Technology Category
- Cybersecurity & Privacy - Security Compliance
- Other - Battery
Applicable Industries
- Automotive
- Education
Applicable Functions
- Maintenance
- Quality Assurance
Use Cases
- Leasing Finance Automation
- Virtual Training
Services
- System Integration
- Training
About The Customer
ZEVx is a US-based company on a mission to provide the most energy and economically-efficient electrification kits for commercial fleets. They develop e-mobility battery packs and powertrain solutions for light and medium-duty fleet vehicles. Their customers and partners, who are spread across the United States, are involved in converting vehicles and may also have to perform maintenance on the repowered vehicles. These customers and partners need to be trained on the installation and maintenance processes, and they also need to comply with industry-specific regulations. ZEVx is committed to helping other companies transition to e-mobility.
The Challenge
ZEVx, a US-based company that develops e-mobility battery packs and powertrain solutions for commercial fleets, was facing a challenge in building a training program for their customers and partners. These individuals, in addition to converting vehicles, may also have to perform maintenance on the repowered vehicle. The company, headquartered in Arizona, serves customers all over the United States, many of whom are in different time zones. This geographical spread added to the complexity of delivering consistent and effective training. ZEVx needed a solution to document all the required steps for those performing vehicle conversions and maintenance, with a focus on improving the customer experience. They also needed to demonstrate compliance with industry-specific regulations, such as those imposed by the California Air Resources Board (CARB).
The Solution
ZEVx found its solution in SwipeGuide, a platform that made it easy to build a training program for their customers and partners. SwipeGuide's features for PDF conversion sped up instruction authoring time, and its ability to provide a detailed overview of the steps and materials used in the electrification process helped ZEVx demonstrate compliance with industry-specific regulations. Using SwipeGuide, ZEVx was able to provide user-friendly powertrain installation instructions and guidance for critical maintenance tasks on converted vehicles. These instructions were accessible on mobile devices in a step-by-step format, eliminating the need to sift through word documents or PDFs. SwipeGuide's intuitive UI, drag & drop content creation, and optimized structure improved the way ZEVx created and managed training materials and standards across their value chain. ZEVx operators also made use of SwipeGuide's PDF conversion tool to speed up instruction authoring and creation time.
Operational Impact
Quantitative Benefit
Case Study missing?
Start adding your own!
Register with your work email and create a new case study profile for your business.
Related Case Studies.
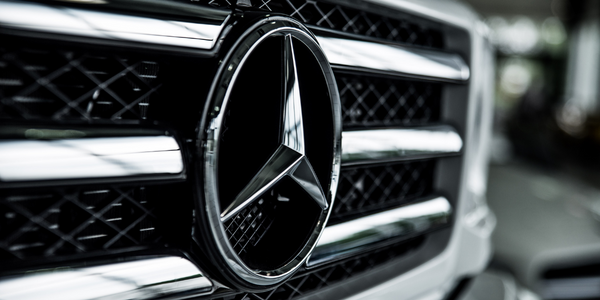
Case Study
Integral Plant Maintenance
Mercedes-Benz and his partner GAZ chose Siemens to be its maintenance partner at a new engine plant in Yaroslavl, Russia. The new plant offers a capacity to manufacture diesel engines for the Russian market, for locally produced Sprinter Classic. In addition to engines for the local market, the Yaroslavl plant will also produce spare parts. Mercedes-Benz Russia and his partner needed a service partner in order to ensure the operation of these lines in a maintenance partnership arrangement. The challenges included coordinating the entire maintenance management operation, in particular inspections, corrective and predictive maintenance activities, and the optimizing spare parts management. Siemens developed a customized maintenance solution that includes all electronic and mechanical maintenance activities (Integral Plant Maintenance).
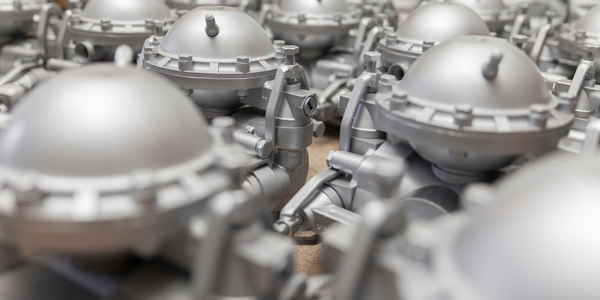
Case Study
Monitoring of Pressure Pumps in Automotive Industry
A large German/American producer of auto parts uses high-pressure pumps to deburr machined parts as a part of its production and quality check process. They decided to monitor these pumps to make sure they work properly and that they can see any indications leading to a potential failure before it affects their process.