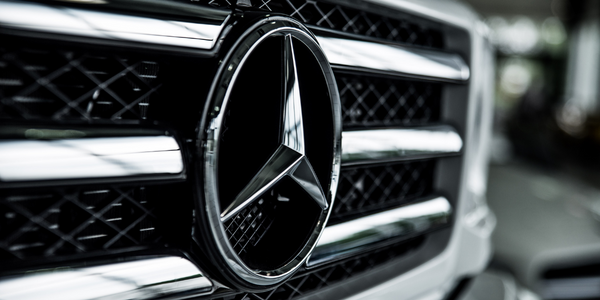
Case Study
Integral Plant Maintenance
Mercedes-Benz and his partner GAZ chose Siemens to be its maintenance partner at a new engine plant in Yaroslavl, Russia. The new plant offers a capacity to manufacture diesel engines for the Russian market, for locally produced Sprinter Classic. In addition to engines for the local market, the Yaroslavl plant will also produce spare parts. Mercedes-Benz Russia and his partner needed a service partner in order to ensure the operation of these lines in a maintenance partnership arrangement. The challenges included coordinating the entire maintenance management operation, in particular inspections, corrective and predictive maintenance activities, and the optimizing spare parts management. Siemens developed a customized maintenance solution that includes all electronic and mechanical maintenance activities (Integral Plant Maintenance).