Technology Category
- Application Infrastructure & Middleware - Event-Driven Application
- Cybersecurity & Privacy - Identity & Authentication Management
Applicable Industries
- Construction & Infrastructure
- Equipment & Machinery
Applicable Functions
- Maintenance
- Quality Assurance
Use Cases
- Experimentation Automation
- Visual Quality Detection
Services
- System Integration
- Testing & Certification
About The Customer
andagon GmbH is a renowned consulting company in the field of quality assurance, specializing in software testing, process and test automation. Headquartered in Cologne, Germany, andagon employs more than 50 quality experts. The company has developed aqua, a comprehensive software solution designed to improve application lifecycle management by integrating quality management into IT project management. aqua revolutionizes the software business processes in IT projects by enrolling all parties in the process: business users, project leaders, analysts, developers and testers, and creates more transparency through improved control and communication – including internationally-distributed teams. The company’s consultants help customers across multiple sectors to implement test automation and quality assurance processes including functional testing and performance testing. For those customers developing and using SAP applications, andagon offers a comprehensive range of tailored testing services designed to optimize performance and reliability.
The Challenge
andagon GmbH, a renowned consulting company specializing in software testing, process and test automation, often encounters clients who have identified quality issues or performance bottlenecks during the implementation phase of their applications. These clients turn to andagon to analyze the difficulties and develop a customized test plan to efficiently address the performance issues. In typical commercial environments, software testing is often delayed until the end of a project, increasing the pressure on the testing team and process. To assess the performance of a complex application quickly and effectively, efficient tools are required to create and execute the relevant test cases. Thousands of companies rely on SAP software to run their core business processes, and need to make sure that application errors do not disrupt business operations. Particularly for manufacturing companies, system downtime can cause significant financial damage. If software quality and performance issues are spotted at a late stage in a development project, the costs and delays incurred by corrective work damages companies’ abilities to reach their goals.
The Solution
andagon advises its customers to integrate testing into general development processes to monitor software quality throughout the project and avoid discovering functional or performance issues at the end of an implementation. As an IBM Business Partner, andagon is a strong advocate of the comprehensive IBM toolset for application development and testing. IBM Rational Performance Tester provides a broad range of features to enable efficient performance testing, and helps to identify application architecture and infrastructure bottlenecks. A simple graphical user interface allows for the creation of test cases without the need to write code, and integrated test data management enables flexible and dynamic customization of test cases. IBM Rational Performance Tester automatically executes tests with dynamically generated test data, and tracks the dynamic data throughout the tests to ensure that correct, useful test results are generated. IBM Rational Performance Tester uses flexible IBM Rational Performance Tester Agents to generate the performance test load. The load test agents emulate user behavior to generate a workload that is as similar as possible to real users.
Operational Impact
Quantitative Benefit
Case Study missing?
Start adding your own!
Register with your work email and create a new case study profile for your business.
Related Case Studies.
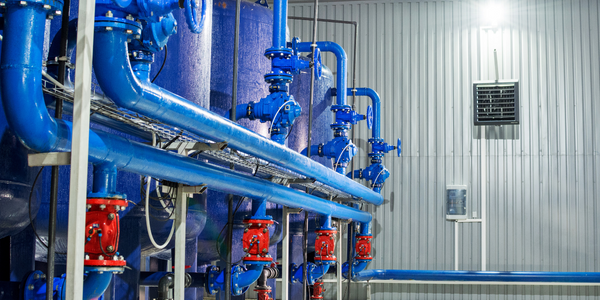
Case Study
Smart Water Filtration Systems
Before working with Ayla Networks, Ozner was already using cloud connectivity to identify and solve water-filtration system malfunctions as well as to monitor filter cartridges for replacements.But, in June 2015, Ozner executives talked with Ayla about how the company might further improve its water systems with IoT technology. They liked what they heard from Ayla, but the executives needed to be sure that Ayla’s Agile IoT Platform provided the security and reliability Ozner required.
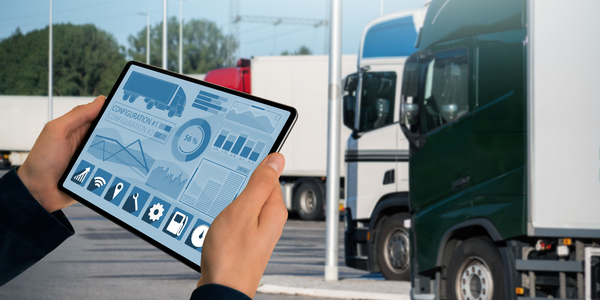
Case Study
IoT enabled Fleet Management with MindSphere
In view of growing competition, Gämmerler had a strong need to remain competitive via process optimization, reliability and gentle handling of printed products, even at highest press speeds. In addition, a digitalization initiative also included developing a key differentiation via data-driven services offers.
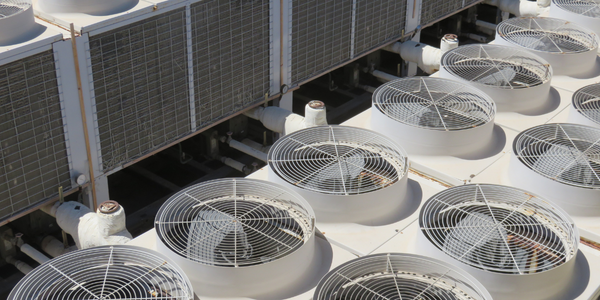
Case Study
Predictive Maintenance for Industrial Chillers
For global leaders in the industrial chiller manufacturing, reliability of the entire production process is of the utmost importance. Chillers are refrigeration systems that produce ice water to provide cooling for a process or industrial application. One of those leaders sought a way to respond to asset performance issues, even before they occur. The intelligence to guarantee maximum reliability of cooling devices is embedded (pre-alarming). A pre-alarming phase means that the cooling device still works, but symptoms may appear, telling manufacturers that a failure is likely to occur in the near future. Chillers who are not internet connected at that moment, provide little insight in this pre-alarming phase.
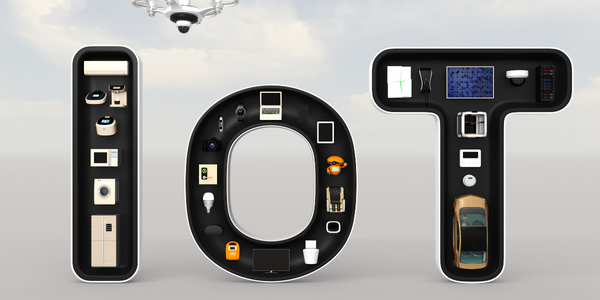
Case Study
Premium Appliance Producer Innovates with Internet of Everything
Sub-Zero faced the largest product launch in the company’s history:It wanted to launch 60 new products as scheduled while simultaneously opening a new “greenfield” production facility, yet still adhering to stringent quality requirements and manage issues from new supply-chain partners. A the same time, it wanted to increase staff productivity time and collaboration while reducing travel and costs.
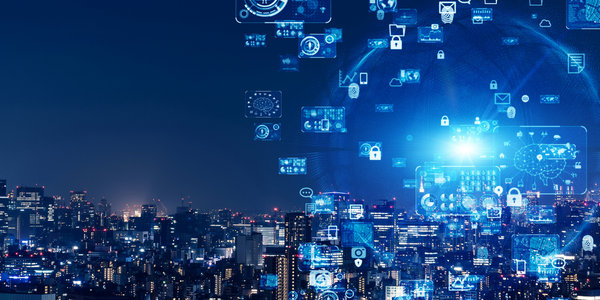
Case Study
Integration of PLC with IoT for Bosch Rexroth
The application arises from the need to monitor and anticipate the problems of one or more machines managed by a PLC. These problems, often resulting from the accumulation over time of small discrepancies, require, when they occur, ex post technical operations maintenance.
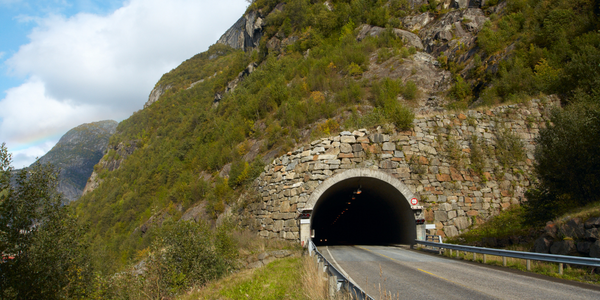
Case Study
IoT System for Tunnel Construction
The Zenitaka Corporation ('Zenitaka') has two major business areas: its architectural business focuses on structures such as government buildings, office buildings, and commercial facilities, while its civil engineering business is targeted at structures such as tunnels, bridges and dams. Within these areas, there presented two issues that have always persisted in regard to the construction of mountain tunnels. These issues are 'improving safety" and "reducing energy consumption". Mountain tunnels construction requires a massive amount of electricity. This is because there are many kinds of electrical equipment being used day and night, including construction machinery, construction lighting, and ventilating fan. Despite this, the amount of power consumption is generally not tightly managed. In many cases, the exact amount of power consumption is only ascertained when the bill from the power company becomes available. Sometimes, corporations install demand-monitoring equipment to help curb the maximum power demanded. However, even in these cases, the devices only allow the total volume of power consumption to be ascertained, or they may issue warnings to prevent the contracted volume of power from being exceeded. In order to tackle the issue of reducing power consumption, it was first necessary to obtain an accurate breakdown of how much power was being used in each particular area. In other words, we needed to be able to visualize the amount of power being consumed. Safety, was also not being managed very rigorously. Even now, tunnel construction sites often use a 'name label' system for managing entry into the work site. Specifically, red labels with white reverse sides that bear the workers' names on both sides are displayed at the tunnel work site entrance. The workers themselves then flip the name label to the appropriate side when entering or exiting from the work site to indicate whether or not they are working inside the tunnel at any given time. If a worker forgets to flip his or her name label when entering or exiting from the tunnel, management cannot be performed effectively. In order to tackle the challenges mentioned above, Zenitaka decided to build a system that could improve the safety of tunnel construction as well as reduce the amount of power consumed. In other words, this new system would facilitate a clear picture of which workers were working in each location at the mountain tunnel construction site, as well as which processes were being carried out at those respective locations at any given time. The system would maintain the safety of all workers while also carefully controlling the electrical equipment to reduce unnecessary power consumption. Having decided on the concept, our next concern was whether there existed any kind of robust hardware that would not break down at the construction work site, that could move freely in response to changes in the working environment, and that could accurately detect workers and vehicles using radio frequency identification (RFID). Given that this system would involve many components that were new to Zenitaka, we decided to enlist the cooperation of E.I.Sol Co., Ltd. ('E.I.Sol') as our joint development partner, as they had provided us with a highly practical proposal.